Coherent | Real world data on LIFT transfer in MicroLED production
- khashayar Ghaffarzadeh
- Sep 30, 2024
- 5 min read
Updated: Jan 3
Author: Dr. Oliver Haupt, Director Strategic Marketing, Coherent, oliver.haupt@coherent.com
Excimer-based laser-induced forward transfer (LIFT) is a practical mass transfer process for today and tomorrow.
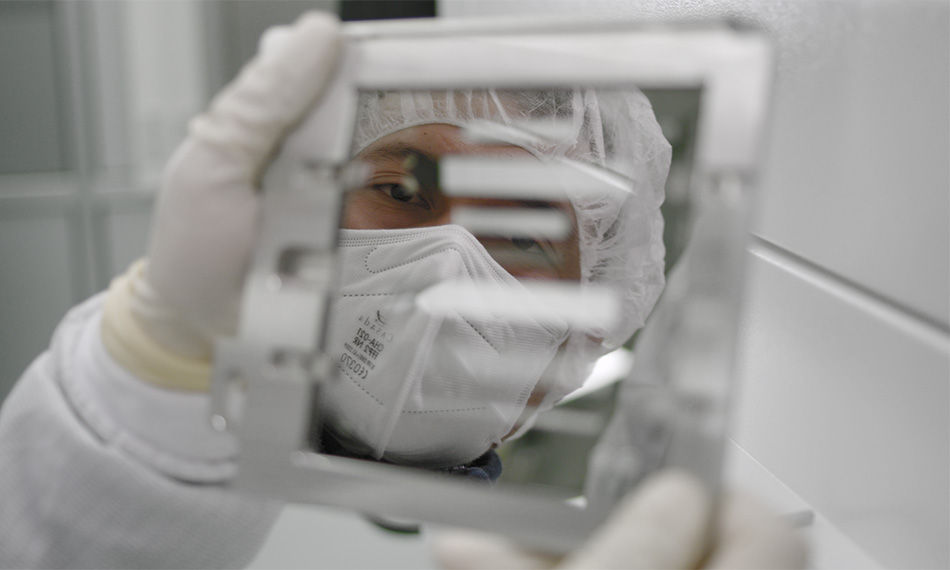
MicroLEDs stand at the forefront of next generation display technologies because they offer superior brightness, efficiency, and longevity over other panel types. In fact, the advantages of microLEDs are so significant that they promise transformative applications ranging from advanced smartwatches to expansive AR/VR experiences.
However, the display industry faced a significant setback when tech giant Apple abandoned its ambitious microLED project after years of heavy investment (estimated at over US$3 billion since 2014). Apple hasn’t publicly announced their reasoning for this move.
Those in the display industry who are not Apple suspect that they have not been able to develop a cost-competitive microLED display compared to existing OLED displays. They may not have utilized the latest advances in production technology to improve yield and throughput. A key to this could be the "mass transfer" process approach - a critical step in large-scale production.
Here we’ll learn about the pivotal role of advanced mass transfer technologies and see how Excimer laser-based methods can overcome the production hurdles that might have stymied Apple. We’ll see how these offer a cost-effective and future-proof solution for microLED production.
What Exactly Is “Mass Transfer?”
We’ve described the process of mass transfer in some detail in past posts. Briefly, microLED production starts with the fabrication of red, green, and blue LEDs on separate substrates. These must ultimately be transferred to the final display circuit board. There they are arranged in groups of three (one red, one green, and one blue) to form each pixel of the display.
In some cases, the LEDs are first moved from their original substrates to a “temporary carrier” where they are held on by adhesive. Then, they are transferred to the display panel. Other manufacturers move the LEDs directly from their original substrate to the display panel without an intermediate step.
Either way, there are a couple of things that make mass transfer challenging. First, the LEDs must be placed with micron-level positional accuracy. Second, a very large number of LEDs must be transferred, so the process must be fast. For example, even just a 500x500 pixel display requires transferring 750,000 individual LEDs (500x500x3). Third, the process must be reliable to achieve the highest yield and avoid extensive repair.
Plus, keep in mind, as microLED technology develops, the LEDs themselves will get smaller. Currently they’re about 50 x 50 µm, and they’re expected to eventually reach 10 x 10 µm or even beyond. The smaller the LEDs become, the more challenging it becomes to move them without damaging them, and to place them with the required accuracy.
Lasers Lift Microleds To The Next Level
Laser Induced Forward Transfer (LIFT) offers a practical, cost-effective means for mass transfer – both for current LED die sizes (about 20 µm x 20 µm) and moving forward towards smaller (10 µm x 10 µm) dies. In LIFT, pulses from an Excimer laser enter through the backside of the transparent temporary carrier. The light is absorbed in the buffer GaN layer and vaporizes it. This pushes the LED dies away and onto the display panel substrate, which is placed in close proximity. A final bonding step connects the LEDs to the panel substrate both mechanically and electrically.
Excimer LIFT offers significant advantages over other mass transfer methods in the fabrication of microLED displays. One of the primary benefits is its high placement accuracy. LIFT can achieve placement precision below 1 µm, which is essential for the production of small, high-resolution displays. This level of accuracy ensures that each microLED is perfectly aligned, reducing the risk of defective pixels, which can compromise display quality.
Moreover, the efficiency and speed of LIFT are unmatched. It allows for the transfer of millions of microLEDs rapidly and reliably, significantly reducing manufacturing time and thus, cost. This is particularly advantageous as display manufacturers aim to scale up production without sacrificing quality.
Furthermore, the adaptability of laser-based mass transfer to different substrates and microLED sizes offers flexibility. This versatility is crucial as the demand for diverse types of microLED applications grows, ranging from tiny wearable devices to large-scale ultra-high-definition televisions.
Additionally, our LIFT solution is designed to be future-proof. As the microLED market evolves to utilize even smaller LEDs with tighter pixel pitches, excimer LIFT systems can quickly adapt. This can be accomplished without extensive retooling or downtime, ensuring that manufacturers can stay ahead in a competitive market. This adaptability, combined with the Coherent commitment to ongoing research and development, positions our solution as a pivotal technology for the future of displays.
Real-World Results
Coherent applications engineers recently performed testing to quantify some of the parameters for implementing LIFT with microLED dies substantially smaller and thinner than any devices currently in production. Specifically, we tested the placement accuracy of LIFT with 5 µm x 5 µm x 3 µm (thickness) microLEDs as a function of gap distance (distance from the temporary carrier holding the microLEDs to the target substrate). This data is useful because very small gap distances (below 50 µm) are hard to reliably maintain in a volume production environment. So, LIFT must be capable of working quickly, reliably, and at scale over larger gaps than this, even with small LED dies.
The experimental setup used a Coherent UVtransfer to move microLEDs from a 4-inch GaN donor wafer to a 100 mm diameter quartz recipient wafer. Placement accuracy (in x and y) was measured with a microscope and machine vision system that could automatically identify the dies and determine the center position of each. For each gap distance, 979 microLEDs were moved.
The graphs show placement accuracy (offset from the ideal position) for all 979 of the microLEDs, with a 50 µm gap and die-to-die pitch of 90 µm. To summarize this data, 99.7% (3σ) of the microLEDs were placed within 0.66 µm (x) and 0.56 µm of their of their target location.


Position offsets for LIFT of 979 microLEDs measuring 5x5x3 μm³ each, transferred over a 50 µm gap and with a die-to-die pitch of 90 µm.
The next graph shows how placement accuracy varied with gap distance. Submicron placement accuracy was maintained at gap distances of up to 80 µm. These numbers show that LIFT is entirely practical with these small microLEDs.

Mean 3σ position offset deviation (average of X and Y 3σ values) as a function of transfer gap distance for LIFT of 979 microLEDs with dimensions of 5x5x3 μm³.
MicroLED displays offer a revolutionary viewing experience, but mass production hurdles have held back their deployment and discouraged even some of the most technically savvy manufacturers. Excimer laser-based LIFT overcomes one major production hurdle and succeeds where other mass transfer technologies have failed. It enables precise, high-speed transfer of even the smallest LEDs, and is based on lasers that have demonstrated 24/7 operational reliability in other demanding display fabrication processes. Plus, the adaptability of LIFT ensures compatibility with ongoing microLED advancements, making it a future-proof solution for display manufacturers and paving the way for commercialization of this technology.
Learn more about LIFT.
Comments