Molecular inks for extreme shapes | Narrowband inkjettable phosphors | R2R sheets of GaNs...
- khashayar Ghaffarzadeh
- Aug 16, 2022
- 8 min read
Molecular inks for extreme shapes | Narrowband inkjettable phosphors | R2R sheets of GaNs| Silicone-based AgCl inks| Art of screen making | EMI Sheild
House Keeping Note I: TechBlick is now putting together its agenda for its Innovation Showcase Day on 6 June 2022. Email khasha@TechBlick.com if you wish to present. In our last event we had nearly 600 live participants over a 4 hour period!
Topics: In this edition, we will cover the following technologies: Molecular inks for extreme shapes | Narrowband inkjet printable phosphor color converters | R2R large area growth of GaN microLEDs | Conformal package-level EMI shielding | Silicone-based stretchable AgCl pastes | Advances in screen printing towards <20um features
Molecular particle free inks enable extreme formability and stretchability
Molecular particle free inks can offer extreme formability and stretchability, allowing the design and production of 3D shaped and/or in-mold electronics parts with extreme curvatures and complex shapes.
Arnold Kell and Julie Ferrigno showcased some unique properties of these inks- together with unique IME possibilities- at a TechBlick conference in May 2021. Some unique feetures are:
UV sintering: you can see in the slide below how the transparent clear molecular inks can be UV sintered (x5 times faster than thermal cure). At first, the clear inks absorb very little UV light. However, as Ag particles begin to percipitate out, the absorption grows. The higher absorption in turn raise the temperature, accelerating the sintering and resulting in higher UV absorption. This process continues until the ink is fully sintered and then self stops because then the particles reflect the light back like a mirror.
Partial sintering compatible with InMold Electronics: as part of the IME process, a thermoforming step is required. In this step, the substrate temperature is raised in a controlled fashion to soften the material, allowing it to be 3D formed. In the proposed scheme, the printed molecular inks are first only partially cured by UV light. The full sintering then takes place in-situ by the elevated temperature of the 3D thermoforming process. This is an interesting approach because it enables faster curing and also allows one to sinter molecular inks on low-T substrates like PC.
Extreme formability: The 3rd slide belows shows comparision of these molecular inks with other standard inks. It shows that these inks can be stretched upto 50% with comparatively little change in resistance. This can be because these printed lines are very thin, and are thus able to follow the contours of the stretched substrate far better than a thicker particle-filled ink/paste
Unique shaped: The shapes enabled by IME are often limited by the formability of the inks. These inks can liberate the designer from such limitation, allowing the design and production of complex shapes with extreme curvatures. Here, an award-winning example is showcased by Julie, showing steep curves (see the controlled knob)
Phosphors or QDs for color conversion in LCD and microLED ? Which will win?
This is an interesting and evolving technology space to watch. James E. Murphy et al from GE Research have developed best-in class narrowband red and green phosphors, and are now evolving the technology towards microLEDs and on-chip integration.
The red KSF phosphor is an excellent narrow band color converter for wide color gamut displays. It emits 5 peaks, each of which exhibits an ultra narrow 5-nm FWHM. The main peak is centred around 631nm. It is a stable material under high light flux and high temperature conditions. Indeed, it can be on-chip integrated as a direct replacement for existing yellow phosphors. It is a major commercial success with >19 licensees and >40 BILLION (and growing) KFS-containing LEDs sold worldwide into the display industry.
As the slide below, presented at TechBlick July 2021, shows, the KFS technology is evolving. At first in 2014, the average particle size was a 25-30um. It is now down to 3-9um and evolving towards sub-micron and even nano-sized particles, enabling direct integration with microLEDs of today and tomorrow! This is an important technology trend because it brings the QD vs phosphor competition even to the microLED space (previously QDs were the only game in town due to their small size)
Furthermore, GE's KSF can now be formulated into air-stable inks based on encapsulant-free phosphors suitable for inkjet printing without nozzle clogging. It means that it can be even printed as a color converter atop microLED, in particular allowing one to use efficient blue microLEDs to create red color and/or only transfer a blue microLED color.
James E. Murphy offers also an interesting comparison of Cd-free InP QDs vs KSF for microLEDs. It argues that at very thin films (<10um), QDs are more efficient. However, as the layer is thickened, perhaps to prevent blue color leakage, self-abosrption effects can kick-in, reducing the EQE. Thus, it is argued that KSF clearly wins at >20um thickness given that it has no self absorption.
Finally, here is lack of ultra narrowband green phosphors leaving the space open to QDs. In particular, green perovskite QDs are very strong in this field. However, GE is advancing the development of its narrow-band GREEN phosphors. As shown below, these materials enable 100% DCI-P3. The performance is comparable to Beta Sialon but without cross talk with a KSF red emittesr. Furthermore, it offers 100% HTHH stability, enabling direct on-chip integration. Finally, it apepars to have QE levels approach >90%. Of course, just like KFS, it has a slow PL decay time on the order of 90-450um (QD is ns).
To learn more about QDs and microLEDs join TechBlick's event on 30NOV-1Dec: www.TechBlick.com/microLEDs
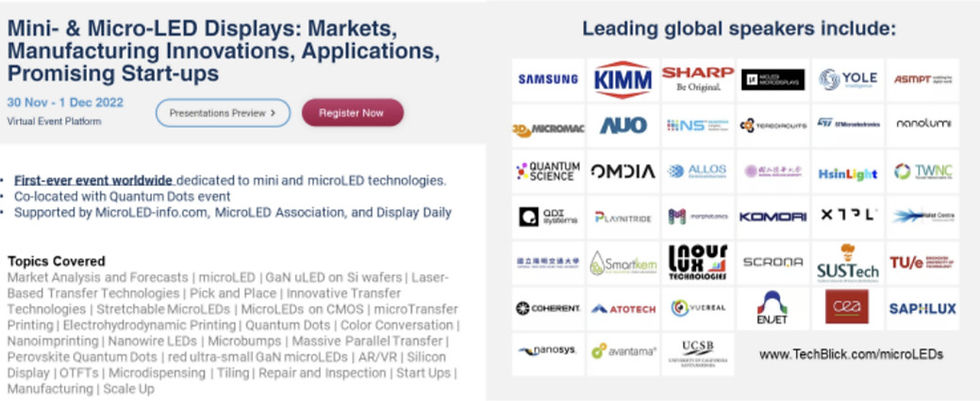
R2R grown GaN LEDs and perhaps even GaN/AlGaN HEMT transistors on metal foils instead of expensive small-area sapphire substrates?
This could be a breakthrough technology, bringing the robust and efficient inorganic LED technology to large-areas. In microLED displays, it could mean monolithic integration, leading to mobile-sized and large displays manufactured without a wafer-to-substrate transfer step.
As shown below, iBeam Materials is developing such technology. It first planarizes a rough metal foil and then uses an ion beam to form a nm-thick layer with aligned grains. This 'template' then acts as the growth substrate in lieu of, say, a sapphire wafer.
As seen below, this technology has already been used to demonstrate a functional GaN LED as well as a GaN/AlGaN HEMT. In July 2021 (when the results were presented at TechBlick) the PL was upto 70% of normal LEDs. However, a direct comparison is not yet fair as the standard approach benefits from decades and decades of accumulated know-how and production expertise.
Currently, the LEDs are still not done in a R2R fashion, although the 'template' can be R2R manufactured on 20"-wide substrate. The next step of development will involve demonstrating a R2R MOCVD GaN growth. The R2R production of the template is not the bottleneck, but the growth of a thick (5um or so) GaN LED..
Finally, Vladimir Matias argues that this technology has the potential to lower cost of production by a factor x25. A detailed cost analysis is shown below, demonstrating the technical milestones which need to be achieved to enable this cost roadmap.
To learn more about this talk and about microLED join TechBlick first-ever specialist event on microLEDs: www.TechBlick.com/microLEDs
Particle Free Inks for Conformal EMI Shielding?
Conformal EMI shielding is a megatrend on its way to become ubiquitous in electronics. The incumbent process is based on sputtering a tri-layer structure consisting of SUS (stainless steel)- Cu-SUS (total stack is 3-6um typically) on the EMC (epoxy molding compound) of the package. Hikaru Uno from Merck & Melbs LeMieux from Electroninks Incorporated show an alternative based on non-vacuum spray coating of particle-free Ag inks. In these slides, you can see performance analysis and detailed cost analysis/projections.
The incumbent (sputtering) is a well established technique with many market reference from the likes of Apple and Samsung. However, it is a vacuum process requiring substantial CapEx investments with a large production footprint. The sputtering deposition rate will also be low given the required film quality. Sputtering is poor at side wall and deep trench coverage, resulting in large thickness variations between the top and side walls.
Spraying the EMI shielding can address some issues: it is a non vacuum process with a low Capex and a high unit-per-hour (UPH) throughput and is able to offer uniform side and top wall coverage. The spraying can be used with Ag or Cu nanoparticles.
Both nanoparticle techniques though suffer from expensive materials, potential for nozzle clogging and thus production downtime, and even relatively thick required coatings.
To overcome these shortcomings, particle-free silver inks can be sprayed.
Is this technique effective? The below slides show shielding effective upto 40GHz with 1.2 and 3um coatings. This seems to meet the requirements.
Is it reliable? In the slides below you can reliability data showing no measured change in sheet resistance of the package-level coated when subjected to a prolonged duration of harsh conditions
Is it cost effective? Sputtering has a high capex cost as well as relatively high labour costs. However, spraying has higher ongoing material consumption costs.The slides below shows that spraying can be a very cost competitive approach
Already commercial? It is still in sampling. The main stumbling back is the ever underestimate power of incumbency and already sunk CapEx investments in sputtering lines
On the process, as shown below, the package is first pre-treated with plasma. The particle-free ink is then sprayed whilst the packages on the chuck are held at 160-200C. The elevated temperature results in rapid particle formation during the spray. Finally, after spraying, the inks are then cured for 20min@140-160C. There are relatively low curing temperature compared with other particle-free inks on the market.
With the first successful market reference using spraying, the market gates will open, lifting all ink-based techniques and making this a part of fast-growing electronic packaging industry
Stretchable silicone-based medical devices with AgCl fillers?
In general, silicone-basedsheets conductive pastes are rare and the versions with AgCl fillers- needed for many medical wearable applications- are even rarer! David Dewey from FUJIKURA KASEI Co Ltd unveiled this paste for the first time in June at TechBlick. The pastes can offer 1-10 E-4 ohm/sqr when cured at 150C for 30min or so on substrates such as PET or silicone sheet. These inks are compatible with other silicone-based (insulator, adhesive, etc) out of Fujikura's portfolio, enabling one to print complex multi-layer medical wearable devices on stretchable substrates like silicone!
To learn more visit www.TechBlick.com or join the industry in Eindhoven on 12-13 OCT 2022
Pushing screen printing below 20um linewidths
The progress of screen printing towards fine line printing has been incredible going from 100 µm features before 2010 to 70 µm to 2015 to 40 µm in 2018 and now pushing - in development- towards 20 µm and less. In parallel, the wet thickness of the printed line have gone down from 12um or so in 2018 to now just 4um.
In the slides below, Jeffrey Campbell from Sefar Inc. shared examples of screens for fine line printing and showcased fine (<20um) printed features. This slides were presented at TechBlick in March 2022.
Advances in all elements of screen making technology have been crucial in driving this development forward. In his presentation at TechBlick Jeff also explained the key technological steps required in enabling and sustaining this trend. These include
fine mesh: this is a must as a finer mesh enables higher openings and thinner lines even at high mesh counts. This is shown below. In this slide, you can examples of printed features using 11um stainless steel meshes from Asada Mesh. Narrowing the diameter of the mesh may sound easy, but shaving each micron meter requires three years of intense development!!
mesh calendarig: flattening of mesh with rollers improves tensile strenght of the mesh and provides dimensional stability. This enables better control and print-to-print consistency even in fine feature printing
emulsion flatting: Reduces the surface roughness of the screen’s surface and reates a more consistent corridor for the paste to travel through. Furthermore, it improves the edge definition of the final print
In the slides below you can see many examples of various screens (mesh + emulsion + additional processing like calendering) suited to fineline printing (20um or less).
Do NOT forget to secure your ticket to the most important upcoming event on Printed Electronics

תגובות