
The technology for integrating dies is one of the key enablers for the realization of new applications in flexible hybrid electronics (FHE), e.g. in in-mold electronics or smart glass.
Using inkjet printing technology, DoMicro has developed a state-of-the-art approach for micro assembly. This approach enables the realization of demonstrators of advanced applications with for example ICs, passive components, sensors and LEDs. An example, described in this paper, is the demonstrator for wireless IoT devices with touch sensors and a Bluetooth chip. With the integration of ultra-thin bare dies, the total height of the demonstrator is below 0.7 mm. This thin form-factor enables smooth integration of functionality in various surfaces, labels, fabric etc.
The inkjet printing technology brings several important capabilities, such as seamless and invisible integration, integration of thinned bare dies on flexible substrates and a reduced number of process steps.
Configurations for die bonding and contacting
A first step for the realization of the wireless IoT demonstrator was the investigation of the optimal configuration for die contacting and bonding.
Several configurations have been studied. Figure 1 is showing a Fan In Ball Grid Array (BGA) configuration by inkjet printing on bare die. An inkjet-printed dielectric is covering the die while keeping the areas at the contact pads open. Next on top silver ink is connecting the bond pads to a BGA pattern on top of the dielectric coating. Alignment and registration of structures are performed through the automatic vision system of the used PixDRO LP50 laboratory printer equipment.
Figure 2 shows the flip-chip bonding of a bare die to an inkjet-printed silver pattern. For interconnection, high accuracy alignment die bonding equipment is used.

Figure 1. Fan In Ball Grid Array printed on die
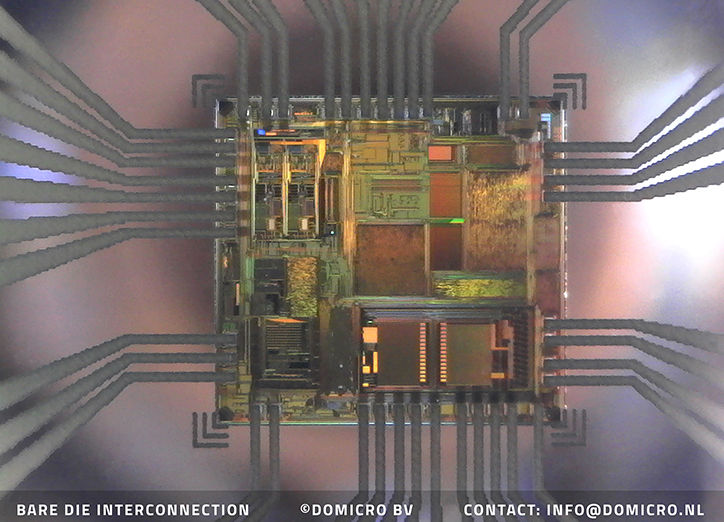
Figure 2. Flip Chip bonding on printed tracks (through substrate view)
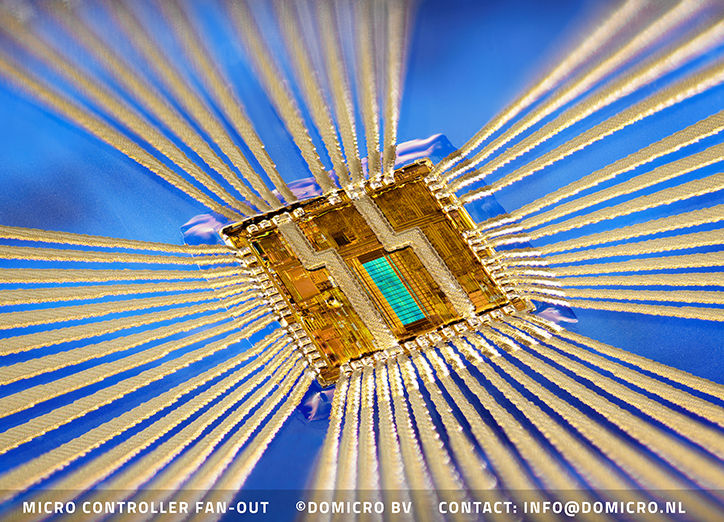
Figure 3. Fan Out Die first face-up
Figure 3 is showing the face up thinned bare die of a microprocessor being interconnected on the bond pads. As it is impossible to inkjet print conductive tracks via a steep vertical surface, a dedicated ramp structure is provided to guide and support the inkjet-printed silver conductors. This innovative approach of contacting is avoiding any regular and height consuming wire bond loops with glob top or as applied in advanced packaging, a redefinition layer or substrate (RDL) interface. This ‘die first’ approach is creating minimal height for assembling and mounting dies in systems. It enables a good optical alignment of the die before integration and offers a compatibility of material surface interaction. From the three configurations as described above, the innovative face up ‘die first’ technology was chosen for the realization of a flexible hybrid electronic (FHE) wireless IoT demonstrator because it was the best fit for this application. It should be noted that it depends on the application which configuration gives the best fit.

Bluetooth Beacon
The next step was to create the Bluetooth functionality. This was done with a Nordic 51822 Bluetooth low energy (BLE) chip, which was available in thinned bare die version. The integration of this chip with printing has been demonstrated in an existing beacon design (see figure 4).
Figure 4. printed BLE beacon
Wireless Flexible Hybrid Electronics interface
Typical for having wireless functionality for IoT devices is the combination and integration of a sensing function, computing processing and radio functionality for operating and communicating remotely from nodes to the network. In line with this, the final step for the realization of the wireless IoT demonstrator was the integration of a micro controller, a Bluetooth radio Integrated Circuit (IC) and a printed touch sensor on a polyester foil. The micro controller (a thinned Cypress CY8C20 touch controller) has been integrated in the same way as the BLE chip. For sake of demonstration, powering the demonstrator has been addressed with a regular cell battery. It is understandable that integration of a flat flexible battery solution would top off this wearable flat flexible device. Typical advantage over standard wire bond interconnection is the ability to print functional circuitry on all kinds of thin and bendable substrates. This form-factor enables smooth integration of functionality in various surfaces, labels, fabric etc. Next to that, the ability to integrate a bare die chip face up instead of flip chip, can expose the sensor side of the chip to the outside in an extremely low height package solution.
On the polymer foil, the thinned BLE IC and the thinned touch controller IC are bonded and contacted in a functional circuit and antenna by inkjet printing technology. Additionally, some SMDpassive components were added as well. Powered with the external cell battery this demonstrator is able to show two-way bluetooth communication with a cellphone app.

The high accurate inkjet-printed traces are aligned and connected to the fine pitch (60 micron track/gap) bond pad of the IC’s. Passives used are approximately 0,5mm thick (height) as this is commonly available in SMD components. Figure 5 is showing the layout of touch area and electronic circuitry for both MC and BLE including the antenna structure.
After powering and testing with the Nordic Blinky app, the functionality is shown while interaction is initiated from the demonstrator device back and forth. The touch area is changing the status message in the app. Touch function is activated by a manual touch area on the sample, the state of the button is shown on the wireless interface. The LED can be switched on/off remotely and activated by a switch on the app.
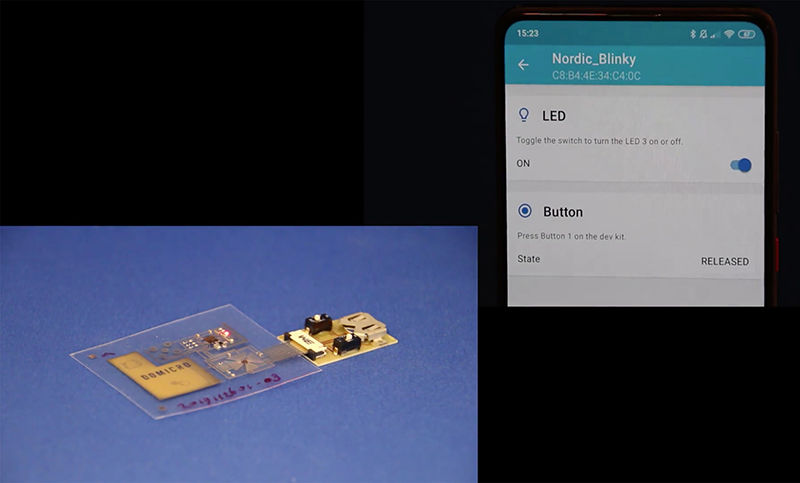
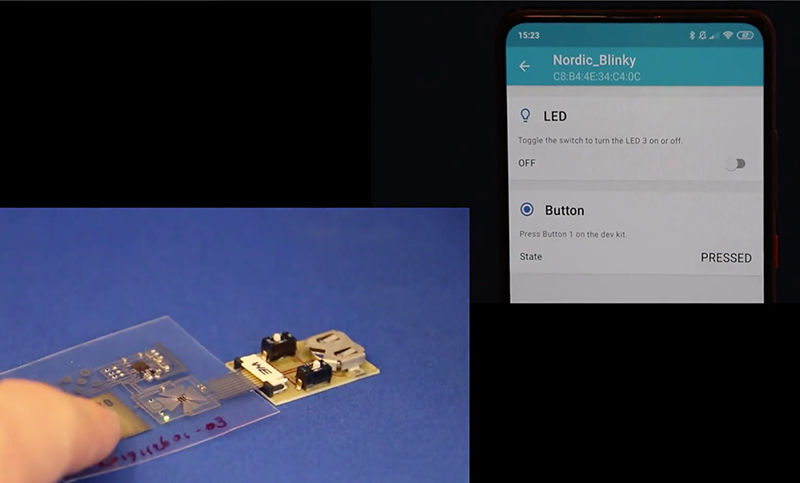
Figure 6. LED on, button released Figure 7. LED off, button pressed
You can check out the demonstrator video via
Conclusions & Outlook
DoMicro has demonstrated that bare dies can be integrated in flexible substrates using inkjet printing for the contact. This is achieved with a dedicated ramp structure for guiding and supporting the printed silver conductors. This innovative approach of contacting eliminates the need for height consuming wire bond loops. The approach has been demonstrated in a Flexible Hybrid Electronics application with thin bendable Bluetooth electronics that can be laminated in a thin flexible and/or wearable product or application.
The thin form-factor enables smooth integration of functionality in various surfaces, labels, fabric, in-mold devices, smart glass, etc. Furthermore, the ability to integrate a bare die chip face up instead of flip-chip, can expose the sensor side of the chip in an extremely low height package solution.
The target group for the demonstrated technology includes application developers in several industry sectors like automotive, transport and logistic companies, and medical device companies, but also in science, aerospace and other applications that might have a need for new ways of integrating electronic functionality in products and structures.
Imagine, Create, Accomplish
DoMicro BV is a technology company providing innovative manufacturing technology, application solutions and micro-assembly technology for flexible hybrid electronics (FHE) and microdevices. DoMicro develops cutting edge inkjet printing processes and technology for micro-assembly and 3D packaging. At the forefront of innovation, DoMicro offers state-of-the-art R&D services and exploration of new capabilities and applications for customers with manufacturability in mind. The company delivers R&D services, small series production, system architecture and project management. Typically for customers exploring new technologies for circuitry on flexible substrates like transparent conductive films, OPV electrodes, OLED, Lab-on-chip, wearables, in-mould electronics, IC and MEMS integrations.
Innovations Festival:
Printed, Hybrid, 3D, InMold, Textile Electronics
Limited Free Spots Available

Comentários