The amount of electronics will increase and the use of raw materials in the sector is expected to double by 2050. The amount of electronic waste has also almost doubled over the past 16 years, and only 20% of this waste is collected efficiently. The EU, therefore, calls for more sustainable solutions from the electronics industry. VTT is developing them by combining printed electronics, bio-based materials, and eco-design thinking.
The environmental load of the electronics industry can be significantly reduced by moving from traditional manufacturing processes to printed electronics and from fossil-based materials to bio-based materials. By using printing processes, up to 90% of fossil materials can be replaced in some applications. At the same time, energy consumption may decrease to one-fifth compared to traditional processes. Ecodesign, on the other hand, promotes the efficient use, recycling, and recovery of valuable materials.
VTT has versatile expertise in all these areas and can provide extensive knowledge in both electronics manufacturing and new environmentally friendly materials. In the ECOtronics project funded by Business Finland, this expertise has been combined to assess the environmental load of electronics and develop sustainable solutions, and determine their feasibility.
“The environmental impact of electronics is caused by, among other things, the used raw materials and manufacturing processes and the use, recycling, and post-treatment of products. The environmental load must be examined on a case-by-case basis throughout the life cycle of the product so that the right route to reduce it may be found,” says Liisa Hakola, the leader of the ECOtronics project at VTT.
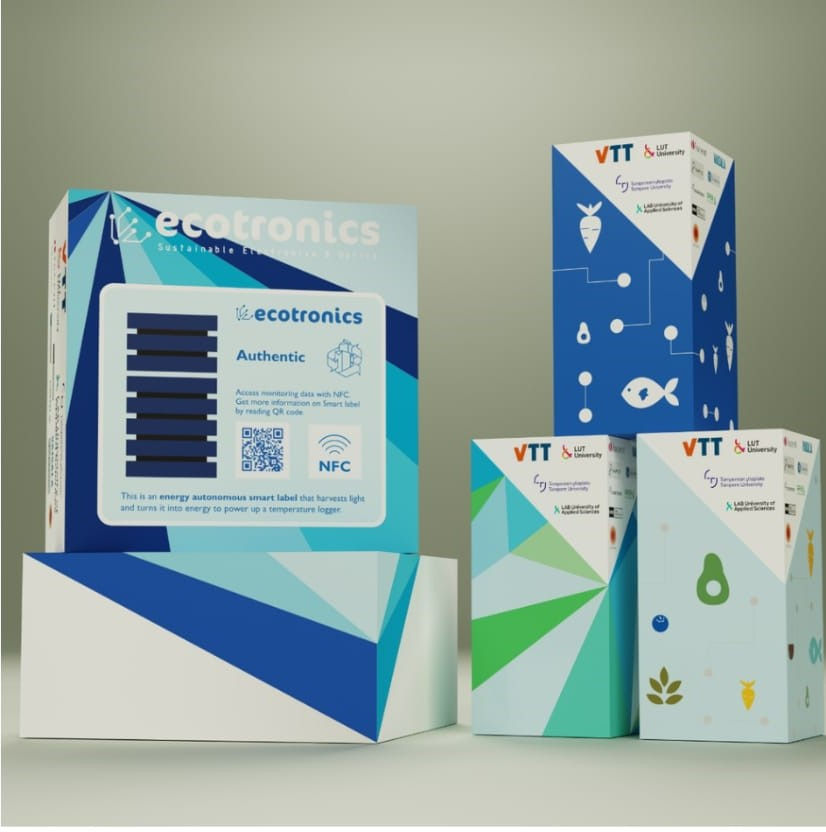
Solutions tested in demo cases
VTT and the university partners have tested the feasibility of new sustainable solutions through demo cases. The subject of one demo was a smart label printed on bio-based plastic, which is powered by a supercapacitor rechargeable with solar panels, even indoors. The label can be added as a part of the product packaging and can be used to monitor, for example, the transport conditions of food and medicines or other heat-sensitive products. The solution is also suitable for monitoring different spaces and, among other things, for monitoring moisture, pressure or damage sustained by-products. Another demo case concerned a biodegradable antenna connected to a circuit board, which is suitable in, for example, wireless transfer of measurement data.

One of the advantages of bio-based materials is that their properties can be modified in many ways. This enables completely new applications. “For example, a smart label is light, thin, and flexible. It is suitable for, among other things, wearable electronics for which traditional heavy, thick and rigid circuit boards are not suitable. We will continue to explore these opportunities,” says Maria Smolander, Research Team Leader at VTT.
Sustainable electronics for business needs
VTT helps companies in the electronics industry find new solutions for sustainable electronics. Eight companies interested in sustainable electronics participated in the ECOtronics project. For example, the package industry operator Iscent received help in material selection and testing, and the health technology developer GE Healthcare in ecodesign and environmental impact assessment. “We wanted to explore and test new bio-based materials, and we found new alternatives, one of which was perfectly suited to our customer. This helped us to sign a significant contract,” says Raimo Korhonen, Partner and Project Manager, Iscent Oy
GE Healthcare wanted to investigate the environmental impact of its new pulse oximeter, which is a cordless device placed on a patient's anfinger.
“We compared the environmental load of our product concept with the alternatives available on the market and examined possible benefits and problem areas in terms of environmental impact. The significance of the environmental load was also assessed by comparing it with examples from everyday life, such as one liter of milk. In this comparison, the product concept's performance was excellent,” says Juha Virtanen, Hardware Project Leader, GE Healthcare.
More information:
Comments