
Darin Heisterkamp, Head of Sales
SAFI-Tech, Inc.
Introduction
Soldering technology is thousands of years old, but is still an essential component in electronics assembly, without which none of our advanced electronic devices would function. Though the soldering process has seen some refinement in modern times, it is still accomplished by heating the soldering metal alloy to its molten state and applying the metal hot at contact points to create a conductive solder joint. For today’s most popular tin-silver-copper (SAC305) soldering metal alloy, that processing temperature is in the range of 240 °C to 260 °C, and therein lies a huge problem.
Design engineers developing the next generations of electronic products are being driven by consumer demand for new solutions that don’t conform to existing formats, are much smaller, and are more feature rich. Meeting this demand requires new materials that are thinner, lighter weight, and flexible, and designs that are more densely packed with increased miniaturization and integration. Unfortunately, such new products are completely incompatible with high-temperature soldering, but they still need the benefits of full metal conductive solder joints to function.
New Supercooled Soldering™ Technology
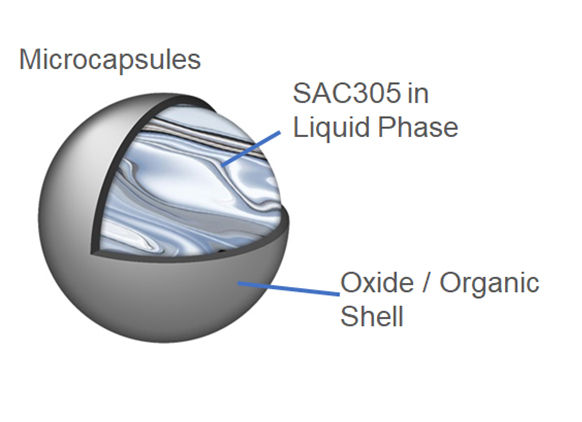
Figure1: Supercooled liquid metal microcapsule.
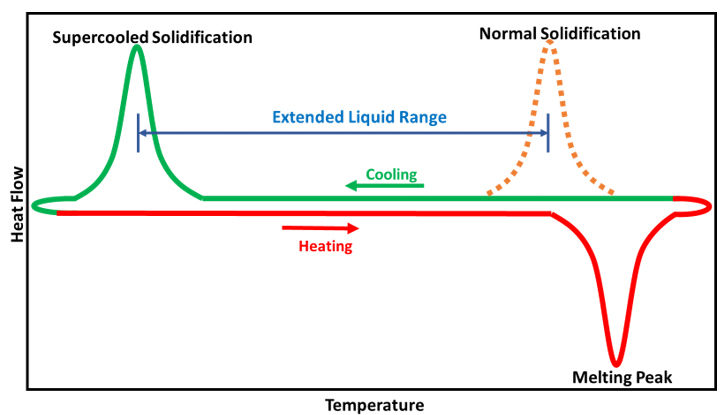
Figure2: Calorimetry graph showing supercooled liquid range.
SAFI-Tech has developed a new Supercooled Soldering™ technology using SAC305 that can solve this problem. Supercooling is a phenomenon that all materials experience at the phase transition from liquid to solid. SAFI-Tech’s micro-encapsulation process creates a new form factor that stabilizes the supercooled liquid phase of SAC305 inside a nanofilm shell, and extends the utility of this liquid phase to temperatures well below the alloy’s normal solidification point (see Figure 1). Now, SAC305 can be applied throughout this extended liquid range to form full metal conductive solder joints at temperatures best suited to each product design (see Figure 2).
This novel solder interconnect technology avoids thermal damage to components and materials, as well as mitigates quality issues caused by coefficient of thermal expansion mismatch. SAFI-Tech supercooled liquid metal microcapsules appear as a fine powder, which can be incorporated into a typical solder paste formulation. Since the metal core inside the microcapsules is a liquid, it can flow out, wet, coalesce, and solidify to form a solder joint after action is taken on the shell. Similar to existing solder pastes, that action can be imparted by solder fluxes which dissolve the shell and release the liquid metal at a target temperature to bond opposing contact points (see Figure 3).
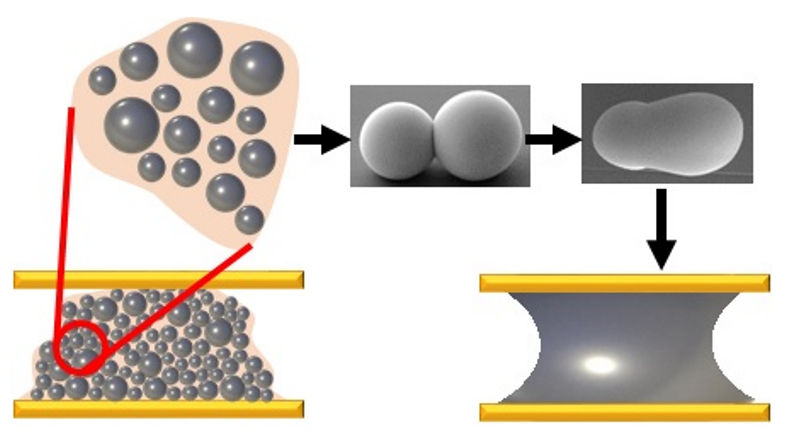
Figure 3: Solder flux dissolves microcapsule shell to form solder joint.
Product Demonstration
SAFI-Tech demonstrates this supercooled soldering technology using SAC305 by attaching a BGA integrated circuit package to a printed circuit board at low temperatures. As BGA package dimensions increase with greater integration, integrated circuit components become more susceptible to thermally-induced dynamic warpage caused by the high temperature soldering process, which leads to attachment defects. For this demonstration, SAFI-Tech developed a prototype paste formulation and a flux with an activation temperature at 180 °C, over 60 °C below normal SAC305 reflow temperatures. This is also the same range where low temperature soldering with BiSn alloys occurs. The demonstration was set up as follows:
Test Board
- FR4 PCB
- ImmAg Surface Finish
- Electrical Testing Contacts
Print Conditions
- Steel Stencil with Steel Squeegee
- 480 µm diameter aperture
- 4 mil thickness
Figures 4 and 5 show the print properties of the paste and the stenciled paste in the BGA grid pattern on the circuit board.

Figure 4: Rheometry of prototype supercooled solder paste.
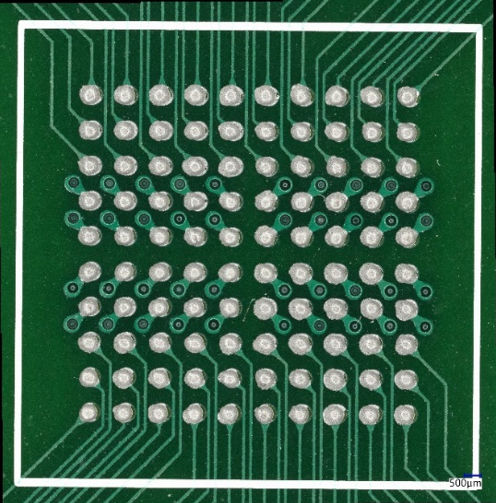
Figure 5: Paste printed in BGA grid pattern
Cross-sectional imagery of the BGA component after supercooled soldering shows good joint formation between the BGA SAC305 solder ball and SAFI-Tech’s supercooled SAC305 solder (see Figure 6). The BGA board assembly was sent to STI Electronics for preliminary analysis, where all BGA joints remained conductive with no failures after 1000 cycles of thermal shock (-40 °C to 110 °C).

Figure 6: BGA with SAC305 ball attached to FR4 board soldered at 180 °C using SAFI-Tech supercooled SAC305 solder paste (Normal SAC305 reflow at 240 to 260 °C).
Particularly interesting is the clear presence of the desirable Cu6Sn5 intermetallic compound (IMC) layer formed with SAC305 at this temperature (see Figure 7). Intermetallic compounds play an important role in the mechanical strength and reliability of the solder joint. Generally, an IMC layer less than 4 µm is preferred, and the supercooled soldering IMC layer was measured at 2.5 µm (see Figure 8). This is very similar to a typical IMC layer formed with SAC305 at conventional peak reflow temperatures.

Figure 7: Cross-section of SAFI-Tech supercooled SAC305 solder joint interface showing intermetallic compound (IMC) layer.
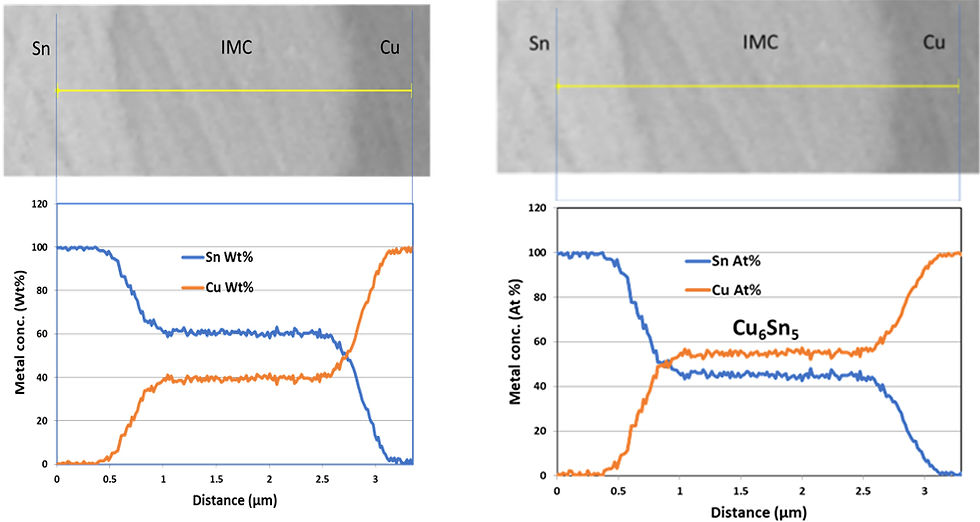
Figure 8: EDS line mapping of 2.5 µm intermetallic compound (IMC) layer.
Further Development
SAFI-Tech continues its development work on supercooled SAC305, with an objective to achieve a supercooled liquid state for this alloy close to 0 °C (see Figure 9). In addition, SAFI-Tech’s patented and patent-pending micro-encapsulation technology is alloy agnostic. Further developments could also include other alloys important to industry that become even more advantageous if applied using supercooled soldering technology.
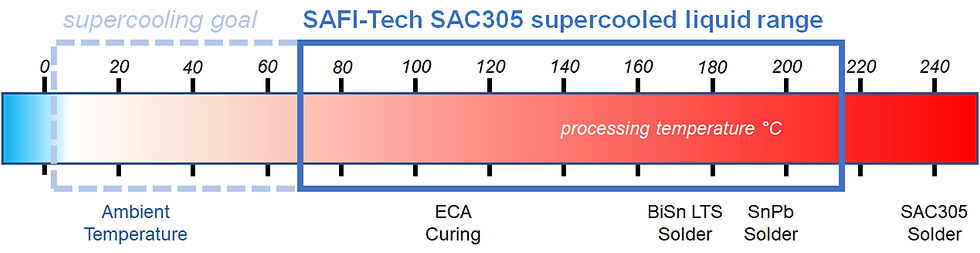
Figure 9: SAFI-Tech development of supercooled SAC305 microcapsules.
About SAFI-Tech
SAFI-Tech, Inc. was founded in 2016 by Prof. Martin Thuo and Dr. Ian Tevis, co-inventors of the platform supercooled micro-encapsulation technology. SAFI-Tech brings a new full-metal no-heat paradigm to conductive interconnect and metallization technologies for the next evolution in electronics. “SAFI” means clean or pure, and guides the company in its efforts to bring new technologies to market that have a positive economic and societal impact.
(This material is based upon work supported by the U.S. Department of Energy, Office of Science SBIR program under Award Number DE-SC0020704.)

Comments