Printing in Si PV, Stretchable Substrates, Autonomous Printing, Low-T Inks
This article reviews diverse technologies in the world of additive electronics including rolling nanolithography, intense light solder sintering/reflow, front side metallization trends and roadmap in Si PV, high-T SMT-compatible stretchable susbtrates, autonomous coating and printing, low-temperature silver NP inks, etc.
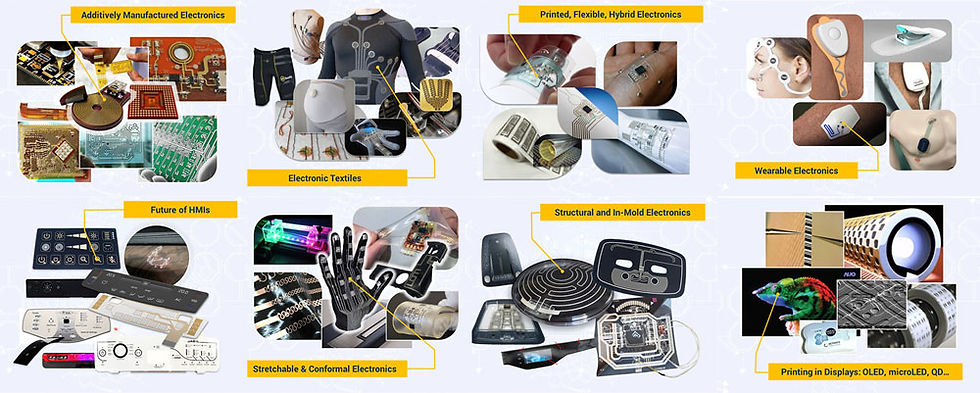
Please do join our Innovations Festival on 24 June 2022 (online) when these and many more interesting technologies will be presented. You can also join us onsite in Eindhoven (12-13 Oct 2022) to meet the global community in-person. Learn more here
Rolling Nanolithography: Industrial R2R process for creating micron and sub-micron feature sizes
Rolling nanolithography can take the linewith resolution of R2R lighography even below 1um. This technology, by Meta Inc (Meta Materials Inc) includes a roller around which a mask is wraped and within which a UV light sits. The wrap-aroud mask itself it manufactured using electron beam lithography, giving it very fine features. Therefore, the mask can support, like nanoimprint technology, nano-meter scale features. However, the UV exposure itself may limit feature size to 500nm or 1um range.
The current web size is 300mm although Meta is developing technology to scale this to 1200mm webwidths. Here, a step-and-repeat process can be used to create larger rolling masks (note: there might be some 100um wide discontinuities and thus may not be fully seamless, although they are workarounds for this).
To achieve single-layer ultrafine line metallizaiton, first a photoresist is deposted and then patterned using the rolling UV mask. Next, a thin metal layer is R2R evaporated (AI or Ag, for example) before creating the final pattern in a R2R lift-off process. Ultra fine features with excellent aspect ratio (300nm/100nm) can be achieved.
This is a wide web industrial R2R or R2S process that can print few micron or even sub-micron features on 1.2m wide webs at lenghts of 6 km and at print speeds around 2-10 m/min speeds.
The embedded slides show examples of products. On slide 2, you can see the examples of fine feature sizes achieved, putting the technology in the same feature size range as silver nanowires. In slide 3, you can see the demonstration of Al and Ag metal mesh with L/S of 500nm/30um achieving 3.5-5 ohm/sqr at 96% transparency. The bechmarking chart shows that this nanoweb technology can outperform all the other options in terms of its low sheet resistance and high transparency.

Silicon photovoltaics (PV) are one of the most important markets globally for printed electronics. This is because each wafer carriers a small of fired screen printed silver paste. Indeed, this could be the largest market worldwide.
The chart below- from the indistry roadmap ITRPV 2022- shows the amount of Ag metallization utilized per wafer (both front and back metallization) per watt depending on the type of silicon photovoltaic (monofacial p-type, TOPCon n-type, HJT n-type, etc). It shows that today something around 25-30 tonnes is used per GW of solar for HJT n-type PV and around 12-14 tonnes for monofacial and bifacial types. Considering the size of the PV market, this translates into a 100+ tpa market!
As shown in the charts below, screen printing remains the prevelant technology for metallization, despite long-term attempts by other technologies to make even a small dent into this space. In the long term future, other technologies such as plating on seed layer or stencil printing are expected to obtain a small foothold, although we have heard this story too many times already.
There are various screen printing techniques. Single print and dual print (finger and bus bar printed seperately in two seperate steps) are the most common techniques. Double printing (print a second layer on an already screen printed already for better aspect ratio) is also popular. The advantage of dual print is that different paste types could be used for fingers and bus bars, giving optimal results.
There is of course always a trend to narrow the linewidht of the screen printed lines, whilst maintaing high aspect ratio, excellent ohmic contact, and high conductivity. This has been the direction of development for years. Today, the state of practice in production is a screen printed linewidth of around 34-35um. The industry expects this to evolve to a linewidth of 20um, which is very narrow for screen printing and would represents a real advancement of the art.
In the slide below, you can see an example from Fraunhofer ISE (2019) demonstrating a screen printed finger with a linewidth and height of 19um and 18um, respectively. This is, in my view, the state of the art, and requires close collaboration of all those involved from stainless mesh makers, to paste and particle manufacturers, to emulsion makers, and so on.
This is an incredibly important market for the printed electronics industry. Outside China, the main particle makers remain Dowa, Ames Goldsmith, Metalor, and Technic. There are many paste makers including Heraeus, DuPont, etc. Of course, given that the market is in China, the supply chain has also been moving there with Chinese suppliers rising in terms of market share as well as technology capabilities. Indeed, their powders and pastes are no longer significantly inferior to the state of the art.
To protect market share, others must evolve their particle/powder and paste technology so that it can sustain the roadmap towards ever narrow printed linewidths without a loss in efficiency. This is one of the guiding principles directing technology development.
Finally, Fraunhofer ISE publishes an excellent and very detailed annual report on the state of the global photovoltaic industry. As seen below, global production is already a staggering 140+ GW/year with 82% being produced in Asia.
To support the scale of this industry, any metallization technology requires to have excellent throughput. The ITRPV 2022 roadmap also outlines the throughput step for the backend steps. It shows that screen printing machines today handle something around 7000 wafers per hour (180 x 182 mm2). This is expected to rise to over 9000 wafers per hour in a decade. This is included here to show the scale of the challenge faced by alternative processes including non-contact technologies such as inkjet.
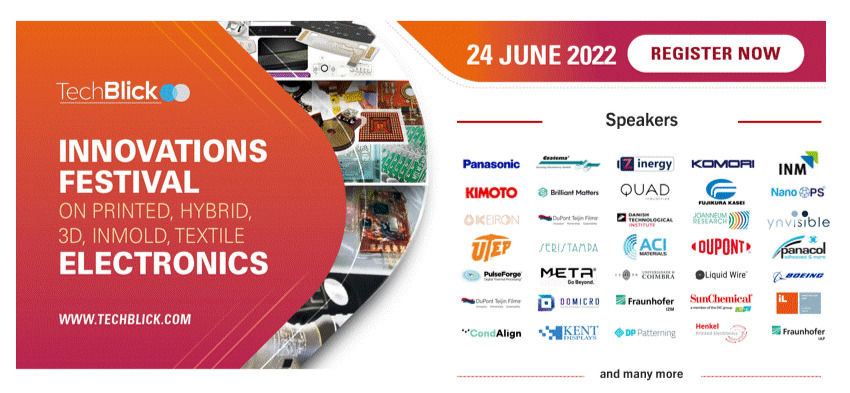
Soldering onto flexible substrates has been a challenge because even standard bismuth-based low temperature solders are not compatible with substrates like PET or even heat stabilized PET which cannot tolerate high temperatures.
To overcome this challenge, many deploy conductive adhesives. This is a good solution but has several shortcoming: (1) one misses the automatic self-alignment feature of solder which is an essential feature in SMT processes; (2) conductive adhesives can contribute to overall resistivity, putting flexible hybrid electronic further beyond standard PI-based FPCB techniques (lower conductivity of printed ink vs bulk copper plus lower conductivity of conductive adhesive interconnects vs standard solder); and (3) narrow pitch sizes will be difficult to support.
Digital thermal processing developed by Pulse Forge Inc (spun off from NovaCentrix) offers a solution. As shown below, a rapid pulse of light raises the temperature of the surface of the substrate very fast, whilst the substrate itself remains relatively cool, allowing one to sinter inks on low-T temperatures such as PET and paper.
This feature has been extensively used in connection with printed inks. Incredibly, it has recently been demonstrated to also work with solder. The second slide shows how the PulseForge technology can in less than a second reflow standard SAC305 solder, creating good joints and also benefiting from solder's automatic realignment feature.
Next slide shows how the PulseForge technology can be deployed to solder on Al on PET, enabling, for example, R2R production of LED foils on Al metallized PET substrate.
Interestingly, this technology can also be applied onto FR4 substrates. Here, there are two crucial benefits: (1) rapid reflow in just a few second (1-3s), saving time (standard reflow process can be 235C for 120s, for example), and (2) low energy reflow at 10% of the energy required for standard reflow ovens, making the process 'greener'.
The slide below shows that the shear strength of the solder joins made with intense pulse light technology and the standard reflow oven technology are comparable. The next slides shows that the joints are of a high quality with very low void content and that a good thin intermetallic layer is solder after pulse light reflow.
Can one can solder joints where no direct line of sight exists? Results on QFN and other packages where joins are not directly visible demonstrate that it is possible, although it will, in our guess, require notable optimization.
In fact, our guess is that significant operator know-how is required to optimize exposure parameters based on solder, substrate, and packages on a board to enable intense pulse light soldering, as it is still a non-standard SMT reflow technology with a new learning curve.
Note that the inline versions of the PulseForge machines can handle 300m wide substrates. These are fantastic results. The tool solves an important problem in flexible hybrid electronics. It can also certainly make a meaningful impact in general SMT business on standard substrates like FR4 given its rapidity and low-energy nature. The impact in the SMT world will not be overnight though as the technology still has to prove and develop itself further to become a standard process, especially if it ever wishes to be a drop-in replacement for the well-established incumbent reflow which can handle all solders on complex large-sized boards containing a vareity of IC and joint types.
Stretchable, flexible substrate compatible with SMT processes & enabling high-temperature ink curing
Current substrate technologies impose severe limits on potential of stretchable or flexible hybrid electronics. This is because (a) they often limit curing temperature of conductive inks which limits conductivity levels far below bulk metal and (b) they rule out compatibility with standard SMT processes and materials such as solder reflow.
The table below is a comparison of common flexible and stretchable substrates. The most common ‘flexible’ substrate is PET, which is low cost, resistant to chemicals, and offers a good surface energy for printing of inks. It however has poor heat resistance, generally making it incompatible with SMT processes and imposing temperature constraints on the curing of the ink, which can limit achieved conductivity levels.
The most common ‘stretchable’ substrate is TPU which offers excellent stretching as well as a good surface for printing, but has very intolerant of heat and humidity, and imposes even more severe constrains on ink and solder/conductive adhesive processing temperatures than PET.
Therefore, there is a need for a substrate that it flexible and stretchable and offers compatibility with SMD and higher temperature processes. Panasonic is developing such a product based on a novel patented fully cross-linked thermoset polymer system.
Below you can film stretch comparison, showing how the new thermoset substrate survives 100% stretch cycle without deformation, unlike even TPU. In the next slide, it can be seen how this substrate survives a solder float operation (1m@260C) whilst PET and TPU are fully damaged. This clearly demonstrates more compatible with standard SMT processes. Next you can see the thermal stability of the film- it maintains its elongation and tensile properties even after 1000 thermal cycles (-55 C to 125C).
To demonstrate some applications, they sintered Cu inks at 230C to form highly conducting copper inks. They also demonstrated a stretchable LED foil together with stretchable Ag inks.
It is of course relatively early stage. Cost and volume questions will need to be addressed, paste makers may need to adjust paste formulations for good printing on this substrate, printers will need to learn how to process on this substrate.
Nonetheless, this substrate is promising because it can enable more conductive pastes and SMT processes. It is not a solution looking for a problem, and clearly addresses a market need

Coatema Coating Machinery GmbH has demonstrated exciting developments, showing a pathway ultimately towards autonomous self-optimising coating and printing machines within the next decade or so.
As can be seen below, Coatema develops multi-station printing and coating systems, inline integrating R2R slot die coating, inkjet printing, drying, laser processing, intense light sintering, winding/unwinding, etc. The example below is a machine installed at the OET - Organic Electronic Technologies P.C. in Greece.
Of course, printing and coating are complex technologies with a large multi-parameter pace. Just some of the parameters are shown below. Therefore, product development and transition from lab-to- fab can be time consuming and challenging since finding as well as maintaining optimal printing, coating, drying, and sintering conditions across such as complex multi-step system can be a significant challenge, particularly for printing multi-layer devices or structures and for lab-to-fab transition.
Coatema now integrates multiple measurement points inline within its machinery (see below). The result is millions of data points per minute as output, giving insights at every stage of the process.
To make sense of all these data points, Coatema, together with partners Panda, is developing AI algorithms, which, for example, enable automatic identification of the location of the anomalies on the coated or printed surfaces. This automatic AI-based anomaly detection can be done in the time series as well, allowing one to identify the location as well as the time stamp of the anomalous coating or printing step. To identify such anomalies, as seen below, the algorithm is constantly analysing the data coming out of the multi-station fully-integrated printing and coating machines.
These developments by Coatema demonstrate the future evolution of printing and coating machinery. This level of insight will enable accelerated product development , optimization and lab-to-fab transition, as well as excellent uniform quality maintenance over large production print runs.
From the long-term perspective, it begins to lay the groundwork for autonomous self-optimising printing machines which find and maintain optimal print conditions with little human intervention.
Ag Nanoparticle Inks: Achieving Ever Higher Conductivity at Lower Curing Time and Temperature
Silver nanoparticle inks improve every year. These improvements are often incremental, but very important. One ever-present direction of development is towards inks which offer ever higher conductivity levels at a low curing temperature and a short curing time. This a critical figure of merit because it opens more substrate choices, saves time, and lowers energy consumption costs.
Here, we highlight the progress by Agfa, who offers both solvent and water based, as well as screen and inkjet printed (IJ) Ag nanoparticle (NP) inks. The first slide below shows the progress in curing time and temperature of a solvent-based IJ printable Ag NP inks. The left picture is the zoomed up version of the right picture. The compares the properties of two different solvent based IJ Ag NP inks: SPS201 and SPS210 sintered at different temperatures (110C, 130C, and 150C).
For a given sintering temperature, we can see that SPS210 reaches a lower resistivity level at a shorter time compared to SPS201, clearly demonstrating this incremental but important advancement of the Ag NP ink technology. As seen in the following slide, the SP2010 Ag NP IJ ink can achieve 3mOhm/sqr/mill when sintered at just 130C for 10min. These are excellent results.
IJP Ag NP inks are beginning to find suitable applications. In the last slide, you can see printed Ag NP lines as narrow (70um) metallization line on a thin film photovoltaic technology (note: screen printed lines on Si PV are now 34um). Next to it, you can see a transparent heater application.
Here, the application is a photochromic laminate for motor sport visors. The visor can change optical transmission to maintain good visibility in different outdoor light levels. One limitation of the photochromic laminate is that it can change its transparency state only slows. This can be a challenge when the driver enters, for example, a tunnel, transitioning from intense sun light into darkness quickly. To overcome this limitation, the laminate can be heated to accelerate the transition. To this end, a CNT or ITO solution is deployed. The result are ok however homogeneous heating can still take too long (40s or longer).
To overcome this limitation, a metal mesh with linewidth of 70um and pitch of 2mm is inkjet printed using Ag NP inks (SPS211). As seen in the slide below, it reduces resistance to 11ohm, and achieves uniform heating in just 20s, which meets requirements.
Comments