Repairing Open Defects in Semiconductors: A Key to Sustainable Manufacturing
- khashayar Ghaffarzadeh
- 4 days ago
- 4 min read
The Evolution of the Semiconductor Industry and Its Path to Sustainability
Author: Elisa DUQUET, Hummink, elisa.duquet@hummink.com
The semiconductor industry is one of the most complex, dynamic, and technologically advanced sectors in the world. It plays an essential role in shaping modern life, serving as the foundation for everything from smartphones and MRI machines to kitchen appliances and space shuttles. In today’s digital world, nearly every device we rely on is powered by semiconductor chips.
The demand for semiconductor chips has reached unprecedented levels. According to the Semiconductor Industry Association (SIA), the industry shipped a record of 1.15 trillion semiconductor units last year, this figure means that every person on earth could receive over 150 chips annually. In addition, the SIA announced that the global semiconductor sales hit $627.6 billion in 2024, an increase of 19.1% compared to 2023. The semiconductor industry is projected to reach over $726.73 billion by 2027.

As production scales up to meet increasing demand, so does the need for sustainable solutions to manage waste and defective components. Indeed, the twelve largest semiconductor manufacturers together generate about 2.7 million tons of waste annually - about as much as 5 million EU citizens. Nearly 50 percent of the waste generated by the semiconductor industry is classified as hazardous (V.A. Heinrich & D. Hübner). This waste includes defective or obsolete chips discarded during manufacturing. In the worst scenario and without further proactive measures, the amount of waste could almost double by 2030, due to expected production growth.

Historically, the semiconductor industry has focused on relentless innovation and mass production, often leading to significant electronic waste and the rapid obsolescence of components. However, a transformative shift is occurring - one that prioritizes repair and sustainability.
In the semiconductor industry, several printing methods can be used to correct production defects and reintegrate components into production lines. These techniques primarily aim to restore defective interconnections and repair open defects at the RDL or bump level. Inkjet printing enables material deposition using an inkjet process without having contact with the substrate. This method minimizes the risk of substrate damage, but it offers limited precision (>10 µm in line width).
EHD (Electrohydrodynamic) printing, on the other hand, uses electric fields to generate droplets and deposit conductive inks. However, this technology is complex to implement, as reproducibility becomes challenging at high resolution and requires precise control of electrical parameters. Finally, UPD (Ultra-Precise Deposition), which applies pressure, is also limited in terms of resolution. Indeed, the pressure applied tends to expand the deposits.
To overcome the challenges of existing techniques, HPCaP technology introduces a breakthrough approach, enabling ultra-precise, high-resolution repairs that ensure superior electrical performance and seamless reintegration of semiconductor components into production lines.

HPCaP technology: Correcting Production Defects for Semiconductor
The HPCaP (High Precision Capillary Printing) technology, developed by Hummink, offers an innovative alternative to traditional additive manufacturing methods. Based exclusively on capillary forces and resonance, HPCaP technology allows for a remarkable level of precision in depositing various materials.
HPCaP technology offers effective repair of production defects at the level of RDLs, flip chip bumps, and interconnections in order to improve the yield and put the chips back into production lines.
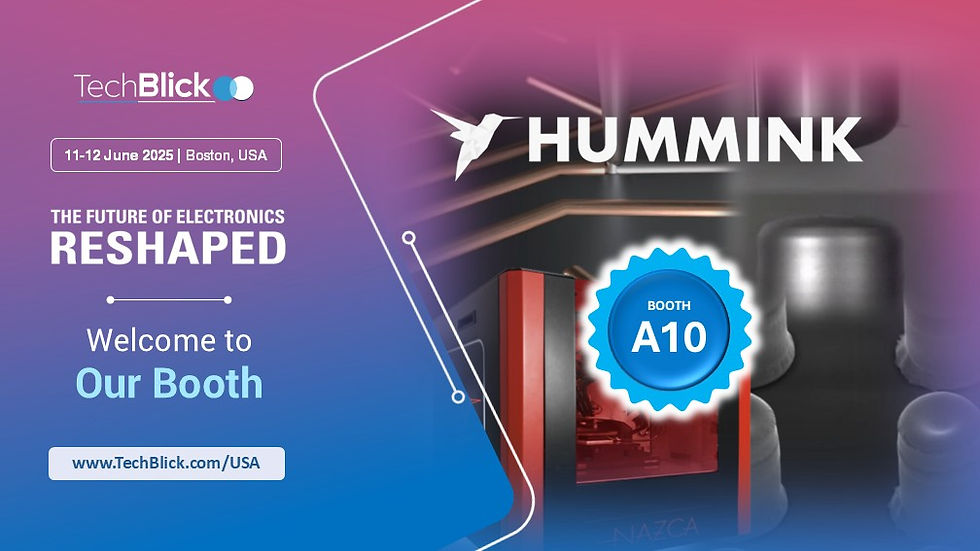
Unlike other conventional repair methods, such as inkjet printing or chemical vapor deposition (CVD), HPCaP achieves an exceptionally low resistivity of less than 10 µΩ·cm, ensuring optimal electrical performance. Additionally, with HPCaP a resolution of less than 2 µm (L/S) is feasible, providing the means to correct RDLs at the needed submicron scales with high precision and reliability, overcoming a key challenge in semiconductor repair. Beyond RDL repairs, HPCaP technology is also effective in addressing missing bumps - a common production defect in advanced packaging. HPCaP provides a solution that meets the new industry specifications by creating high aspect ratio bumps (up to 20:1) and microbumps of diameters less than 5 µm; all while maintaining excellent resistivity and ensuring both high reliability and reproducibility.
Furthermore, HPCaP technology allows for the repair of missing interconnections and damaged pads, restoring semiconductor functionality without requiring costly replacements. By enabling precise, high-performance production repairs, this technology allows semiconductors to be put back into production lines and improve their yield, supporting a more sustainable approach to microelectronics manufacturing.

Conclusion
Innovation and sustainability must be combined as the semiconductor industry is at a pivotal crossroads. As demand for semiconductor chips continues to grow, so does the urgency to adopt environmentally responsible practices that mitigate waste and extend the lifespan of electronic components. Repairing, rather than replacing, defective semiconductors is a crucial step toward achieving this goal.
HPCaP technology offers an efficient and high-performance alternative to traditional methods in terms of precision semiconductor repair. By enabling the restoration of open defects, missing bumps, and damaged interconnections with unparalleled accuracy, HPCaP not only enhances yield and efficiency but also significantly reduces electronic waste through the production line.
Companies that invest in cutting-edge repair technologies like HPCaP will not only gain a competitive advantage but also contribute to a greener, more responsible future for microelectronics manufacturing. The shift toward sustainability is no longer optional - it is the key to long-term resilience and progress in the semiconductor industry.
We are Exhibiting in Boston and Berlin.
Visit our booth at the TechBlick event on
Contact us for your special discount coupon to attend (elisa.duquet@hummink.com)
Commentaires