Kodak’s Copper Micro-Wires for Transparent Heater Applications
- ITORO PETER
- Oct 12, 2023
- 5 min read
Carolyn Ellinger, Chris O’Connor, Chris Liston, Emily Rej, Tom LeBlanc
Eastman Kodak Company
Kodak has a long history of manufacturing quality film products – starting with silver halide imaging films for consumers, including the iconic KODACHROME. Kodak is continuing to build on that history, manufacturing a variety of industrial film products for strategic business partners in many industries – from automotive to battery to healthcare. Built on expertise in coating, printing, and image quality, printed electronics products and contract manufacturing services offer customers modern functionality rooted in decades of manufacturing excellence.
Flexible heaters were first developed in the late 1800s, around the same time as Kodak was starting to manufacture film products While these first flexible heaters were textile based, they operate on the same resistive heating principles as today’s flexible film heaters.
Join us at TechBlick's Future of Electronics RESHAPED conference & tradeshow in Berlin on 17-18 OCT 2023 - www.techblick.com/electronicsreshaped. Contact us for your discounted passes
With new technologies come new challenges and limitations, and “hidden” heaters are being deployed to improve the functionality of a broad range of electronic systems. Temperature-limited electronic devices, such as LCDs, require heating to be able to operate in cold environments. Outdoor sensors require that ice and snow be removed from their front surface to ensure their operation. Each of these applications (many many more) require transparency and heating. However, while each application nominally requires “heat” and “transparency” – the requirements and form-factors of these transparent heaters vary across applications, and from device to device.
Kodak’s manufacturing process for fabricating highly transparent patterned heating films delivers designs optimized for individual customers, various integration paths, and a myriad of end-devices. The copper micro-wire designs are manufactured with 2-μm imaging resolution, enabling ultimate freedom in macroscale and microscale optimization. The fully additive, roll-to-roll printed electronics manufacturing process produces copper micro-wires by printing a catalytic ink in the desired pattern, and then electrolessly plating copper to the specified height allowing for independent control of transparency and sheet resistance.
As described in this white paper, Kodak works with customers to determine the optimum heater design. Figure 1a illustrates a simple approach in designing for a desired power density at a given system voltage. Figure 1b illustrates just a few of the many possible designs for uniform transparent heating.

Figure 1a. Example of heater designs for system optimization. Each heater has the same heated area, same transparency, but have been tuned to a different resistance (R) to achieve the required power density (PD) and the supply voltage of a given application.
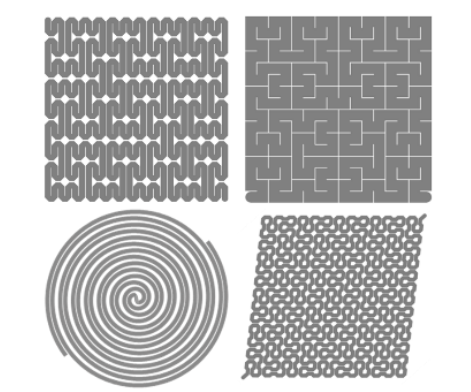
Figure 1b. Example heater patterns.
How do resistive heaters work?
Resistive heaters function by Joule heating, also known as Ohmic heating, where the flow of electric current through a conductor produces heat. All conductive materials exhibit this resistive heating phenomenon, with the heating response varying based on the specific properties of each material. Resistance is defined as the resistance to the flow of current at a given voltage bias, or R = V/I. Heater power is a function of the amount of current that is driven through an element of a given resistance: P = I2R = V2/R.
Join us at TechBlick's Future of Electronics RESHAPED conference & tradeshow in Berlin on 17-18 OCT 2023 - www.techblick.com/electronicsreshaped. Contact us for your discounted passes
Therefore, a heater with a higher resistance will require less current to generate the same power. Conversely, a conductive trace with low resistance will have lesser heating when current is applied than a higher resistance trace. In typical operation, heaters are driven by a constant voltage power supply, and a heater with a lower resistance will consume more power and heat to a higher temperature.
The resistance of any heater is a combination of the pattern of the resistive element and the electrical properties of the material used. The resistance of conductors of a given thickness can be expressed as sheet resistance (Rs) in Ohm/square, so the end-to-end (terminal) resistance of any conductive pattern is Rs*L/W where L/W is the number of squares. Consequently, at a given operating voltage, the power per unit area or power density (PD) is proportional to 1/R, and 1/Rs for square heater element as shown in Figure 2.

Figure 2. Power density of a square heater at various voltage levels as a function of sheet resistance.
What Sets the Kodak Technology Apart?
Kodak’s cleanroom manufacturing leverages Kodak’s long history of innovation in material science, image science, printing, deposition, and roll-to-roll manufacturing to produce patterned micro-wire films with the unprecedented combination of high transparency, neutral color, low reflectance, and low sheet resistance. Cleanroom manufacturing minimizes electrical yield losses and ensures that parts will be free of transparency-reducing particulate going into final integration. The fully additive, roll-to-roll process features ~2 µm imaging resolution to produce fine copper micro-wires as narrow as 5 µm in width, by first printing a patented catalytic ink and then electrolessly plating copper to the desired height. The process enables the ability to independently tune sheet resistance and transparency, the ability to manufacture films with highly conductive traces leading to more resistive heating elements, and the ability to form multiple devices or electrical elements on a single substrate in a single roll to roll manufacturing flow – on one or both sides of the substrate.
The design tools of the Kodak process enable functional heater designs without sacrificing transparency through a combination of mesh design (line dimensions, gaps, curves and angles), copper thickness, and the resistive path of the heater. Not only can the Kodak process support freeform design--only limited by imagination--other supporting elements such as traces, bond pads and even non-conductive or graphic can be additively included. Transparent mesh designs are readily obtainable with visible light transmission (VLT)>85% with Rs from 1 to 5 Ohm/square, as illustrated in Figure 3.

Figure 3. Kodak copper micro-wire mesh performance for a variety of mesh patterns represented the ratio of pitch to linewidth (LW) and copper thicknesses.
The design freedom that comes from patterning via printing enables not only the pattern selection optimized for transparency, but also optimization of the overall design of the heater for a given system. For example, if the application has a square area that requires uniform heating a possible heater design would be a single square patch of resistive heater, but in this case the power density achievable would be limited by both the sheet resistance of the heater and the operating voltage available in the system. Typically, an application will have specified power, temperature and voltage requirements and a heater must be designed to operate at those conditions. Figure 4 illustrates how heaters may be designed using the mesh designs of Figure 3, with a reference shown at 100 W/m2 and the design choices depending on the supply voltage. For example, if a 3V power supply is chosen then a three-leg heater design is preferred, but if a 12V power supply is chosen, then a 3-leg heater would not be suitable and a 7-leg heater is preferred.
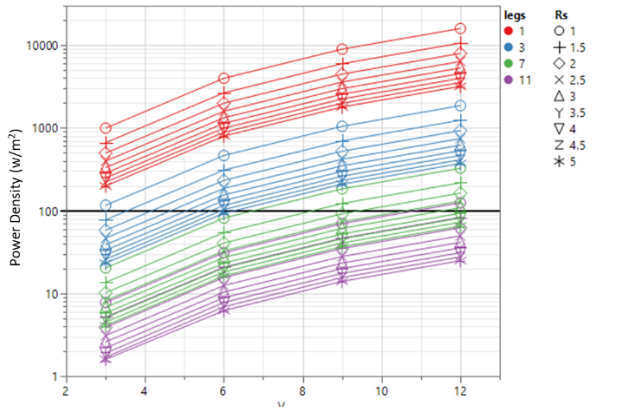
Figure 4. Illustration of heater designs to obtain a desired power density versus supply voltage.
Ready-to-Integrate Transparent Heaters
Kodak is seeking strategic integration partners for transparent conductive heaters. Products and devices from this manufacturing line include all benefits discussed above, and ready-to-integrate films can be supplied for evaluation.
Contact Information
For more information on Kodak’s micro-wire technology and enabling manufacturing process, please contact: sales.printedelectronics@kodak.com.
コメント