Drucken in Si PV, dehnbare Substrate, autonomes Drucken, Low-T-Tinten
Dieser Artikel gibt einen Überblick über verschiedene Technologien in der Welt der additiven Elektronik, wie z. B. rollende Nanolithographie, Sinterung/Reflow mit intensivem Licht, Trends und Roadmap für die Metallisierung der Vorderseite bei Si-PV, SMT-kompatible dehnbare Susbtrate, autonome Beschichtung und Druck, Niedertemperatur-Silber-NP-Tinten usw.
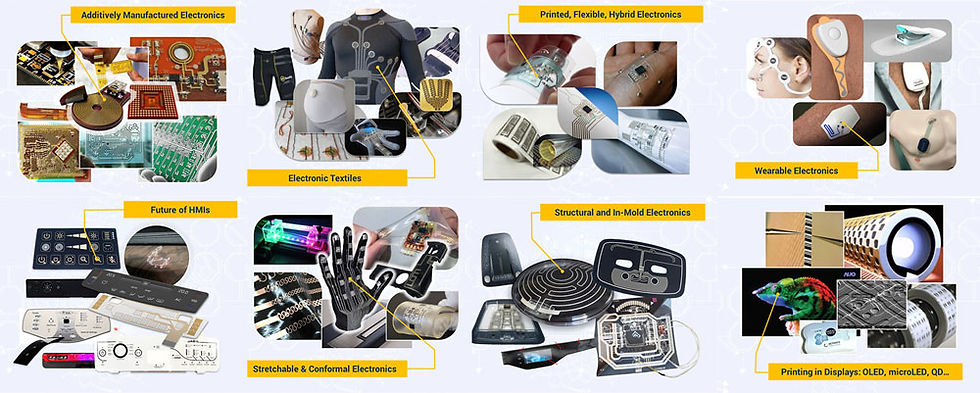
Bitte besuchen Sie unser Innovationsfestival am 24. Juni 2022 (online), wo diese und viele weitere interessante Technologien vorgestellt werden. Sie können uns auch vor Ort in Eindhoven (12.-13. Oktober 2022) besuchen, um die globale Gemeinschaft persönlich zu treffen. Weitere Informationen finden Sie hier
Rollende Nanolithographie: Industrielles R2R-Verfahren zur Herstellung von Strukturen im Mikrometer- und Submikrometerbereich
Die rollende Nanolithografie kann die Auflösung der R2R-Lithografie sogar unter 1 um bringen. Diese Technologie von Meta Inc (Meta Materials Inc) umfasst eine Rolle, um die eine Maske gewickelt wird und in der sich ein UV-Licht befindet. Die Maske selbst wird mit Hilfe der Elektronenstrahllithographie hergestellt, wodurch sie sehr feine Merkmale erhält. Daher kann die Maske, wie die Nanoimprint-Technologie, Merkmale im Nanometermaßstab unterstützen. Allerdings kann die UV-Belichtung selbst die Größe der Merkmale auf 500 nm oder 1 um begrenzen.
Die derzeitige Bahngröße beträgt 300 mm, obwohl Meta eine Technologie entwickelt, um diese auf 1200 mm Bahnbreite zu skalieren. Hier kann ein Step-and-Repeat-Verfahren eingesetzt werden, um größere Rollmasken zu erzeugen (Achtung: Es können einige 100um breite Diskontinuitäten entstehen, die nicht ganz nahtlos sind, aber es gibt Abhilfemaßnahmen dafür).
Um eine einlagige Feinstleiter-Metallisierung zu erreichen, wird zunächst ein Fotolack aufgetragen und dann mit der UV-Rollmaske strukturiert. Anschließend wird eine dünne Metallschicht R2R-bedampft (z. B. AI oder Ag), bevor das endgültige Muster in einem R2R-Lift-off-Verfahren erzeugt wird. Es können sehr feine Strukturen mit einem hervorragenden Aspektverhältnis (300nm/100nm) erzielt werden.
Dabei handelt es sich um ein industrielles R2R- oder R2S-Breitbandverfahren, mit dem wenige Mikrometer oder sogar Submikrometer-Merkmale auf 1,2 m breite Bahnen mit einer Länge von 6 km und einer Druckgeschwindigkeit von 2-10 m/min gedruckt werden können.
Die eingebetteten Folien zeigen Produktbeispiele. Auf Folie 2 sehen Sie die Beispiele für die erreichten feinen Strukturen, womit die Technologie in den gleichen Größenbereich wie Silbernanodrähte fällt. Auf Folie 3 sehen Sie die Demonstration von Al- und Ag-Metallgeweben mit L/S von 500 nm/30 um, die 3,5-5 Ohm/qm bei 96 % Transparenz erreichen. Das Bechmarking-Diagramm zeigt, dass diese Nanoweb-Technologie alle anderen Optionen in Bezug auf ihren geringen Schichtwiderstand und ihre hohe Transparenz übertreffen kann.

Metallisierung in der Photovoltaik: State-of-Practice, Stand der Technik und Industrie-Roadmap
Die Silizium-Photovoltaik (PV) ist weltweit einer der wichtigsten Märkte für gedruckte Elektronik. Das liegt daran, dass auf jedem Wafer ein kleines Stück Siebdruck-Silberpaste aufgebracht ist. In der Tat könnte dies der größte Markt weltweit sein.
Tas nachstehende Diagramm - aus der Roadmap ITRPV 2022 des Ministeriums - zeigt die Menge der pro Wafer verwendeten Ag-Metallisierung (sowohl Vorder- als auch Rückseitenmetallisierung) pro Watt je nach Art der Silizium-Photovoltaik (monofacialer p-Typ, TOPCon n-Typ, HJT n-Typ usw.). Daraus geht hervor, dass heute etwa 25-30 Tonnen pro GW Solarenergie für HJT n-Typ PV und etwa 12-14 Tonnen für monofaciale und bifaciale Typen verwendet werden. In Anbetracht der Größe des PV-Marktes entspricht dies einem Markt von über 100 Tonnen pro Jahr!
Wie aus den nachstehenden Diagrammen hervorgeht, ist der Siebdruck nach wie vor die vorherrschende Technologie für die Metallisierung, obwohl andere Technologien seit langem versuchen, auch nur eine kleine Delle in diesen Bereich zu machen. Langfristig ist zu erwarten, dass andere Technologien wie die Beschichtung auf der Saatschicht oder der Schablonendruck ein wenig Fuß fassen werden, obwohl wir diese Geschichte schon zu oft gehört haben.
Es gibt verschiedene Siebdrucktechniken. Einzeldruck und Doppeldruck (Finger und Busbar werden in zwei separaten Schritten gedruckt) sind die gängigsten Techniken. Der Doppeldruck (Druck einer zweiten Schicht auf ein bereits gedrucktes Sieb für ein besseres Seitenverhältnis) ist ebenfalls sehr beliebt. Der Vorteil des Doppeldrucks besteht darin, dass für die Finger und die Stromschienen unterschiedliche Pasten verwendet werden können, was zu optimalen Ergebnissen führt.
Es gibt natürlich immer einen Trend, die Linienbreite der im Siebdruckverfahren hergestellten Leitungen zu verringern, während gleichzeitig ein hohes Seitenverhältnis, ein ausgezeichneter ohmscher Kontakt und eine hohe Leitfähigkeit beibehalten werden. Dies ist seit Jahren die Richtung der Entwicklung. Heute ist der Stand der Technik in der Produktion eine Siebdrucklinienbreite von etwa 34-35 um. Die Industrie erwartet, dass sich dies bis zu einer Linienbreite von 20 um entwickeln wird, was für den Siebdruck sehr schmal ist und einen echten Fortschritt darstellen würde.
Auf der Folie unten sehen Sie ein Beispiel vom Fraunhofer ISE (2019), das einen Siebdruckfinger mit einer Linienbreite und Höhe von 19 um bzw. 18 um zeigt. Dies ist meiner Meinung nach der Stand der Technik und erfordert eine enge Zusammenarbeit aller Beteiligten, von den Herstellern rostfreier Gewebe über die Pasten- und Partikelhersteller bis hin zu den Emulsionsherstellern und so weiter.
Dies ist ein unglaublich wichtiger Markt für die gedruckte Elektronikindustrie. Außerhalb Chinas sind die wichtigsten Partikelhersteller nach wie vor Dowa, Ames Goldsmith, Metalor und Technic. Es gibt viele Hersteller von Pasten, darunter Heraeus, DuPont, usw. Da sich der Markt in China befindet, hat sich natürlich auch die Lieferkette dorthin verlagert, wobei die chinesischen Anbieter sowohl in Bezug auf ihren Marktanteil als auch auf ihre technologischen Fähigkeiten zunehmen. In der Tat stehen ihre Pulver und Pasten dem Stand der Technik nicht mehr wesentlich nach.
Um ihren Marktanteil zu sichern, müssen andere ihre Partikel-/Pulver- und Pastentechnologie so weiterentwickeln, dass sie den Weg zu immer schmaleren gedruckten Linienbreiten ohne Effizienzverluste mitgehen können. Dies ist eines der Leitprinzipien für die Technologieentwicklung.
Schließlich veröffentlicht das Fraunhofer ISE einen ausgezeichneten und sehr detaillierten Jahresbericht über den Zustand der weltweiten Photovoltaikindustrie. Wie unten dargestellt, beläuft sich die weltweite Produktion bereits auf über 140 GW/Jahr, wobei 82 % in Asien produziert werden.
Um das Ausmaß dieser Industrie zu unterstützen, muss jede Metallisierungstechnologie einen hervorragenden Durchsatz aufweisen. Die ITRPV-Roadmap 2022 skizziert auch den Durchsatz für die Backend-Schritte. Sie zeigt, dass Siebdruckmaschinen heute etwa 7000 Wafer pro Stunde (180 x 182 mm2) verarbeiten. Es wird erwartet, dass dieser Wert in einem Jahrzehnt auf über 9000 Wafer pro Stunde ansteigen wird. Dies wird hier aufgenommen, um das Ausmaß der Herausforderung zu verdeutlichen, der sich alternative Verfahren, einschließlich berührungsloser Technologien wie Inkjet, gegenübersehen.
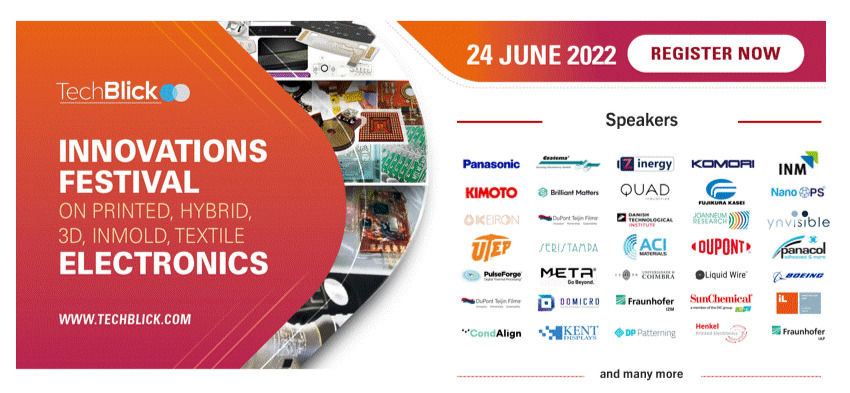
Intensives Pulslicht: Schnelles und energiearmes Löten auf PET und FR4
Das Löten auf flexiblen Substraten war eine Herausforderung, da selbst Standard-Niedrigtemperaturlote auf Wismutbasis nicht mit Substraten wie PET oder sogar hitzestabilisiertem PET kompatibel sind, die keine hohen Temperaturen vertragen.
Um diese Herausforderung zu meistern, setzen viele auf leitfähige Klebstoffe. Dies ist eine gute Lösung, hat aber mehrere Nachteile: (1) man vermisst die automatische Selbstausrichtung des Lötmittels, die ein wesentliches Merkmal bei SMT-Prozessen ist; (2) leitfähige Klebstoffe können zum Gesamtwiderstand beitragen, wodurch die flexible Hybridelektronik noch weiter von den standardmäßigen PI-basierten FPCB-Techniken entfernt ist (geringere Leitfähigkeit der gedruckten Tinte im Vergleich zu losem Kupfer plus geringere Leitfähigkeit der leitfähigen Klebstoffverbindungen im Vergleich zu Standardlötmitteln); und (3) enge Pitch-Größen werden schwer zu unterstützen sein.
Die von Pulse Forge Inc. (ausgegliedert aus NovaCentrix) entwickelte digitale Wärmeverarbeitung bietet eine Lösung. Wie unten gezeigt, erhöht ein schneller Lichtimpuls die Oberflächentemperatur des Substrats sehr schnell, während das Substrat selbst relativ kühl bleibt, was das Sintern von Druckfarben auf Niedrigtemperaturen wie PET und Papier ermöglicht.
Diese Eigenschaft wurde bereits ausgiebig in Verbindung mit Druckfarben genutzt. Unglaublicherweise wurde kürzlich gezeigt, dass es auch mit Lot funktioniert. Die zweite Folie zeigt, wie die PulseForge-Technologie in weniger als einer Sekunde Standard-SAC305-Lot aufschmelzen kann, wobei gute Verbindungen entstehen und auch die automatische Neuausrichtung des Lots genutzt wird.
Die nächste Folie zeigt, wie die PulseForge-Technologie zum Löten auf Al auf PET eingesetzt werden kann, was zum Beispiel die R2R-Produktion von LED-Folien auf Al-metallisiertem PET-Substrat ermöglicht.
Interessanterweise kann diese Technologie auch auf FR4-Substrate angewendet werden. Hier gibt es zwei entscheidende Vorteile: (1) schnelles Reflow in nur wenigen Sekunden (1-3s), was Zeit spart (der Standard-Reflow-Prozess dauert beispielsweise 120s bei 235C), und (2) energiesparendes Reflow mit 10 % der Energie, die für Standard-Reflow-Öfen benötigt wird, was den Prozess umweltfreundlicher" macht.
Die Folie unten zeigt, dass die Scherfestigkeit der Lötverbindungen, die mit der intensiven Pulslichttechnologie und der Standard-Reflow-Ofentechnologie hergestellt wurden, vergleichbar sind. Das nächste Dia zeigt, dass die Verbindungen von hoher Qualität sind, mit einem sehr geringen Hohlraumgehalt und dass eine gute dünne intermetallische Schicht nach dem Pulslicht-Reflow gelötet wird.
Kann man auch Verbindungen löten, bei denen keine direkte Sichtverbindung besteht? Die Ergebnisse von QFN- und anderen Gehäusen, bei denen die Lötstellen nicht direkt sichtbar sind, zeigen, dass dies möglich ist, auch wenn es nach unserer Einschätzung noch einer erheblichen Optimierung bedarf.
Wir gehen sogar davon aus, dass ein erhebliches Know-how des Bedieners erforderlich ist, um die Belichtungsparameter auf der Grundlage des Lots, des Substrats und der Gehäuse auf einer Leiterplatte zu optimieren, um intensives Pulslichtlöten zu ermöglichen, da es sich immer noch um eine nicht standardisierte SMT-Reflow-Technologie mit einer neuen Lernkurve handelt.
Beachten Sie, dass die Inline-Versionen der PulseForge-Maschinen 300 m breite Substrate verarbeiten können. Das sind fantastische Ergebnisse. Das Werkzeug löst ein wichtiges Problem in der flexiblen Hybridelektronik. Angesichts seiner Schnelligkeit und seines geringen Energiebedarfs kann es auch im allgemeinen SMT-Geschäft auf Standardsubstraten wie FR4 einen bedeutenden Einfluss haben. Die Auswirkungen in der SMT-Welt werden jedoch nicht über Nacht eintreten, da sich die Technologie noch bewähren und weiterentwickeln muss, um zu einem Standardprozess zu werden, insbesondere wenn sie jemals den etablierten Reflow-Prozess ersetzen soll, der alle Lote auf komplexen, großformatigen Leiterplatten mit einer Vielzahl von IC- und Verbindungstypen verarbeiten kann.
Dehnbares, flexibles Substrat, das mit SMT-Verfahren kompatibel ist und die Aushärtung von Tinte bei hohen Temperaturen ermöglicht
Die derzeitigen Substrattechnologien schränken das Potenzial der dehnbaren oder flexiblen Hybridelektronik stark ein. Dies liegt daran, dass (a) sie häufig die Aushärtungstemperatur von leitfähigen Tinten begrenzen, wodurch die Leitfähigkeit weit unter der von Bulk-Metall liegt, und (b) sie die Kompatibilität mit Standard-SMT-Prozessen und -Materialien wie dem Reflow-Löten ausschließen.
Die nachstehende Tabelle enthält einen Vergleich der gängigen flexiblen und dehnbaren Substrate. Das gebräuchlichste "flexible" Substrat ist PET, das kostengünstig und chemikalienbeständig ist und eine gute Oberflächenenergie für den Druck von Druckfarben bietet. Es hat jedoch eine schlechte Wärmebeständigkeit, was es im Allgemeinen mit SMT-Verfahren inkompatibel macht und Temperaturbeschränkungen für die Aushärtung der Tinte mit sich bringt, wodurch die erreichten Leitfähigkeitsstufen begrenzt werden können.
Das gebräuchlichste "dehnbare" Substrat ist TPU, das sich hervorragend dehnen lässt und eine gute Oberfläche zum Bedrucken bietet, aber sehr hitze- und feuchtigkeitsunempfindlich ist und die Verarbeitungstemperaturen für Tinte und Lot/Leitkleber noch stärker einschränkt als PET.
Daher besteht ein Bedarf an einem Substrat, das flexibel und dehnbar ist und mit SMD- und Hochtemperaturprozessen kompatibel ist. Panasonic entwickelt ein solches Produkt auf der Grundlage eines neuartigen, patentierten, vollständig vernetzten duroplastischen Polymersystems.
Unten sehen Sie einen Dehnungsvergleich, der zeigt, dass das neue Duroplast-Substrat im Gegensatz zu TPU einen 100%igen Dehnungszyklus ohne Verformung übersteht. Auf der nächsten Folie ist zu sehen, wie dieses Substrat einen Lötschwimmvorgang (1m@260C) übersteht, während PET und TPU vollständig beschädigt werden. Dies zeigt deutlich die bessere Kompatibilität mit Standard-SMT-Verfahren. Als Nächstes sehen Sie die thermische Stabilität der Folie - sie behält ihre Dehnungs- und Zugeigenschaften auch nach 1000 Wärmezyklen (-55 C bis 125 C) bei.
Um einige Anwendungen zu demonstrieren, haben sie Cu-Tinten bei 230 °C gesintert, um hochleitende Kupfertinten herzustellen. Sie demonstrierten auch eine dehnbare LED-Folie zusammen mit dehnbaren Ag-Tinten.
Es handelt sich natürlich um ein relativ frühes Stadium. Kosten- und Mengenfragen müssen noch geklärt werden, die Pastenhersteller müssen möglicherweise die Pastenformulierungen anpassen, um dieses Substrat gut bedrucken zu können, und die Drucker müssen lernen, wie sie dieses Substrat verarbeiten können.
Nichtsdestotrotz ist dieses Substrat vielversprechend, da es leitfähigere Pasten und SMT-Verfahren ermöglichen kann. Es ist keine Lösung, die nach einem Problem sucht, und entspricht eindeutig einem Marktbedarf.

Auf dem Weg zu autonomen Beschichtungs- und Druckmaschinen?
Die Coatema Coating Machinery GmbH hat spannende Entwicklungen aufgezeigt, die den Weg zu autonomen, selbstoptimierenden Beschichtungs- und Druckmaschinen innerhalb der nächsten zehn Jahre weisen.
Wie unten zu sehen ist, entwickelt Coatema Druck- und Beschichtungssysteme mit mehreren Stationen, die R2R-Schlitzdüsenbeschichtung, Tintenstrahldruck, Trocknung, Laserbearbeitung, Sinterung mit intensivem Licht, Auf- und Abwickeln usw. inline integrieren. Das folgende Beispiel ist eine Maschine, die bei OET - Organic Electronic Technologies P.C. in Griechenland installiert wurde.
Natürlich sind Druck und Beschichtung komplexe Technologien mit einer großen Anzahl von Parametern. Nachstehend sind nur einige der Parameter aufgeführt. Daher kann die Produktentwicklung und der Übergang vom Labor zur Fertigung zeitaufwendig und anspruchsvoll sein, da das Finden und Aufrechterhalten optimaler Druck-, Beschichtungs-, Trocknungs- und Sinterbedingungen in einem solch komplexen mehrstufigen System eine große Herausforderung darstellen kann, insbesondere beim Drucken von mehrschichtigen Bauteilen oder Strukturen und beim Übergang vom Labor zur Fertigung.
Coatema integriert jetzt mehrere Messpunkte inline in seine Maschinen (siehe unten). Das Ergebnis sind Millionen von Datenpunkten pro Minute, die in jeder Phase des Prozesses Aufschluss geben.
Um aus all diesen Datenpunkten einen Sinn zu machen, entwickelt Coatema zusammen mit seinem Partner Panda KI-Algorithmen, die zum Beispiel eine automatische Identifizierung der Position von Anomalien auf den beschichteten oder bedruckten Oberflächen ermöglichen. Diese automatische KI-basierte Anomalieerkennung kann auch in den Zeitreihen durchgeführt werden, so dass sowohl der Ort als auch der Zeitstempel des anomalen Beschichtungs- oder Druckschritts identifiziert werden kann. Um solche Anomalien zu erkennen, analysiert der Algorithmus, wie unten zu sehen, ständig die Daten, die aus den voll integrierten Druck- und Beschichtungsmaschinen mit mehreren Stationen kommen.
Diese Entwicklungen von Coatema zeigen die zukünftige Entwicklung von Druck- und Beschichtungsmaschinen. Dieses Niveau an Einblicken wird eine beschleunigte Produktentwicklung, Optimierung und den Übergang vom Labor zur Fertigung sowie eine ausgezeichnete gleichmäßige Qualitätserhaltung über große Produktionsläufe ermöglichen.
Langfristig gesehen wird damit der Grundstein für autonome, sich selbst optimierende Druckmaschinen gelegt, die mit wenig menschlichem Eingriff optimale Druckbedingungen finden und aufrechterhalten.
Ag-Nanopartikel-Tinten: Immer höhere Leitfähigkeit bei geringerer Aushärtungszeit und Temperatur
Druckfarben mit Silbernanopartikeln werden jedes Jahr verbessert. Diese Verbesserungen sind oft schrittweise, aber sehr wichtig. Die Entwicklung geht immer weiter in Richtung von Tinten, die bei niedriger Aushärtungstemperatur und kurzer Aushärtungszeit eine immer höhere Leitfähigkeit bieten. Dies ist ein entscheidender Vorteil, da dadurch mehr Substrate zur Verfügung stehen, Zeit gespart wird und die Energiekosten gesenkt werden.
Im Folgenden werden die Fortschritte von Agfa hervorgehoben, das sowohl lösemittel- und wasserbasierte als auch sieb- und inkjetgedruckte (IJ) Ag-Nanopartikelfarben anbietet. Die erste Folie unten zeigt den Fortschritt bei der Aushärtungszeit und -temperatur einer lösungsmittelbasierten IJ-druckbaren Ag-Nanopartikelfarbe. Das linke Bild ist die vergrößerte Version des rechten Bildes. Hier werden die Eigenschaften von zwei verschiedenen lösungsmittelbasierten IJ-Ag-NP-Tinten verglichen: SPS201 und SPS210, gesintert bei verschiedenen Temperaturen (110C, 130C und 150C).
Bei einer gegebenen Sintertemperatur ist zu erkennen, dass SPS210 im Vergleich zu SPS201 in kürzerer Zeit einen niedrigeren spezifischen Widerstand erreicht, was deutlich diesen schrittweisen, aber wichtigen Fortschritt der Ag-NP-Tintentechnologie zeigt. Wie auf der folgenden Folie zu sehen ist, erreicht die Ag NP IJ-Tinte SP2010 einen Wert von 3 mOhm/sqr/mill, wenn sie bei nur 130 °C für 10 Minuten gesintert wird. Dies sind hervorragende Ergebnisse.
IJP Ag NP-Tinten beginnen, geeignete Anwendungen zu finden. Auf der letzten Folie sehen Sie gedruckte Ag NP-Linien als schmale (70um) Metallisierungslinie auf einer Dünnschicht-Photovoltaik-Technologie (Anmerkung: Siebdrucklinien auf Si-PV sind jetzt 34um). Daneben sehen Sie eine transparente Heizanwendung.
Hier handelt es sich um ein photochromes Laminat für Motorsportvisiere. Das Visier kann die optische Durchlässigkeit verändern, um bei unterschiedlichen Lichtverhältnissen im Freien eine gute Sicht zu gewährleisten. Eine Einschränkung des photochromen Laminats ist, dass es seinen Transparenzzustand nur langsam ändern kann. Dies kann eine Herausforderung darstellen, wenn der Fahrer z. B. in einen Tunnel einfährt und der Übergang von intensivem Sonnenlicht in die Dunkelheit schnell erfolgt. Um diese Einschränkung zu überwinden, kann das Laminat erhitzt werden, um den Übergang zu beschleunigen. Zu diesem Zweck wird eine CNT- oder ITO-Lösung eingesetzt. Die Ergebnisse sind in Ordnung, aber die homogene Erwärmung kann immer noch zu lange dauern (40 Sekunden oder länger).
Um diese Einschränkung zu überwinden, wird ein Metallgitter mit einer Linienbreite von 70 um und einem Abstand von 2 mm mit Ag-NP-Tinten (SPS211) per Tintenstrahl gedruckt. Wie auf der Folie unten zu sehen ist, reduziert es den Widerstand auf 11 Ohm und erreicht eine gleichmäßige Erwärmung in nur 20 Sekunden, was den Anforderungen entspricht.
[This is automatically translated from English]