This presentation was developed for the Advanced Screen Printing Workshop organized by Asada Mesh. The theme was fineline printing. In this presentation, we discuss the following:
Existing and future applications for ever finer Screen Printing Linewidths (sub-15micron meters).
Photovoltaic metallization
MicroLED wrap-around edge electrodes
Fan-out structure for flexible hybrid electronics
Transparent HMIs
Transparent Touch Displays
Edge Electodes
MLLC
LTCC
Hybrid and direct (non-digital) printing technologies towards sub-micron linewidths
Hybrid screen printing (print + etch/ablate)
R2R flexoprinting
R2R Gravure Offset PRinting
S2S Offset Printing
S2S Reverse Offset Printing
R2R Reverse Offset Printing
R2R Imprinting + Filling
R2R Photolithgraph
You can download the slides at the end. Please scroll down
This is an automatic transcription of the full presentation. It has not been proof read so there may be errors. This is here to help in case you prefer to read
Hello, everyone. My name is Kasha. I am the CEO of TechBlick. We are really the home of the global community for additive electronics, for printed flexible hybrid electronics, 3D electronics. And we provide our community members a year round programme of curated onsite and online conferences and masterclasses market studies and beyond.
The presentation itself has two parts. So the first part. The presentation will be looking at applications which will benefit or which will require ever finer screen printed line width. And then the second part of the presentation will be looking at non digital printing techniques, hybrid and directly or fully additively printed techniques which allow one to take the linewidth from, let's say, 30 or 40 micrometers down to a few micrometers and then eventually to sub micrometer range.
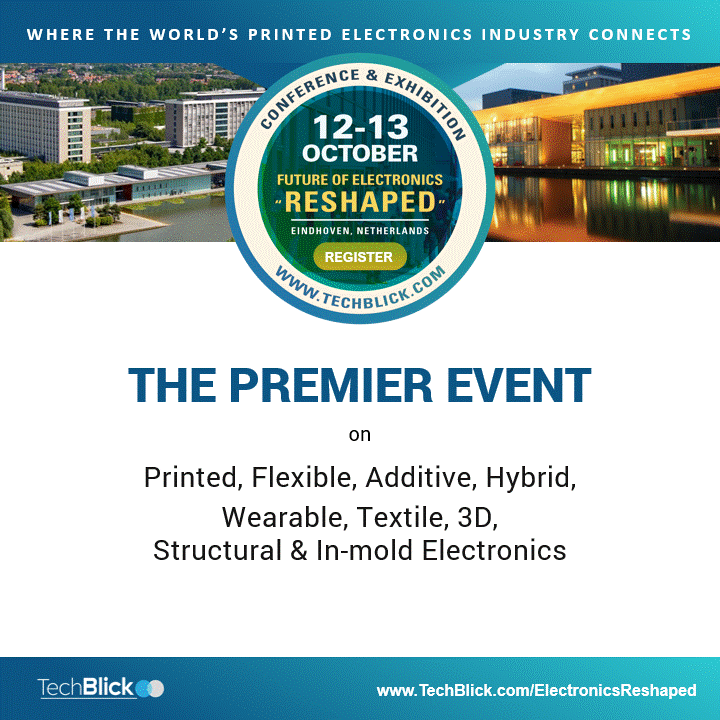
Photovoltaics So first, as I mentioned, we are going to look at applications which require or which will benefit from ever finer screen printed line widths and the first. Important application is, of course, silicon photovoltaics is, you know, one of the biggest applications for conductive inks and for screen printing in electronics is metallization of silicon PV wafers. And if you look at this chart here, if you look at the orange lines, what you find is that is the line width of the printed metal mesh as the printed metallization. You can see the current state of production today is something around 34 to 36 micrometers today and it is coming down very, very fast. So it is expected that within a few years we'll be reaching 20 micrometer line widths and maybe even lower. What is also interesting about this application is that screen printing is actually a very, very productive process. So here you can see the wafer per hour rate for the back end processes, which also include the metallization step screen printing. The wafer size is something around 180 to 182 millimeters. And you can see that today we are something around 7000 wafers per hour. And this is projected to rise to something around, let's say, 10,000 wafers per hour by the end of the year. So you already have screen printing in this very productive high volume production setting, producing, you know, 30 to 35 micrometer linewidths and evolving the process down to 20 micrometer line width. And here on the left, you can see an example of what I think is a very good representation of the state of the art. And here you can see a screen printed sort of finger on a perc solar cell. This was made by Fraunhofer ISE. And you can see very nice, with 19 micrometers and a very nice aspect ratio of about 18-19micrometers. And so yeah, I mean that, that already tells you that there is an application in high volume production which has narrow language in the line which will go down to 20 micrometers and beyond. But I want to say that solar metallization is really relatively an easy application, and that is because the pitches are very wide and at the same time broken lines, interrupted lines, can to some extent be tolerated. So there is some tolerance of defects. MicroLEDs Another application which I think would benefit as an example for ever finer screen printing metallization lines is the Micro-led display application, so microLEDs are a very hot display topic. And one of the key uniques of this display technology is that you can create bezel free displays. So when you have bezel free displays, it means that you can form a larger display by putting together many kind of smaller tiles and building up the big display. So here you can see an example of one such display tile. So we have glass and on this you deposit the TFT, the thin film electronics on the glass. You might deposit the the bonds, the micro bonds or something, and then you transfer the micro LEDs on the top. the driverwould be on the bottom. So first you can imagine that the two surfaces on the top have to be metallized (see the lines on the top surface). You have to realize the lines on the bottom surface, connecting them to the pins on the driver. And then you have to somehow connect the front to the back. And one way, of course, would be to drill via into the glass, fill the through glass vias. But this is really not elegant. And as far as I know, nobody uses this process. So a more interesting approach would be to create this so-called wraparound edge electrodes. So you would have these electrodes going around the edge connecting the front to the back. So this example, I believe, is from Applied Materials, and this one is from Corning. Here is an example again by Applied Materials showing you the kind of process so that the front metallization would be printed on a chamfered glass. Then the bottom metallization would be screen printed on the chamfered glass, and then the glass would be rotated to print the edge electrode and then cure. So first you need very good alignment. You need very, very highly conductive inks and you need to control your printing process so that you don't end up with peaks around at the chamfered edge of the glass. Here's an example where the chamfered edge, the example on the on the bottom left, you need to have a topography of a printed line which is relatively smooth, with no major peaks around the edges. And then the thickness would be for a given connectivity level of inks something around 3 to 6 micrometers after drying. So here you can see an example of fine line printed, a screen printing also around the edges and the line width of the spacing is 40 to 60 micrometers in this case. So already this is by some standards very, very fine line screen printing. But perhaps this is the technology of yesterday? And the reason I mentioned this is because micro led dies are shrinking in size. So the early generations were actually mini LEDs with the dies being something around 125 by 225 micrometer size. And now we are going down, and this chart is put together by, Yole and you can see that we'll be going into a territory where the dies are something around maybe ten micrometers by ten micrometers. And as we approach that range, the bond sizes are going to get smaller and also the metallization lines are going to get ever, ever narrower, which means that the screen printing, if screen printing is to stay competitive in this technology, it also has to produce ever finer lines. And so here's an example again by Applied Materials. I think you can't see it in the recording because my video is here, but this is a 15 micrometer printed screen printed line. So it shows you that you can print that level. And I'm sure all of you in this expert audience know this, that one can print 15 micrometers, but this application is not like a PV application. It is very challenging. It cannot tolerate broken interrupted lines because that would imply a dead microleds and therefore a dead pixel. And in the worst case, you might be able to tolerate some defects on 10% of the tiles, but on 90% of the tiles, all the metallization, have to be defect free. So not only one needs to deposit very, very fine lines with good control of topography, high conductivity, good wraparound coverage. But also one needs to do so without too many broken lines. So this is a challenge for the industry and I think this workshop would help the industry achieve these targets. I should say here that the competition actually here is actually one of the competitions here is PVD and Samsung uses a PVD process developed by a Korean company in which in the PVD chamber they stack all the glasses together and then they rotate them and they get PVD to deposit also around the edges. So PVD is always, always the competition in these cases. But if screen printing could produce fine lines, 15 micrometers or less without defects, maybe this could be with very little defects. Screen printing would remain competitive in this application. Flexible Hybrid Electronics (fan-out) So another application that I wanted to highlight, and I think it's an interesting one, is around flexible hybrid electronics. So flexible hybrid electronics is about combining the performance of rigid ICs, rigid silicon ICs with the low cost production and the flexibility of printed flexible electronics on low temperature substrates like PET. And I think many of the technology hurdles which have held back this technology are being cleared away now. So people are developing ways to use standard solders or developing materials with solder like properties, i.e. self alignment on heat or on other low temperature substrates. People are finding ways to thin ICs and make them flexible. People are finding ways to do pick and placing of these very thin ICs, sometimes even in a roll to roll set up. So many of the technology hurdles are being cleared. And the reason I have it here in this screen printing workshop is because I think screen printing could also play a role here, at least fine line screen printing could play a role. So look at this example here. This is, I think a demonstrator by Nexflex, you have the IC here, you have the wiring lines printed. Let's say the wiring lines can typically be screen printed. The pitches are wide. The linewidth is well within what screen printing can do. Then one needs to go from the wiring to the ICs. So in the pictures, the pins of the ICs are much narrower than the wiring. So one needs to have this so-called fan-out structure connecting the pins with the bumps and connecting the pins to the actual wiring. And here's an example of a fan-out structure. So right now, screen printing cannot do the wiring and the final structure just based on the screen printing process. So different processes have to be combined. But what I think if fine line screen printing would be further advanced, then this would be possible to screen print the fan-out as well as the wiring and the requirements for the line width of the fan out is something around 30 microns or less with a pitch of around 60 microns or less. So this particular image is from Netflix and some of these images I took from a presentation by Komori in Japan and adapted them just for reference. Transparent HMIs So I wanted to also say a few words about this very interesting application for Transparent Touch or HMIs. I mean, here the competition is maybe trying to replace PEDOT transparent dot layer, which is also printed in very high volumes. But in this case, in the case of these metal mesh structures, one maybe does not need a protective layer. Simplifying the structure and making it also thinner. This example is by sSun Chemical as other mesh type, CFR and others. So this is a well known example in this audience that actually I think Erika will have presented on this. . So I won't I won't discuss this particular application. But just to say the linewidths, I think, are around 30 or 35 micrometers, so you can see the meshes, but it is probably okay for these switch or HMI applications, but. Say that, you know, the requirements for a transparent touch display are very different from the requirements for a transparent switch. Transparent Touch Displays So when we talk about a transparent display like on your phone or on your tablet, then the line width needs to be a lot narrower. So here you can see an example of the kind of the different ranges to micrometer range for me, so sorry. So maybe let me explain this again. So here you can see the ranges. If your linewdith is wider than 4 to 5 micrometers, it is possible to see the structure even though it is transparent. If the line width is around 2 to 4 or five micrometers, then it is very difficult to see. But if one looks very, very carefully, one can sense. I can recognize that something is there and if it's below two micrometers, probably it's totally invisible. And I just want to show you in this table what companies are doing, what kind of line widths they are printing for the metal meshes, which act as a transparent conductive field for display industry. So these are different companies. These are different processes. I won't go into the processes in this presentation, but just look at this column here showing the line width. So one can clearly see that the line widths are generally sub four micrometers and that shows you the requirement for this industry. So I just have this slide here to kind of make a contrast between transparent touch displays and transparent touch switches. Edge Electrodes Now another interesting application. I think if if screen printing could print ever finer lines, then screen printing would stay would have stayed relevant in this application and would be very competitive process that is for printing the edge electrodes in a transparent touch display. So here you can see an example of a kind of an edge electrode series. The requirements because the bezels have been getting narrower and narrower, the line width to spacing requirements have also shrunk over time. So I have here two examples of companies offering a full, transparent film structure, including the transparent layer and the edge electrodes. And here you can see the line with over the spacing in micrometers of just the edge electrode just to give you a sense of what kind of requirements people have. So if screen printing is to stay relevant, it needs to target sub 15 or so, maybe at least sub 20 micrometer micrometer range And here is a kind of an evolution chart. Very rough, very, very, very approximate chart showing line with over the spacing requirements. Standard screen printing maybe takes you down to 40, 50, 40 micrometers then fine down screen printing. So screen printing technologies which are being developed now and together with the ones that are the subject of this workshop, maybe take you down to 20-15 micrometers, then people start to use hybrid processes. So I'll give you an example later on screen printing plus laser plus photolithography. And then there are other non-screen printing techniques which are put here in green. So all the blue ones are either direct or hybrid screen printing and the other ones are non screen printing processes. So basically I guess the message here is that if screen printing could do very fine lines, then it would be able to participate in this market. Also printing the electrodes for transparent touch display. Other Applications (MLLC, LTCC, etc) So. We want to focus on alternative technologies. So so far in the application area, we talked about photovoltaic metallization and how the line width will go to 20 micrometers or below with very, very high wafer per hour throughputs. We looked at the microgrid application and how the requirements there are moving towards 15 micrometer line width and below, but with very exacting sort of defect and yield requirements. We looked at flexible hybrid electronics and how it might benefit from printing the wiring or screen printing the wiring and also screen printing the fan out. We then said a few words about transparent light switches, transparent type screens, edge electrodes. And before going to the alternative technologies, I just want to mention maybe a couple of applications which I omitted in my presentation but are very important. One of them is MLC, where nickel powders are screen printed. Maybe some do gravure printing, maybe 30% or so do gravure printing for the mobile application, but the majority are still screen printed and will remain so. And the reason I mentioned this is because the thickness of the lines is going down and down. And I think now it's between 1 to 2 micrometers, the thickness of the final line and the other application is LTCC. LTCC is, I think, a very competitive technology for 5G. And when you think about 5G and LTSC as a substrate technology and if you think about heterogeneous integration of different ices in an LTC kind of a system, then one needs to have very, very fine line printing techniques with very good edge definition to support 5G lines and also very, very narrow, narrow printed lines. I think they are also the requirements would be very soon about 15, 15 micrometers. Technologies Towards sub-Micron Printing So in the next few slides, what I want to do is I want to tell you about technologies which allow you to go to find very fine lines, sub micrometer or micrometer range. So we'll look at screen printing plus photolithography. We look at role of flexible printing, we look at gravure offset printing, sheet to sheet offset, reverse offset and so on. And basically you will see how we go towards ten micrometers and then we go to sub ten and sub five and sub three and then in some cases sub one micrometer. Hybrid Screen Printing So just two quick, quick, quick slide on this one. So this is a hybrid screen printing process. The idea is that the ink itself in this case contains a photosensitive material. So you don't need a photoresist. So as you can see here, you can screen, print it and then expose it to UV light directly with the photoresist and then etch. And then this will allow you to get very, very fine lines. So in this case, this material is Toray. the references are behind my behind my image. So this is my Japanese company. And these examples, this example here is linewidth over a spacing of about about ten, ten by ten micrometers. This is for curing for 140 degrees Celsius. So compatible with PET substrates. But I think what is important here is that the conductivity of the line is not very high because you also are loading other additives into the formulation. If you want a higher temperature version that is compatible with PI or glass, then you can adjust the process and go to even finer lines. 2.45 micrometers or eight eight micrometers. So that was a hybrid screen printing process, a screen print plus etch. R2R Flexo Printing In this case, I want to talk about a direct, flexible printing process. Of course, flexible prints, thin lines, just just how it is. And this case is developed by Kodak, who has a very good laser process for creating the plates with flat top dots. And they created a metal mesh here. This is a semi additive process where they flexo print a catalyst layer and then they use plating to thicken the layer and achieve bulk like conductivity. And if you look at these metal meshes here, the only reason I have it here is that the linewidth can be around eight eight micrometers. So it shows you that with this technique one can go down to sub10 micrometers. R2R Gravure Offset Here is an example of road roll gravure offset printing being developed for a number of years in Japan. And I don't want to go into the details of the actual technology, but you can see a kind of the narrow web tools which are being developed now. The web speed is relatively, relatively low, but here I think they print with submicron particles. So let's say a nanoparticle ink is used to print these metal mesh lines and you can see that the lines are five micrometers. S2S Offset Printing Another example which I liked again by a Japanese company. This time you can see the name here. And the reason I like this here is that this is a sheet to sheet offset printing process. And you can see they can print these very, very complex patterns with just 1.5 micrometer linewidth. And here, too, they're using silver nanoparticles. You can see it's a very thin line, maybe 250 nanometer just thickness cured at low temperature. So you can cure the ink at 120 to 400 degrees Celsius. But the reason I basically have it here is that this shows you that with direct printing sheet sheet on various substrates, as long as it is sheet to sheet, one can achieve 1.5 or three three micrometers. S2S Reverse Offset Process Then if you want to go below that level and achieve kind of one micrometers, then I think an interesting sort of process is the reverse is the reverse offset process. Here you can see an example by. This was, I think, published recently and showcased at our conference just in March at the TechBlick show. And you can see a kind of a desktop reverse offset printing machine. Reverse offset printing technique is very unique because you usually have a PDMS roller mold, you totally ink it, so it's totally covered with ink. Then the ink semi absorbs into the PDMS, which means that you're not dealing with a complete liquid, but because it is in a semi dried state, then you can control the wetting a little bit better and then it is brought into contact with the relief plate. Some of the patterns are removed, removed, and then the roller mold is brought into contact with the final substrate and then the ink is transferred. So you can see that in this case, they have developed a process. They have developed a process which allows them to create metal meshes with just, just one micrometer line. So I think it is a very interesting process. I mean, reverse offset is good for these kind of line widths. I would imagine that the printed lines are generally very thin. So let's say from 20 to maybe 1000 nanometers, the printed resolutions could be about 0.5 or a little less to a few micrometers. And the printing speeds could be would be, well, less than 50 millimeters per second or so, just to give you some parameters about the capabilities of this process generally so. R2R Reverse Offset Printing? Here's another, I think, interesting technology. This one is, again, by a Japanese company. Unfortunately, the source is again falling behind my picture. So this is by Asahi Kasei in Japan. So you can see they're printing very fine lines. And I didn't have a video here, but these are continuous lines with very well defined edges and just 300 micrometers wide. One of the innovations here is that they have these roller molds, which they call a seamless roller mold, and it is patterned not using just laser, but with electron beam lithography. And you can see the kind of the features they can define on this roller mold, around one micrometer wide and five micrometer pitches. And this is a very, very smooth, smooth surface. And here you can see a couple of examples of actual kind of roller roller molds. This is, I think, 250 millimeters in width and about a hundred millimetres in diameter. So what is the actual printing process here? Undisclosed. But my guess is that this is also a form of reverse offset printing process. So the previous example that I showed you was the relief plate was flat. In this case, the relief plate is actually a roll, so it's a fully roll to roll process. And here you can see an application in this demonstrator. They are printing aligned with a three micrometers. So not at the leading edge of the of the capability, but it is a transparent kind of an antenna application for transparent RF ID for for putting it on products without without taking up real estate. So the RFID would be there without occupying any real estate on the packaging. R2R Nanoimprinting So I guess we are now almost approaching the end. There are only two slides left, I believe. So. I just wanted to say that there is a whole array of technologies which are hybrid and roll to roll, and they go to very, very, very fine lines. So this example is by Panasonic. Panasonic is not the only company developing this technology and is in fact, not the first. But I think it is kind of a state of the art. From what I can gather, because the way the process works is that you have a substrate, you coat it with a resin, and then you roll to roll emboss a pattern into the resin. Actually, they do it on both sides, so it's a double sided embossing process. Then they simply fill in the grooves with silver nanoparticles. So here you can see they can achieve a two micrometer line with with a good aspect ratio. And very, very good sort of sheet resistance of two ohms per square. What is really interesting about this process, I think, is that the conductive line ends up being embedded into the substrate. And what that means is that to increase the conductivity of the line, you don't actually have to print a thicker and therefore a wider line. So this is a classical example, but you could just make the grooves a little deeper. R2R Photolithography And I want to say just a few words about the competition, which is photolithography. And here's an example of a roll to roll photolithography. This is developed, I believe, by Dai Nippon Printing. The target market is transparent displays, and you can see the kind of the line with that they've achieved. So the first generation of their products had four micrometers line with the second had two micrometers, and now they've announced on kind of smaller sizes, one micrometer line width. So here's an example and I think they can do this to serve the market of sub 40 inch displays. Just, just gives you some information about the state of the art using alternative techs. So with that, we come to the end of the end of the presentation. Again, thank you for your attention.
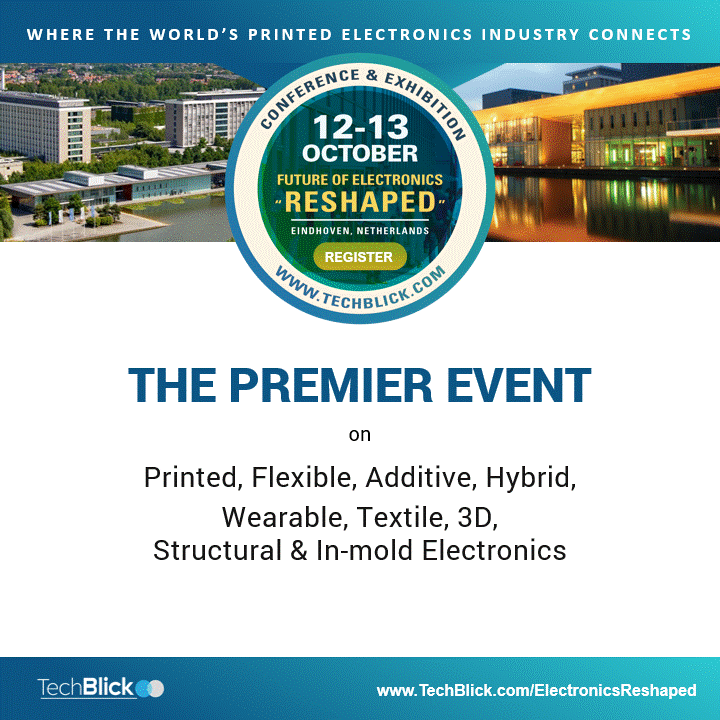
Comments