Optimizing Embroidered Conductive Traces for E-Textiles
- ITORO PETER
- Sep 18, 2023
- 6 min read
Updated: Sep 19, 2023
Authors: Steliyan Vasilev1, Melanie Hoerr1, Michaela Kasdorf1, Sven Boehmer2
13E Smart Solutions, Krefeld, Germany
2ZSK Stickmaschinen GmbH, Krefeld, Germany
steliyan@3esmartsolutions.de
1. Introduction
Embroidery was historically a means of adorning fabrics with intricate patterns, a testament to human skill. However, in the modern era, this ancient art form has significantly evolved. In recent years, embroidery has undergone a profound transformation, emerging as a pioneering technology at the intersection of artistry and functionality. This article delves into the possibilities which embroidery offers for the production of Smart and E-Textiles, exploring technical intricacies, advantages, and challenges related to embroidered conductive traces.

Join us at TechBlick's Future of Electroncis RESHAPED conference & tradeshow in Berlin on 17-18 OCT 2023 - www.techblick.com/electronicsreshaped. Contact us [steliyan@3esmartsolutions.de ] for a special attendee discount
2. Solutions for the E-Textiles Production Made Possible by Embroidery
E-Textiles represent a fascinating synergy between traditional textiles and modern technology, serving diverse sectors like automotive, aerospace, sports and fitness, medical, home textiles, and wearable technology. Thanks to the exceptional precision and high degree of automation of embroidery technology, it is ideal for integrating functional elements into textiles, such as sensors, actuators, antennas, or electrodes. By use of conductive threads and specialized attachments for automated integration of electronic components, embroidery techniques, originally developed for aesthetic purposes, now enable reliable and scalable E-Textiles production. Embroidery makes possible the following innovative solutions, among all:
Integrating and Interfacing Electrical Components and PCBs
Semi-Automated Integration
In decorative embroidery, the Appliqué technique is utilized to attach pre-made textile patches to the carrier fabric. This same method can be used for semi-automatic placement of printed circuit boards (PCBs). After the manual placement and adjustment of the PCB, the embroidery machine takes over, automatically fixing it to the fabric and establishing the electrical connections at the interface pads.
Automated Integration
Embroidery machines equipped with automated Sequin Placement Devices can be configured to incorporate functional sequins into textiles (Fig. 1a). Functional sequins can be equipped with SMD soldered components, such as LEDs or RFID chips. For larger circuit boards, whether rigid or flexible, embroidery machines fitted with automated PCB Placement Devices can precisely position and secure the PCBs to the textile (Fig. 1b), followed by embroidery of the electrical connections. Automated integration is especially valuable for achieving reliability and reproducibility in the production of E-Textiles on a large scale.

Figure 1 Automated integration of functional LED sequins (a) and PCBs (b) by using automated Sequin Placement Device and PCB Placement Device from ZSK Stickmaschinen GmbH
Embroidery of Complete Electrical Circuits
By embroidering conductive traces onto fabric, placed PCBs and peripheral components can be electrically connected to each other, as well as to power sources or external circuitry. This approach allows for the automated integration of complete electrical circuits into textiles during a single production step.
Integration of Conductive Fibers and Wires
Tailored Wire Placement (TWP) and Tailored Fiber Placement (TFP) techniques allow precise conductor placement for applications such as illumination, textile-based heating, RFID antennas, and more.
Embroidery of Conductive Areas
With conductive threads, conductive areas in various shapes and sizes can be embroidered. These areas can serve a multitude of functions, including wide conductive traces, sensors, electrodes, and antennas, expanding applications from automotive control elements to advanced medical devices.
3. Advantages of Embroidered Conductive Traces
Embroidery of conductive traces has opened up new horizons for Smart and E-Textiles, driven by several distinct advantages:
Versatility in Design and High Precision
Embroidery offers unparalleled versatility in design. Complex patterns and intricate geometries become feasible, catering to diverse application needs. The precision achieved in embroidery ensures that these designs are replicated accurately and consistently.
Flexibility and Breathability
One of the standout features of embroidered conductive traces is their inherent flexibility. They easily integrate with the carrier fabric, preserving its natural drape. Unlike printed circuits, embroidered traces allow textiles to breathe, enhancing wearability in clothing and comfort in various applications.
Durability and Washability
Embroidered conductive traces exhibit impressive durability. They withstand the rigors of daily use and multiple washing cycles, remaining fully functional over extended periods. This longevity contributes to the reliability and sustainability of embroidered E-Textiles products.
Enabling Direct Connection to Electrical Components and PCBs
Embroidery facilitates the direct integration of conductive traces with electrical components and printed circuit boards (PCBs). This approach eliminates the need for additional connectors or complex wiring, enhancing the product’s reliability and comfort and reducing production costs.
4. Challenges and State-of-the-Art Solutions for Embroidered Conductive Traces
While there are clear advantages to using embroidered conductive traces, there are also associated challenges. In the following sections, we will outline the primary challenges and present state-of-the-art solutions to address them.
a) Compensation for High Yarn Resistivity
One of the main challenges in utilizing conductive embroidery threads is their intrinsic high resistivity of up to a few hundred Ohms per meter. To address this challenge, several state-of-the-art solutions have emerged:
Multiple Passes and Use of Conductive Bobbin Thread
A method to compensate for the high resistivity of the conductive thread is to embroider multiple passes using the so-called running stitch. Each pass adds to the overall conductivity, effectively acting like parallel resistors (Fig. 2a). Additionally, incorporating a conductive bobbin thread enhances conductivity by further reinforcing the electrical path (Fig. 2b). As an additional benefit, multiple embroidered passes compensate for the inhomogeneity in resistance throughout yarn length due to local damages in a single yarn pass during use, increasing the reliability of the E-Textiles product.
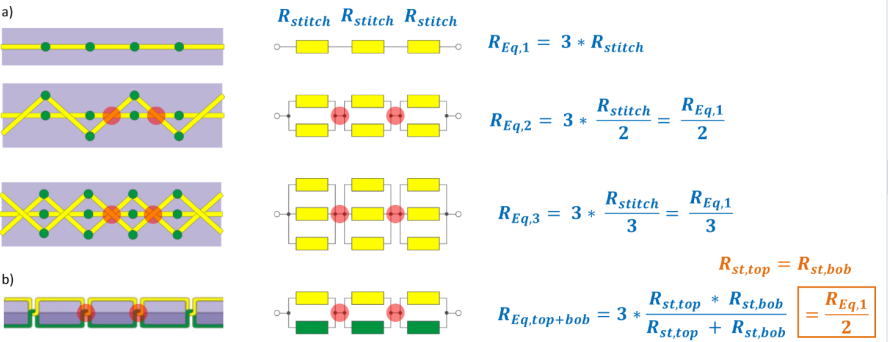
Figure 2 Equivalent circuit of embroidered conductive trace with one, two, and three passes (a), and conductive embroidery (yellow) and bobbin (green) thread (b)
Conductive Traces Embroidered as Filled Areas
An alternative approach for reducing resistivity is to embroider conductive traces as filled areas, using the fill stitch rather than the running stitch. The high density of stitches in the filled areas enhances the overall trace conductivity. To ensure sufficient electrical contact between the stitches along the stitch direction, an underlayer must be added beneath the fill stitch, angled to the primary stitch direction (Fig. 3) [1].
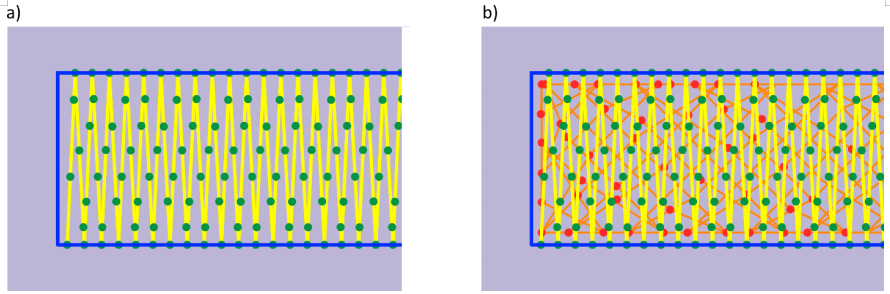
Figure 3 Embroidered area with fill stitch without (a) and with a grid underlayer (b)
b) Avoiding Conductive Thread Damage during Embroidery
During embroidery, stitching directly into the conductive yarn can damage it, compromising electrical properties. Therefore, special attention must be given to the digitizing of the embroidery design to avoid placing stitches over previously embroidered threads as well as repetitive stitching in the same spot.
To mitigate this while embroidering multiple running stitch passes, a swing factor can be introduced in the digitizing program, altering the stitching path slightly with each pass. This minimizes localized stress on the yarn, preserving its integrity and conductivity. Fig. 4 illustrates a conductive trace with four passes and an added swing factor, shown as a visualization in the embroidery machine’s programming software (a) along with a photograph of the embroidered trace (b).

Figure 4 Conductive trace with four passes for increased conductivity and added swing factor, shown in the digitizing software (a) and after embroidery (b).
When adding a swing factor, corners pose a specific challenge, leading to repeated puncturing at the same location (Fig. 5a). Rounding corners in the embroidery design is essential, as it significantly reduces the risk of stitching into the yarn, maintaining its electrical properties (Fig. 5b) [1].

Figure 5 Running stitch with three passes and an added swing factor, with multiple punctures in sharp edges (a) and without multiple punctures in rounded corners (b)
c) Enabling Crossing and Insulation of Conductive Traces
Complex E-Textiles designs often require multiple closely adjacent or intersecting conductive traces. Without proper insulation, unwanted electrical connections can occur when these traces come into contact. Adding non-conductive bridges between traces prevents unintended short circuits and maintains the desired electrical paths. Insulating bridges can be created by embroidering multiple layers of satin stitch with non-conductive thread, as depicted in Fig. 6a. It is crucial to ensure that the stitch directions of the bridge layers are angled in relation to the intersecting conductive traces.
Covering conductive traces with non-conductive thread can also be used for insulation towards the surrounding environment. Fig. 6b illustrates an example of covered conductive traces connected to moss-embroidered electrodes for body signal acquisition. The covering prevents direct contact with the skin outside the electrode areas. For applications requiring waterproofing of the conductive traces, seam sealer in the form of tape or liquid, or dispensed polymer coatings can be utilized.

Figure 6 Covering conductive traces with non-conductive thread to create insulating bridges between intersecting traces (a) and as a method of insulation towards the surrounding environment (b).
5. Conclusion
The integration of conductive traces into textiles through embroidery offers a promising avenue for the development of Smart and E-Textiles. While the advantages of embroidered conductive traces make them a compelling choice for a wide range of applications, there are technical hurdles. Fortunately, various state-of-the-art solutions have been developed to address these challenges, ensuring that embroidered conductive traces can meet the demands of diverse applications.
As technology advances and the demand for Smart Textiles grows, continued research and innovation in the field of technical embroidery will be essential. With ongoing efforts to refine techniques and materials, we can expect to see even more sophisticated and reliable embroidered E-Textiles, opening up new possibilities in wearable technology, healthcare, fashion, and beyond.
References
[1] McCann, J., & Bryson, D. (2023). Smart Clothes and Wearable Technology, Second Edition. Elsevier.
Join us at TechBlick's Future of Electronics RESHAPED conference & tradeshow in Berlin on 17-18 OCT 2023 - www.techblick.com/electronicsreshaped
Contact us [steliyan@3esmartsolutions.de ] for a special attendee discount
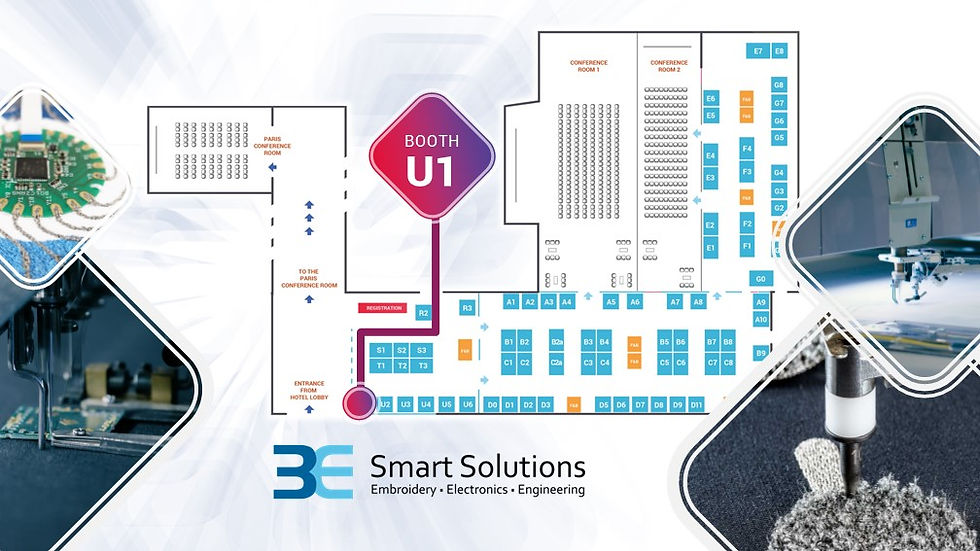
Comentarios