(以下、テキストは自動翻訳)
低温はんだ付け
最初のトピックは、低温はんだ付けです。フレキシブルプリント基板について考えてみると、実は多くのフレキシブルプリント基板は基板をベースにしていることに気づかれるでしょう。その理由のひとつは、PIが比較的高い温度に耐えられるため、はんだ付けの自動リフロープロセスが可能になるからです。
もちろん、PETにもはんだ付けはできますが、通常は手作業で行います。手作業で行う場合、はんだ付けプロセスの温度プロファイルをよりよく制御し、PETの制約を超えないようにすることができるからです。
しかし、現在では、PETのような基板にはんだ付けするための非常に興味深いアプローチがいくつかあります。この会社は、パルス照明システムをはんだ付けに導入し、接合部に大量の光を照射することで、実際の基板が高温にならずにパルス光で接合部を形成することができるのです。
さらに興味深いのは、焼結プロファイルを最適化すれば、このプロセスをミリ秒単位で実現できることです。つまり、PETなどの基板に、高スループットでロールtoロールのはんだ付けができるようになるのです。
このスライドの真ん中に、もう一つ非常に興味深いイノベーションが示されています。アイオワ州立大学です。
これを商品化しているのは、Safi-Techというスタートアップ企業です。彼らが開発しているのは、わずか120℃でPETに塗布できるSAC305マイクロカプセルソルダーです。
これは、はんだの特性と自動セルフアライメント機能を組み合わせることができるということで、低温の基板でも正確な位置決めをする必要がないため、ピックインプレースの負担が軽減され、非常に興味深いものです。
このように、ロールtoロールでメタライズし、ロールtoロールでピック&プレイスし、かなり高速に、しかも低温でハンダ付けできるため、フレキシブルなハイブリッド電子機器が実現に近づいているのです。
しかし、導電性接着剤もまた、多くの興味深い傾向を示しています。ここで注目したいのは、CondAlign社の製品です。CondAlignは、非常に興味深いプロセスを持っています。電界を利用して、ホスト内部のフィラーを垂直方向に整列させる、つまりチェーンを形成させるのです。その結果、フィラーをそれほど多く配合しなくても、熱伝導性や電気伝導性に異方性を持たせることができるのです。この種の導電性接着剤では、高価なのはフィラーであることが多いのです。ですから、フィラーの量を80〜90パーセントも減らすことができるのです。
右側がその例です。上側には、ホストの中にある粒子がランダムに分散しているのが見えます。2枚目の右側の真ん中の画像では、電界をかけて粒子を垂直に整列させているのがわかります。これは、同じ性能あるいはそれ以上の性能を得るために必要な量を減らすためです。
そして、下の画像にあるように、これはシート状にすることができます。これはもうロールtoロールで行われます。シートの厚みは、お客様のご要望に応じて変更することができます。また、ピッチ密度も優れており、現在ではプロセスのスケールアップが進んでいます。
これは、既存のオプションを上回る、あるいは少なくともそれに匹敵する性能を持ちながら、コスト削減に貢献できる興味深い技術革新だと思いますので、ぜひ検討してみてください。

大面積照明におけるプリンテッドエレクトロニクス
もうひとつの興味深いトレンドは、大面積LED照明におけるプリンテッドエレクトロニクスです。もちろん、LED照明にはプリンテッドエレクトロニクスやプリント回路、メタライゼーションが適用されてきました。
左の写真にあるように、これはKundischという会社の製品ですが、表面にカスタマイズされたパターンを作り、そのカスタマイズされたパターンにLEDを配置することができるというのが、大きな利点です。つまり、フレキシブル基板や大型基板にプリントした回路で、思い通りの形状やデザインを実現することができるのです。
もう一つ興味深いのは、これは以前からあるトレンドだということです。少なくとも4、5年前から商品化している企業がありますが、今は勢いがあり、ロールtoロールで何でもできるようになっています。
プリンやメタライゼーション、部品に付属する材料をロールtoロールし、LEDをフレキシブル基板にロールtoロールで組み付けることで、優れたスループットを実現します。これは、フレキシブルコンフォータブルLEDフォイルを製造するための優れた製造プロセスです。
これはまた、注目すべき興味深い分野だと思います。今回ご紹介したのは、オランダのホルスト・センターによるものです。
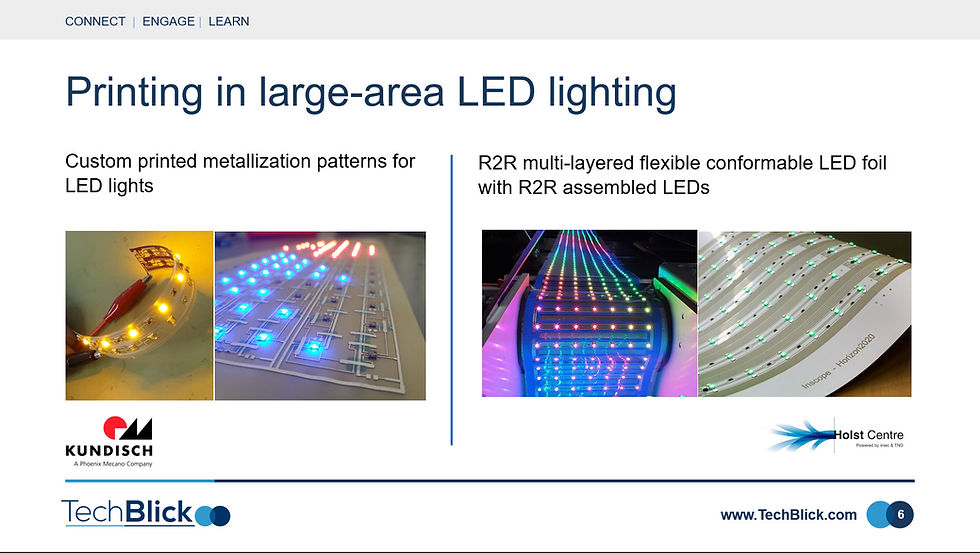
マイクロLEDディスプレイにおけるプリンテッドエレクトロニクス
しかし、LEDの話題の一方で、ディスプレイ業界のホットトレンドの1つは、もちろんマイクロLEDだと思います。
マイクロLEDは素晴らしいものですが、製造が難しいのです。右側にあるように、マイクロLEDにはさまざまな形があり、小型のディスプレイから超大型のディスプレイまで、さまざまな種類のディスプレイに使用することができます。また、インクの転写方法、LEDへの転写方法など、さまざまな方法があります。
その中で、意外と軽視されがちなのが、実際の基板をどのようにメタライズするかという点です。LEDを作成したら、それをマザー基板に配置または転写し、基板にメタライズする必要がありますが、これはPVDで行うことができます。そして、基板の表側(通常はガラス)と裏側の間にビアを作り、そのビアを充填することで、接続しなければなりません。
しかし、現在では、このメタライゼーションと、表側から裏側への接続をスクリーン印刷で行うことを提案している企業があります。
これはアプライドマテリアルズの例です。これは、アプライド マテリアルズのイタリアグループによるものです。表面と裏面をつなぐガラスの縁をぐるりと囲むように電極を印刷し、線幅と間隔の比率を約60~40マイクロメートルで実現しているのがわかります。
この利点は、ビアが不要であることと、アディティブ・プリンティングであることです。これは、工学的な問題でありながら、転写の問題ほどには注目されていません。ですから、あまり注目されていませんが、同じくらい重要な問題なのです。プリント印刷は、ここで興味深い役割を果たすことができると思います。
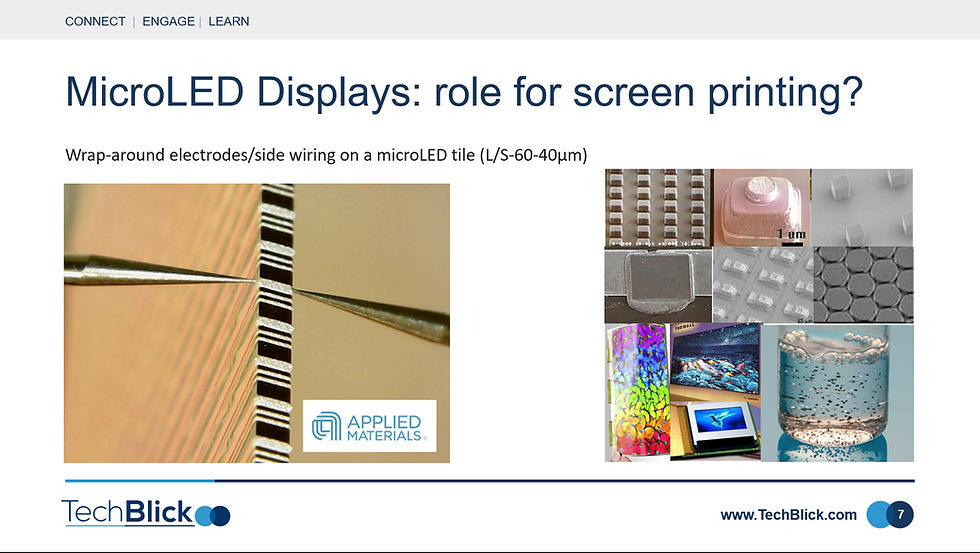
マイクロLEDにおけるトランスファーへの挑戦
しかし、当然ながら、マイクロLEDを作るとなると、転送が大きな大きな問題となります。
左側は、マイクロLEDが非常に小さいことがわかると思います。このグラフは、例えば、マイクロLEDと比較して実際には比較的大きい髪の毛や、埃やウィルスとの大きさの比較を示しています。X軸は対数であることに注意してください。
右側のグラフは、異なる解像度で一定の歩留まりを実現した場合の、故障したダイの数を示しています。
基本的に、不良ダイをほとんど出さないためには、プロセスの歩留まりは非常に高くなければなりません。もちろん、メタライゼーション、転写、ボンディングなど、プロセス全体の歩留まりを考慮すると、これは非常に困難なことです。
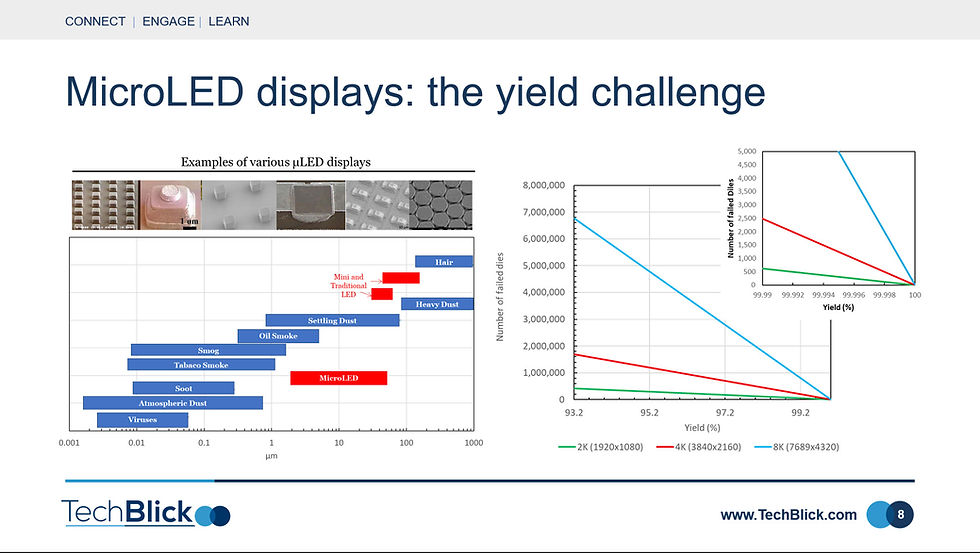
ディスプレイ修理におけるデジタル印刷
だから、修理の必要性があるのです。そして、再びプリンテッドエレクトロニクスが提供する機会のひとつが、3D表面への精密デジタルプリントです。
ここで、ポーランドにある非常に興味深い会社を紹介したいと思います。この会社は、粘性のある銀のナノ粒子を用いて、非常に細い線を描くことができるデジタルプリンターを持っています。
左上には、例えば3.2ミクロンの線を、わずか0.7ミクロンの間隔で印刷した例があります。
左下には、この技術を応用して、高解像度ディスプレイのオープン欠陥修復を可能にした例があります。
もちろん、マイクロLEDだけでなく、他の種類のディスプレイにも応用できます。これは、印刷プロセスの解像度が飛躍的に向上していることを示すもので、非常に興味深いものです。
右の図は、インクジェットやエアロゾルなど、他のアディティブプロセスに対するこのプロセスのベンチマークを示したものです。興味深いのは、このプロセスでは、非常に優れたフィーチャーサイズ、非常に小さなフィーチャーサイズを達成することができ、さらにインクの粘性も高いということです。
このプロセスは、高解像度ディスプレイの欠陥修復だけでなく、セキュリティや再分配層の試作、電子パッケージなど、さまざまな用途に応用できる可能性があります。
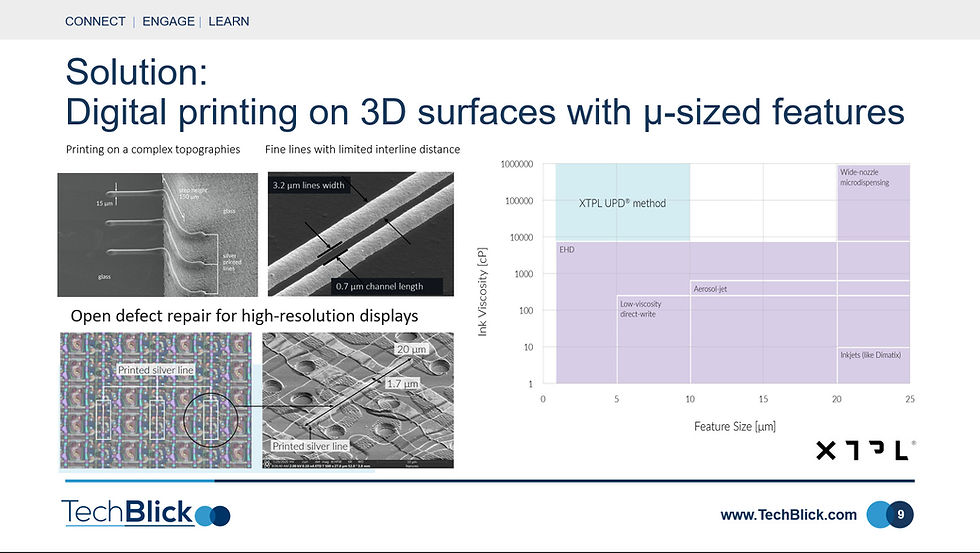
高解像度・高速R2Rプリント
しかし、解像度の向上はデジタル印刷に限ったことではなく、ロールtoロール印刷でもプリンテッドエレクトロニクスの黎明期には考えられなかった解像度を実現していることをここで強調したいと思います。
私がこの分野に入った10年ほど前、R2R印刷で線幅18マイクロメートルという最先端の解像度を達成している会社に初めて会ったのを覚えています。
これはコダックの例ですが、ロールtoロールフレキソ印刷で、線幅5ミクロンの解像度を達成しながら、1分間に100メートルという高速でプロセスを実行できることを示しています。
これは非常に興味深いことです。そしてもちろん、右下にあるように、マスターテンプレートを形成する方法にも革新性があります。このポイントは、ドットの上部が平らになるように製造されていることです。

透過型アンテナ
そのひとつが、透明なアンテナです。実は、これは完全にダイレクトなアディティブ・プリンティングのアプローチではありません。ハイブリッドなアプローチなのです。左下にあるのがその例です。フレキソ印刷とR2R印刷でインクパターニングを行い、さらにロールtoロール電気めっきでメタライズしているため、ハイブリッドになっています。
右下の表を見ていただくと、非常に興味深いパラメータがあるのがわかると思います。7〜8マイクロメートルの線幅で、シート抵抗は1平方メートルあたりわずか6Ω、透明度は約90.5%と非常に高く、550ナノメートルで緑色になります。
このアンテナは、GPSやLTE、Wi-Fiなど、さまざまな要件に合わせて設計をカスタマイズすることができます。
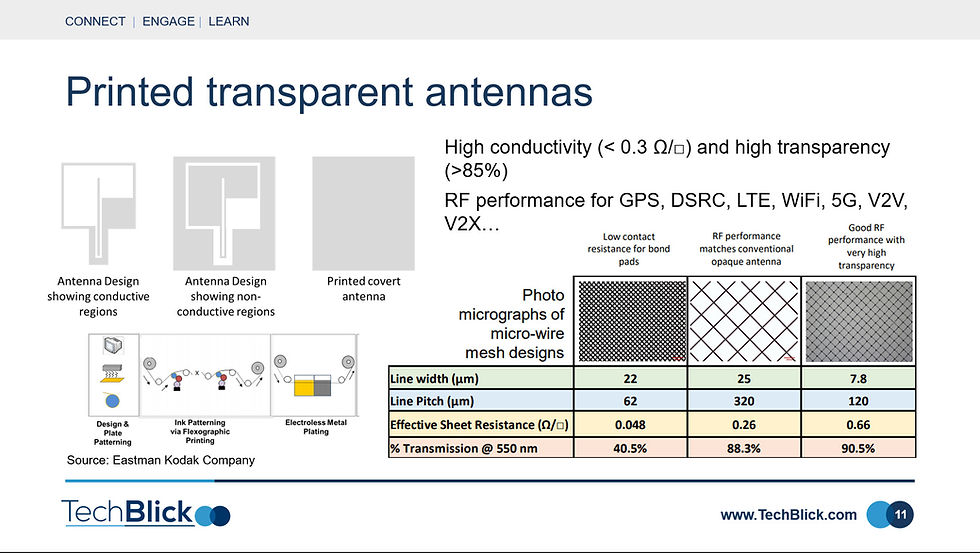
スキンパッチ、メディカエレクトロニクス
プリンテッドフレキシブルエレクトロニクスのホットな分野は医療用電極であり、多くのアプリケーションが存在する。
開発の最前線は、継続的な健康管理のための電子皮膚パッチの使用です。もちろん、標準的なグルコースサンプリングから連続グルコースサンプリングへ、さらにあらゆる種類の連続心拍モニタリングへと移行している現在、この分野は非常にホットになってきており、現在数十億ドルのビジネスとなっています。
この分野では、印刷が大きな役割を果たすことができます。ここで紹介したいのは、ホルスト・センターが開発したソリューションです。これは、臨床グレードの使い捨てパッチで、再利用可能な電子機器、乾燥電極などを備えています。ドライ電極には、印刷されたメタライゼーションが施されています。これにより、心電図、呼吸、体温を測定することができます。そして、7日間の連続モニタリングに有効です。つまり、接着剤からプリントライン、リジッドエレクトロニクスなど、フルソリューションが揃っているのです。そして、私はこう思います。プリンテッドエレクトロニクスで何が可能かを示しています。
右側の例は、別の会社、Screentec Oyのものです。右上の紫色の赤い絵は、医療用電極で、上部に表面金属デバイスを集積しています。右下の写真は、骨格筋の活動を検出するスクリーン印刷されたセンサーの例です。このように、あらゆる種類の電極を印刷することができます。

e-textile用ストレッチャブル導電性インク
スキンパッチの話題の一方で、エレクトロニックテキスタイルについても多くの議論がなされています。電子テキスタイルとプリンテッドエレクトロニクスが重なる部分として、インターコネクトやストレッチセンサーの印刷があります。
初期の頃、おそらく4〜5年前に、企業は第一世代の導電性伸縮インクを発表し始めました。
そして、ここ2年ほどで起こったことは、各社が単に伸縮性のある導電性インクを提供するだけでなく、電子テキスタイルの作成に必要な伸縮性インクの全ポートフォリオを提供するようになったということです。これには、銀インクはもちろん、カーボンインク、誘電体インク、導電性接着剤も含まれます。
ここでは、長瀬産業の例をご紹介します。銀のインクを100%伸ばせることがおわかりいただけると思います。カーボンインクもありますし、非常に優れた接着剤もあります。
真ん中のチャートは接着剤の特性ですが、ヒステリシスをほとんど発生させずに30パーセントまで伸ばすことができます。また、180℃で硬化させることができます。接着剤は、フルシステムの中で非常に重要な役割を担っていると思います。
右下のグラフは、銀線だけを印刷した場合、銀、カーボン、誘電体からなるスタックを印刷した場合よりも抵抗率が低くなることを示しているからです。銀、カーボン、誘電体からなるスタックを印刷した場合、抵抗率は低くなりますが、スタックを印刷することで、より洗浄しやすくなります。この場合、100回の洗浄サイクルを経験した後、材料や材料のスタックはより良い性能を発揮していることがわかります。全体の抵抗値の変化も小さくなっています。

医療用電子機器 R2R 量産型スクリーン印刷
電極の話に戻りますが、ここで強調したいのは、電極はかなり大きなビジネスであるということです。これはデンマークのMekprint社の例です。
右側にあるのは、ECG電極をロールtoロールで印刷した例です。このアプリケーションは、年間1億個以上の販売実績があります。
そして、左側の例は失禁センサーです。これもロールtoロールのスクリーン印刷です。なぜこれが面白いかというと、伸縮性のある不織布に導電性のケーブルラインをロールtoロールでプリントしているからです。また、これは商用アプリケーションですが、プリントセンサーは、リジッドエレクトロニクスや通信など、フルソリューションの一部であることがわかります。
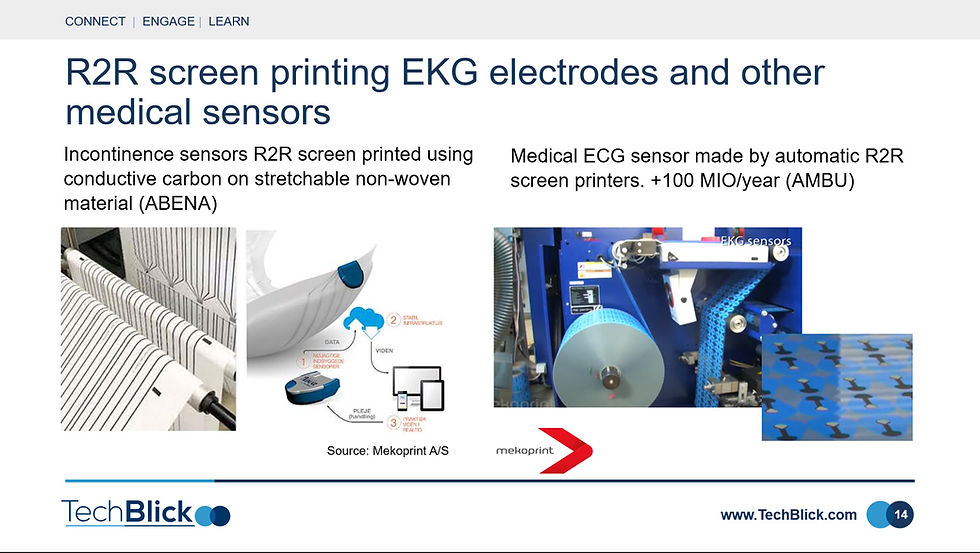
R2Rプリントディスプレイ
そこで、輪転印刷の話をするときに、このエレクトロクロミックディスプレイの例だけを取り上げたいと思います。
エレクトロクロミックディスプレイは、実はかなり以前から存在しており、初期の頃は手作業で生産していたため、非常に時間がかかっていました。しかし、今はYnvisibleという会社が、その工程をロールtoロールにしています。
ここにロールtoロールの機械の例がありますが、すべての工程がロールtoロールになっています。印刷、変換、テストなど、すべての工程がRoll to Rollマシンの中で行われます。
もちろん、これはコスト削減や大量生産への対応に役立ちます。
また、数ヶ月前に発表したばかりのアプリケーションですが、真ん中の写真は、バリューチェーンを通過するひき肉の状態を継続的にモニターするために、エレクトロクロミックディスプレイをパッケージに取り付けたものです。
Ynvisibleは、研究開発、設計段階からパイロット生産、量産に至るまで、ワンストップでお客様をサポートすることができるようになったのです。

プリンテッド二次電池の革新
そこで、エレクトロクロミックディスプレイの話をしているうちに、プリント電池で進行中のこれに行き着いたわけです。なぜこれを選んだかというと、右下の例を見ていただきたいからです。
この例では、左側にNFCチャージャーがあります。上側にはエレクトロクロミックディスプレイがあり、真ん中には印刷された二次電池があります。
数秒で充電が完了し、エレクトロクロミック・ディスプレイの駆動に使用することができます。ユニークで耐久性のある高分子固体電池ということで、非常に興味深い技術革新だと思います。
供給元はEvonik社
スラリー印刷は、お客様のデザイン・形状に合わせ、製造工程の一部としてスクリーン印刷することができます。有害物質もなく、二次電池にもなります。ですから、私たちの業界における重要なペインポイントを解決していると思います。
もちろん、プリント電池が登場しても、業界ではコイン電池を使用してきたことは周知の事実です(もちろん、非常に優れた例外もありますが)。プリント電池は商品化されていますし、商品化されています)。
これは、業界にとって実に興味深い展開だと思います。

フルラインR2Rプロセスインターフェイス
デジタルとアナログの両プロセスを統合した、フルインラインの統合型ロールtoロールシステムの例をお見せしたいと思います。これはCoatema社のもので、巻き出し機から乾燥機、レーザーパターニング、ロータリースクリーンプリンター、インクジェット、インライン検査、冷却まで、すべてを1台のマシンに集約している点が非常に興味深いです。
このように、ほとんどロールtoロールのファウンドリシステムが1つの箱に収まっているのがおわかりいただけると思います。
右側には、各工程で使用される機械のさまざまな要素の例を示しています。
Coatemaは、この分野で何年も経験を積んできた素晴らしい会社です。そして、その機械でインクやコンセプトのプロトタイプやテストをすることができます。そして、彼らはこの分野で深く長い経験を持っている必要があります。
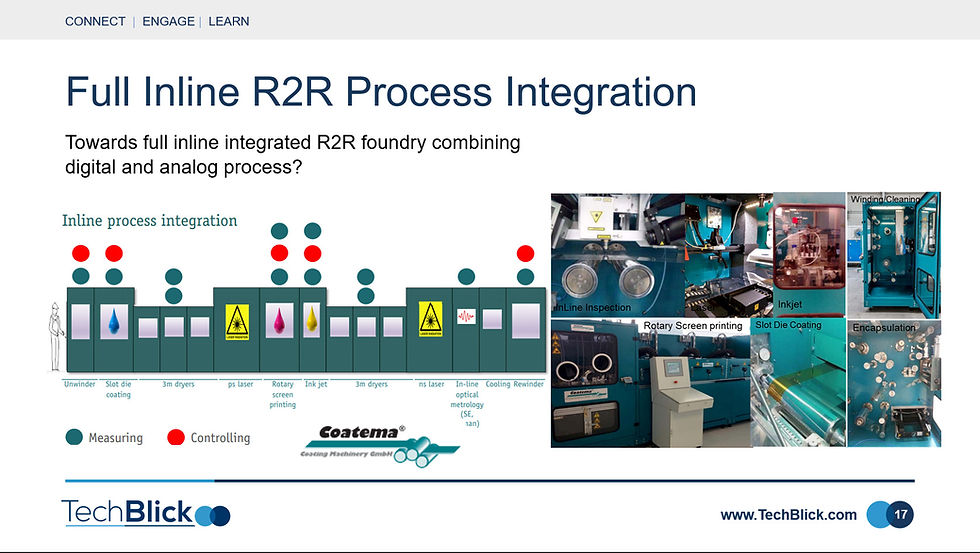
有機薄膜太陽電池とペロブスカイト薄膜太陽電池
冒頭で、プリンテッドエレクトロニクスと太陽光発電は、もちろん非常に密接な関係にあると申し上げました。プリンテッドバスバーが太陽電池に使われているのはご存じのとおりで、これはすでに大きな応用例です。
また、有機太陽電池の印刷も何年も前から試みられています。そして、Konarkaがいた頃がピーク、ハネムーンでした。
アメリカのKonarkaを覚えている人もいると思いますが、彼らは1億ドル以上の資金を調達しました。しかし、結局は失敗しました。彼らは業界を劇的に誇張しました。過剰な期待を抱かせたのです。Konarkaの失敗の後、この業界は長い間、荒れ果てた状態に陥りました。迷走していたんです。
ペロブスカイト型太陽電池は、非常に速いスピードで効率が向上していたため、ペロブスカイト型太陽電池への注目も失われてしまいました。
しかし、OPVは再び注目されるようになったと思います。OPVは再び注目され、突然、急速な効率向上を示しています。
この図は、カナダのブリリアント・マテリアル社から提供されたもので、OPVの効率をさらに向上させるために開発されている材料が示されています。
また、アクセプターがフラーレン系から非フラーレン系にシフトしており、この流れが加速しています。
また、製造のノウハウも蓄積されてきています。また、アクセプターとドナーの混合物を基板上に印刷する際、その形態をより正確に制御できるようになりました。
また、非常に興味深いのは、右側の例です。これは、コダックから生まれたと思われるEMSの製品です。
この会社は、ペロブスカイトのロールtoロール生産の規模を拡大しようとしています。100マイクロメートルのフレキシブルなガラスにプリントしています。
真ん中の写真は、100マイクロメートルのフレキシブルなガラスに金属メッシュをプリントしているところです。この例では、最高で毎秒60メートルの速度で走らせることができました。しかし、もちろん、全体のプロセスはもう少し遅いです。
右側にあるように、彼らはパイロットの役割からパイロットダウン、そして超大型の機械へと進んでいます。
そして、ここでのアイデアは、1.5メートルのウェブで、毎秒30メートルのウェブ速度を目標にやりたいと考えていることです。すべてがうまくいけば、これはフレキシブルガラスの大きなアプリケーションになるかもしれませんね。R2R印刷の大きな成功例で、4GWのロール印刷やコーティングされたペロブスカイト工場を作る。
もちろん、開発すべきことはたくさんあります。しかし、それにもかかわらず、これは、これらの企業がどのような意図で、どこまで来たかを示しています。

3Dプリンテッドエレクトロニクス。3D表面にインテリジェンスをもたらす
では、次に3Dプリンターで作られた電子機器について少しお話ししましょう。こちらも非常に興味深い分野です。大まかに言って、2つの方向に分けられると思います。1つは、すでに3D形状になっている基板をメタライズすることです。
上の段は、その例です。これは、3D形状の基板にアンテナをメタライズしたものです。また、自動車やヒーター、医療機器などにも応用されています。このほかにも、さまざまな用途があります。もちろん、アンテナの印刷は最も大きなものでした。しかし、これからはもっと増えていくと思います。
下の段は、3Dプリンテッドエレクトロニクスの例です。プリンテッドエレクトロニクスを従来の3Dプリンティングと組み合わせて、非常に複雑な形状の3Dプリントオブジェクトの内側と外側に回路や表面実装デバイスを作成することが可能になっています。
ここでは、部品が一種のデバイスに統合されている例や、卵の形に統合されている例を見ることができます。
3Dプリントにインテリジェンスをもたらすことができるのです。つまり、単に機械的なものを作るのではなく、3Dプリントされたオブジェクトの中にエレクトロニクスを組み込むことができるのです。設計から製造までシームレスに行うことができれば、多くの素晴らしい可能性が開けます。
その好例が、ドイツのニュルンベルクにあるNeotech AMTという会社で、この分野で最高のマシンをいくつか持っています。

あらゆる基板にプリントできる
もちろん、プリント基板はエッチングされたもので、印刷されたものではありません。しかし、4、5年前に始まったトレンドのひとつに、実際にプリント基板を印刷するものがあります。
その一例が、カナダのVolterraという会社です。この会社は、導電ラインを印刷できるデスクトッププリンターを持っています。ゲルバファイルを機械に供給すると、メタライゼーション・ラインをプリントしてくれます。ビアを作り、はんだや導電性接着剤を塗布し、リフロー処理も可能です。
これはデスクトップ型のオールインワン・ターンキー・ソリューションで、新しい研究センターや、さまざまな種類の回路を設計して試しているグループなどのプロトタイピングに多くの応用があります。また、もちろん、大学向けにも。

インモールド・エレクトロニクス 離陸
IMEもまた、成熟し始めたトレンドとして注目されるべきものです。これは始まっては止まり、始まっては止まりの繰り返しで、何年も前の大きな話題は、フォードがインモールド・エレクトロニクスを使って作ったオーバーヘッドコンソールを受け入れたものの、欠陥があったためリコールを余儀なくされたことだったと思う。
しかし、その裏では開発が続けられていたのです。そして数年前、ウェアラブルやコンシューマーデバイスへの小型のアプリケーションが登場しました。
さらに、自動車用LEDライトのカバーガラスにヒーターを埋め込み、霜取りを促進させるという用途も出てきました。
そして今、インモールド・エレクトロニクスを使った自動車の内装への応用が間もなく期待できるところまで来ていると思います。
このプロセスは、材料全体の開発から、非常に複雑なプロセスの開発まで、長い道のりを歩んできました。必要なすべての層を印刷し、改質し、硬化させるという、業界にとって非常に急な学習曲線でした。
かなり複雑なプロセスです。しかし、現在では、業界には蓄積された経験があります。複雑なデザイン、照明の統合、小型電子機器へのさまざまな機能の統合に対応できるようになりました。
ですから、この流れは本当に加速していると思います。しかし、3D形状やストレッチ、機能性レイヤーの応用は、電子機器に限ったことではないことを示したいと思います。その好例が、木本製作所の製品です。
木本は、3つの成形可能な拡散膜を作りました。右側にあるのがその例です。右下にあるように、このフィルムは200%まで伸ばして好きな形にすることができます。
これは光拡散フィルムで、用途は右上に示したとおりです。ですから、LEDの光が目立たない代わりに、照明が続いているように見えるのです。ですから、このような3次元成形可能な拡散フィルムを貼ることで、優れた配光を実現することができるのです。
また、熱を逃がす効果もあるので、ホットスポットを隠すこともできます。
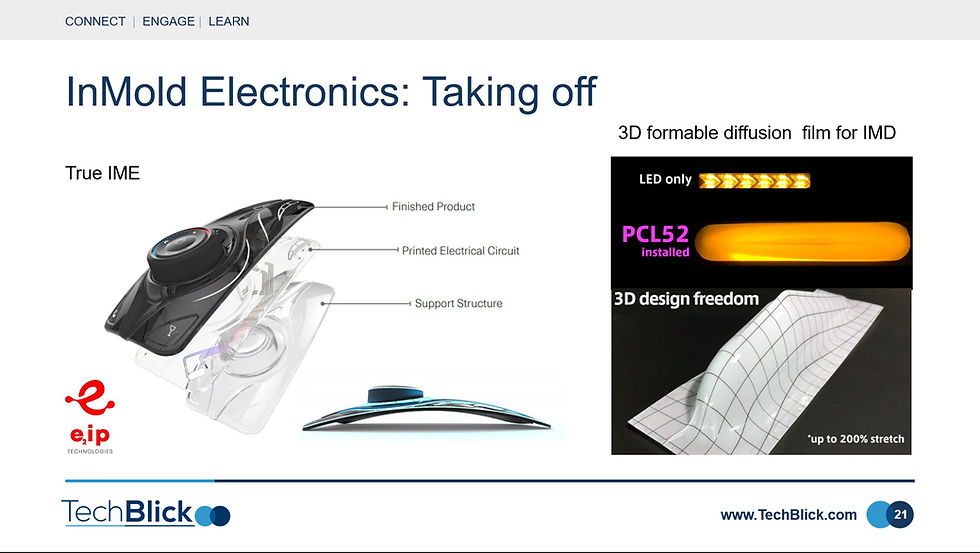
自動車用プリント透明ヒーター
透明ヒーターを印刷するための優れたソリューションはそれほど多くありませんし、新たに登場したソリューションの多くが印刷を伴うものだからです。
その1つが、基板に非常に細かい溝を埋め込み、シード層を印刷し、電鋳することで、基板に非常に細かいが深い銅線を埋め込み、高い導電性を実現し、非常に細かい金属メッシュで広い面積をカバーする方法です。つまり、非常に低い接続性と高い透明性を両立させることができるのです。
もう一つのアプローチは、マサチューセッツ州にあるChasm社によるもので、銀ナノワイヤーとカーボンナノチューブを組み合わせた独自の材料をスクリーン印刷することができます。
これをフィルムにスクリーン印刷すると、下の写真にあるように、摂氏120度以上のヒーターを作ることができます。
右側には、このフィルムを自動車のフロントヘッドに貼った例があります。温度プロファイルが実際に上がっているのがお分かりいただけると思います。
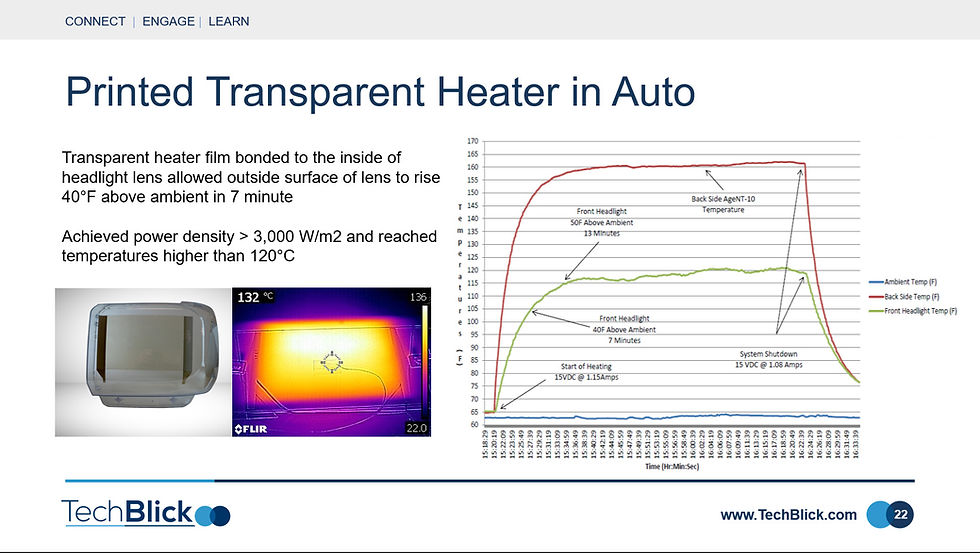
銅インキ:課題は克服されたのか?
もちろん、プリンテッドエレクトロニクスと導電性インクの話は絡み合っている。そして、長年にわたり、高価な銀に代わる銅の指輪を作ろうとする人々がいましたが、それほど成功しませんでした。
そこには2つの大きな問題があった。そのひとつは、酸化させずに硬化させること。そのため、特殊な設備や特殊な条件が必要となり、しばしば費用や設備の追加が発生し、また、銅は代用品としては使えないということになりました。
また、もう一つの問題は、銅のインクが十分に導電性を持っていなかったことです。そのため、厚い層を印刷することになり、コスト面でのメリットがなくなってしまうのです。
現在では、非常に有望と思われる銅が市場に出てきています。その一例が、イスラエルのCopprint社によるものです。
彼らのベンチマークはこちらでご覧いただけます。これは同社が独自に行ったベンチマークです。この例では、銅の導電性と焼成時間を、さまざまなナノ粒子や他の種類のインクと比較した結果を見ることができます。これは、印刷して乾燥させた後、非常に高速に焼結して非常に高い導電性を達成するプロセスです。
焼結は通常200℃以上の高温で行われます。しかし、160℃で焼結できるプロセスもあり、例えば熱安定化PETと互換性があります。
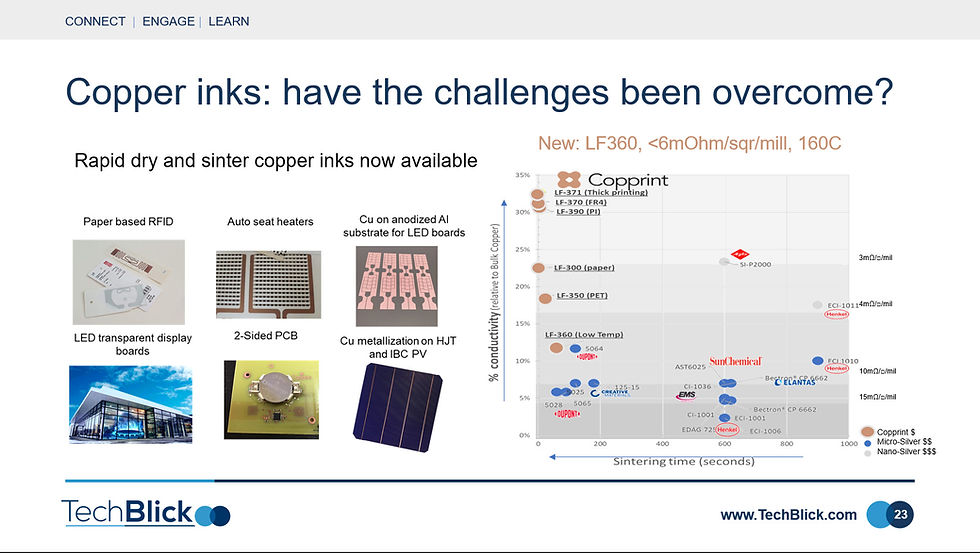
Agナノ粒子インク: 低い硬化温度でより高いパフォーマンス
開発の進展は、銅だけでなく、銀のナノ粒子にも及んでいます。
銀ナノ粒子は新しい技術ではありません。銀ナノ粒子は新しい技術ではなく、10年以上前から存在しています。銀ナノ粒子は新しい技術ではなく、10年以上前からある技術です。
AGFAは、クラリアント社の銀ナノ粒子事業を最近買収しました。AGFAでは、有機インクと水性銀ナノ粒子インクの両方をポートフォリオに持つことになりました。
これらの例から、所定の硬化温度において、導電性が劇的に向上していることが分かります。特に、硬化温度が110℃の場合、最新世代のインクがはるかに優れた導電性を達成していることがわかります。
これは、銀ナノ粒子を低温処理に向かわせるという意味で、重要な開発です。これは重要な開発で、銀ナノ粒子を低温処理に向かわせるもので、使用できる基板の幅が広がります。長い間、アニール温度の制約があり、基板がその温度に対応できない場合、十分な導電性が得られないという問題がありました。そこで、これらの開発では、この問題を解決しようとしているのです。

HMIも立ち止まらない
プリンテッドエレクトロニクスは、長い間、何十年もの間、メンブレンスイッチやヒューマンマシンインターフェイス、静電容量式スイッチの分野でした。このような分野でも、業界は停滞しているわけではなく、実にうまく進歩していることを、ここで簡単に強調したいと思います。
ここでは3つの例をご紹介します。左は、USBを内蔵したメンブレンスイッチキーボードをカスタマイズしたものです。中央は静電容量方式のキーボードで、コントローラが内蔵されています。右はタイトセンサーとディスプレイドライバが統合されたものです。
基本的に、ここでのメッセージは、アトマイズメモリースイッチや静電容量式スイッチを作っている会社は、より高い価値と複雑なステップを印刷プロセスに統合しようとしている、あるいはメンブレンスイッチにUSBシステムを統合している、などということです
メンブレンスイッチ自体が、これまでのようにコモディティ化の進んだビジネスになっていく中で、より高付加価値なものへと移行していこうということです。
[This is automatically translated from English]
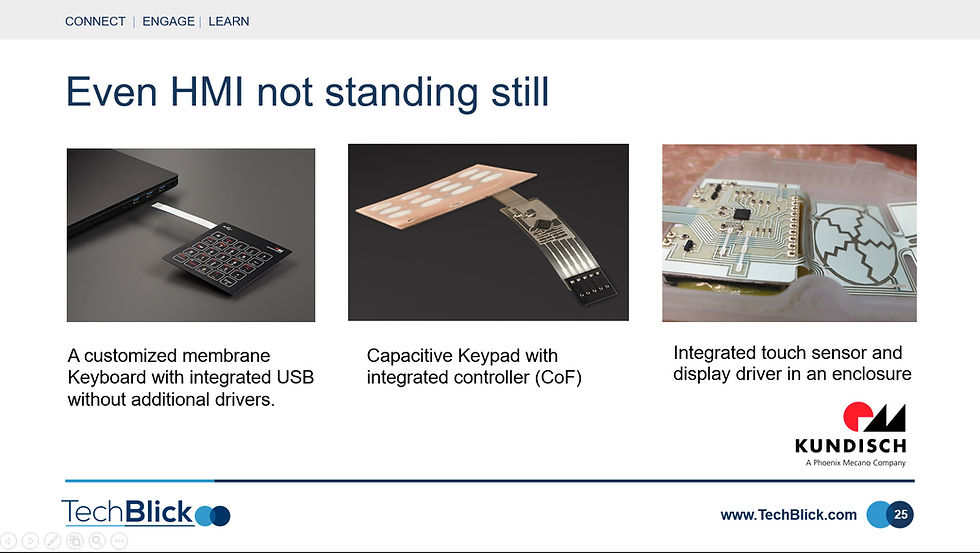