Eastprint | Biosensores portátiles
- khashayar Ghaffarzadeh
- Oct 9, 2022
- 3 min read

Contacto: Rick Ramos, Ingeniero de marketing y ventas internas – Eastprint Inc. Correo electrónico: rramos@eastprint.com Página web: https://www.eastprint.com/index.html
Introducción:
A medida que los dispositivos electrónicos portátiles se van imponiendo, las empresas que los fabrican se enfrentan a un reto cada vez mayor para mantener su ventaja competitiva. Es de vital importancia para los fabricantes que cada dispositivo sea eficaz, rentable y refleje la máxima calidad disponible.
Producción en masa de biosensores portátiles:
Para producir en masa y de forma rentable biosensores vestibles, la integración vertical y las operaciones de montaje son fundamentales. Tener la capacidad de imprimir tintas conductoras en sustratos flexibles y realizar completamente las operaciones de conversión (como la laminación de hidrocoloides de grado médico, adhesivos, capas no tejidas y de espuma, dispensación de hidrogeles y/o colocación y empaquetado final) en componentes SMT y cualquier conexión en el lado no paciente del parche (garantiza la comodidad del paciente). Han tenido éxito en el llenado de huecos de 0,010" de diámetro para tener continuidad entre el contacto con la piel y un supuesto dispositivo de comunicación.

Tecnologías utilizadas para la fabricación de biosensores
El proceso de fabricación de biosensores emplea la serigrafía, el corte por láser, la laminación y los adhesivos. La serigrafía de diversas tintas conductoras, como, por ejemplo, plata, plata/cloruro de plata, carbono, zinc, oro, dieléctrico, etc. Además, se utiliza la tecnología de montaje en superficie (SMT) si se necesitan componentes. Hay varios procesos de conversión clave, como el troquelado, la laminación de espumas y adhesivos de grado médico, así como la dispensación y colocación de hidrogeles de grado médico y el embalaje final. El papel de la impresión a través de métodos de agujeros, que permiten conexiones entre los circuitos impresos superiores e inferiores y hasta 6 capas por lado.
En la mayoría de las aplicaciones, la fabricación de biosensores implica una cadena de suministro de empresas, ya que pocas empresas poseen todas las capacidades necesarias. Las funciones requeridas se detallan a continuación:
Impresión de circuitos/electrodos
Hoja o R2R
Normalmente, de 2 a 5 pases de impresión
Secado en horno o curado UV después de cada pasada de impresión
Tiempo de permanencia en el horno normalmente ≤10 minutos ≤140°C
Es posible que se requiera una lámina deslizante o intercalada para evitar el desprendimiento de la tinta, ya que las tintas de carbono tienden a ser blandas y se transfieren al reverso del sustrato cuando se apilan o enrollan en rollos
Mediciones rutinarias durante el proceso para confirmar la conformidad con las especificaciones dimensionales, de espesor de la tinta y eléctricas acordadas.
Estampado de la capa espaciadora/adhesiva
Uno o una combinación de SRD, Rotary, Match Metal y/o Láser
Estampado de la tapa o de la capa superior
Igual que el espaciador/adhesivo
Dispensación y secado/acondicionamiento del material funcional
Aquí es donde existe la mayor parte de la propiedad intelectual (PI) y a menudo la realiza el OEM. Esta situación está cambiando a medida que los convertidores médicos añaden la capacidad de dispensación en un esfuerzo por añadir valor.
Laminado
En frío con adhesivo sensible a la presión (PSA) o en caliente (hot melt)
Realizado por el OEM o el convertidor
Opción: configuración tipo cartucho o casete
La aplicación puede omitir el proceso de laminación y, en su lugar, troquelar los circuitos individuales de los sensores e instalarlos en un cartucho o casete de microfluidos de plástico moldeado por inyección.
Hoja/rollo a tarjetas
Formato grande recortado a formato de tarjeta rectangular (sensores anidados 1 fila x TBD a través) para la compatibilidad con el equipo de singulación de tiras disponible en el mercado
Singulación
Los sensores individuales suelen cortarse de las tarjetas para formar tiras de prueba individuales
Embalaje
Las tiras de prueba singuladas se colocan en viales de plástico, a menudo con las paredes interiores revestidas con un desecante. Se instala un tapón de rosca o a presión, seguido de la aplicación de una etiqueta
[This is automatically translated from English]
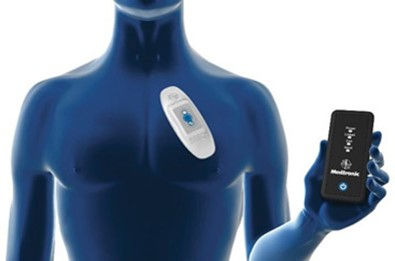
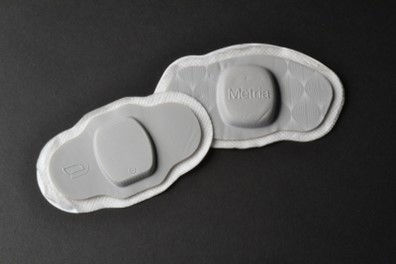