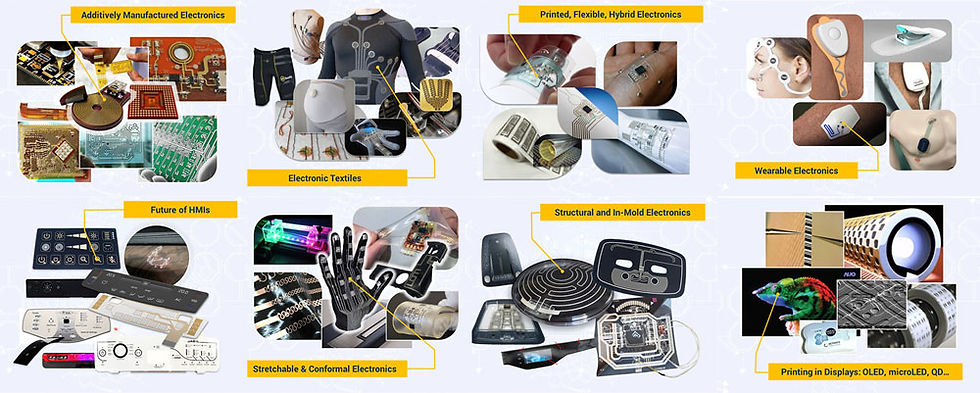
このニュースレターでは、材料、プロセス、アプリケーションの広範な領域をカバーするアディティブエレクトロニクスに関する最新情報を定期的にお届けします。アディティブエレクトロニクスという言葉は、極めて多様な技術やアプリケーションを包含しています。私たちはそのすべてをカバーするつもりです。詳しくは、TechBlickのオンラインまたはオンサイトでご覧ください。 (www.TechBlick.com).
マイクロLED用ラップアラウンド電極
マイクロLEDディスプレイを大面積化するために、小型のディスプレイにはタイトルを付けることができます。マイクロLEDはエッジのないデバイスなので、タイリングが機能し、見た目がすっきりする。
各タイトルには、マイクロLED、バックプレーン、ドライバー電極を配置する。ガラス基板の表側にはマイクロLEDとバックプレーン、裏側にはドライバー電極を配置します。この2つをつなぐのがインターコネクトです。ラップアラウンド電極(端に巻きつけて表と裏をつなぐ配線)は、ドリルで穴を開けてガラスを貫通させる必要がない、エレガントなソリューションです。
ラップアラウンド電極は、印刷またはPVD成膜が可能です(いずれも面取りガラスが望ましい)。後者は、より良いフィーチャーサイズと薄く導電性のあるラインを得ることができ、一方、前者は生産性を向上させることができます。
以下の画像は、様々な技術のデモンストレーションです。スクリーン印刷は、TACT時間が短く、堅牢なソリューションです。アプライド マテリアルズは、非常に狭い線幅(30μm)を狭いスペーシング(50μm)でスクリーン印刷できることを実証しています。これは素晴らしい結果です。ちなみに、シリコン太陽電池への導電性ペーストのスクリーン印刷の最先端/生産は、それぞれ35umと20umであることに注意してください。この工程では、まず上下の電極を印刷した後、基板を回転させて(アライメントに優れている)端から電極を印刷する。

この技術には優れた装置が必要である。アプライドマテリアルズは、230x230mmの基板に対応し、±6umの再現性と1000pphのスループットを実現する装置を発表した。なお、過去と印刷プロセスの最適化が重要である。一般に、ガラスへの密着性が5Bで非常に高い導電性(バルクAg20%)のペーストが必要になります。最終的な印刷厚みは3-5μmが目標である。スクリーン印刷は、エッジ付近にピークがなく、滑らかな表面であることが望ましい。
ラップアラウンド電極のアディティブデポジションには、エアロゾル噴射も提案されている。エアロゾルの利点は、3次元表面上に印刷できることと、一般にスクリーン印刷よりも微細な形状を成膜できることである。ラップアラウンド電極を実現するためには、ハーフラップ電極を2回印刷する必要がある(下図参照)。その間に、ガラスを回転させる必要がある。オプトメックでは、1時間あたり18kのフルラップインターコネクトを達成するとしています(ガラスを回転させる時間は除く)。なお、以下の例ではL/Sが50umですが、原理的にはエアロゾルの噴射は下方向から可能です。
一般的に、これはマイクロLED市場にとって興味深いソリューションです。
インパルスプリンティング-プリンテッドエレクトロニクスプロセスの最高峰?
I先日、TechBlickで発表されたmpulse Printingは、エキサイティングな技術であるようです。技術の詳細はまだ完全に開示されておらず、開発はまだ実験室の段階ですが、開示された結果と主張された性能レベルは驚くべきものです。
下の写真にあるように、この技術では、2μmから1mmまでの解像度でトラックをデジタルプリントすることができます。また、0.1〜10,000 Pa.sという非常に広い粘度範囲の材料をプリントできるため、銅や銀のインク、はんだ、エポキシ系(!)導電性接着剤もプリントできるのだそうです。また、3次元表面への印刷も可能で、1μmから10mmまでの隙間への印刷が可能です。このデジタル印刷技術は、連続したパターンだけでなく、同時のパターンも高速で印刷することができます。
解像度、印刷ギャップ、インクやペーストの粘度など、あらゆるパラメータが多様であることは、デジタル印刷プロセスとしては非常にユニークです。実際、下の図に示すように、各技術は解像度/フィーチャーサイズ、粘度、プリントギャップなどの点で一定の位置を占めている。)
この技術はまだ歴史が浅く、発展途上である。現在、印刷面積は1x10mm2と小さいですが、20x20mm2、96x96mm2と印刷できるように拡張するロードマップがあります。
この技術は、まもなくスタートアップ企業としてスピンアウトする予定ですので、ご期待ください。
プリンテッドエレクトロニクスの精度を1um以下に
プリンテッドエレクトロニクス技術が進化している。その方向性は超微細線印刷であり、フォトリソグラフィーの領域にまで踏み込むことが可能になってきています。今回ご紹介するのは、VTTが開発したサブミクロン印刷のプロセスです。
プロセスは、リバースオフセット印刷です。まず、PDMSローラーにインクを塗布します。インクはローラー上で半乾燥し、一部はPDMSに吸収される。この半乾燥状態により、インクが液体である場合の濡れに関する問題を克服することができる。インクを塗布したPDMSローラーをCliche(凸版)に接触させ、インクの一部を除去する。PDMSローラー上でパターン化された半乾燥インクは、最終的な基板に転写されます。
この例では、VTTが銀ナノ粒子インクの1µmダイレクトプリントを実現しています。デスクトップ型ROプリンターを用いて、PET上に金属メッシュを1µmの線幅で印刷しました。報告されたシート抵抗はあまり低くなく(100Ω/sqr)、おそらく線が非常に細いためと思われます。
一般に、ROPは最小解像度0.5-5µm、印刷厚み線幅20-1000nm、重ね合わせ精度<2um、印刷速度50mm/s(3m/min)を可能にすることに留意されたい。

柔軟なハイブリッドソリューションのための先進のインターコネクトソリューション
フレキシブル・ハイブリッド・エレクトロニクス(FHE)は、印刷されたフレキシブルなエレクトロニクスとリジッドなSiベースのエレクトロニクスの長所を融合させたものです。印刷物(広幅)とSi IC(狭ピッチ)間の配線は、重要かつしばしば制限されるボトルネックとなっています。TPU(ストレッチャブルエレクトロニクス)やPET(フレキシブル電極)などの基板は、ビスマスベースの低温ハンダよりも厳しい温度制限があり、また、一部のインク(特にAgインク)はハンダに溶けるため、通常のハンダは簡単に使用することができません。さらに、これらの配線は、ICのピッチサイズに対応するだけでなく、屈曲や伸縮に耐え、業界の標準的なプロセスに適合する必要があります。
一つの選択肢として、粒子を充填した(多くの場合Ag粒子)エポキシ樹脂で相互接続を形成する方法があります。この場合、異方性でない限り、ピッチサイズに制限があります。さらに、高い導電性を得るためには、粒子の充填量が多くなり、コストアップにつながる。
サンレイサイエンティフィック社は、2液性エポキシ系に強磁性粒子を分散させるという新しい解決策を開発した。強磁性粒子は、外部磁場により垂直方向に配列し、z軸方向に導電路を形成する。この場合、ピッチは100μmまで可能である。硬化温度は80℃と低く、TPUやPETとの相性も良い。また、極端な繰り返し伸縮にも耐えることができる。
さらに、下図のように標準的なSMTプロセスとの互換性があります。この材料は、ステンシル印刷やディスペンス印刷が可能です。コンポーネントをピックアップして配置した後、磁気パレットを使用して粒子を整列させ、フィルムを硬化工程(バッチオーバー、リフロー、縦型オーブン)に送ります。
これは面白いプロセスですね。もちろん、ハンダのようなセルフアライメント機能はありません。また、現在のところ100μmが限界であり、多くのICには広すぎる。

はんだ付け可能な高導電性Cuナノ粒子インク?
プリンテッドエレクトロニクスでは、最も一般的なインク・ペースト材料であるAgペーストに直接はんだ付けを行うと、金属間化合物層が形成されないため、大きな課題となっている。Cuの場合、これは異なる可能性があります。
コプリントは、Cuペーストに直接はんだ付けができ、濡れ性が悪くても良好なせん断試験結果が得られることを実証している。また、例えばFR4基板に標準的なSAC305はんだを使用した場合、はんだ付け中に強い金属間化合物層が形成されることも示しています。
これは、プリンテッドエレクトロニクスを標準的なSMTプロセスとの互換性を高めるものであり、当技術分野の重要な進歩です。さらに、Cuインクは低温はんだにも対応しており、Cuラインを印刷したPET基板に直接部品をはんだ付けすることも可能です。
一般的に、Cuインクにはこれまで問題がありました。導電率が十分に高くないため、より多くの材料が必要となり、銀に比べて1Kgあたりのコストが高くなってしまうのだ。また、新しい焼結工程が必要で、新しい学習曲線と新しい装置が必要であった。Copprint社のデータは、同社のインクが非常に高速に焼結でき、従来の銀製品メーカーを凌駕する導電性レベルを達成できることを示唆している。 [This is automatically translated from English]
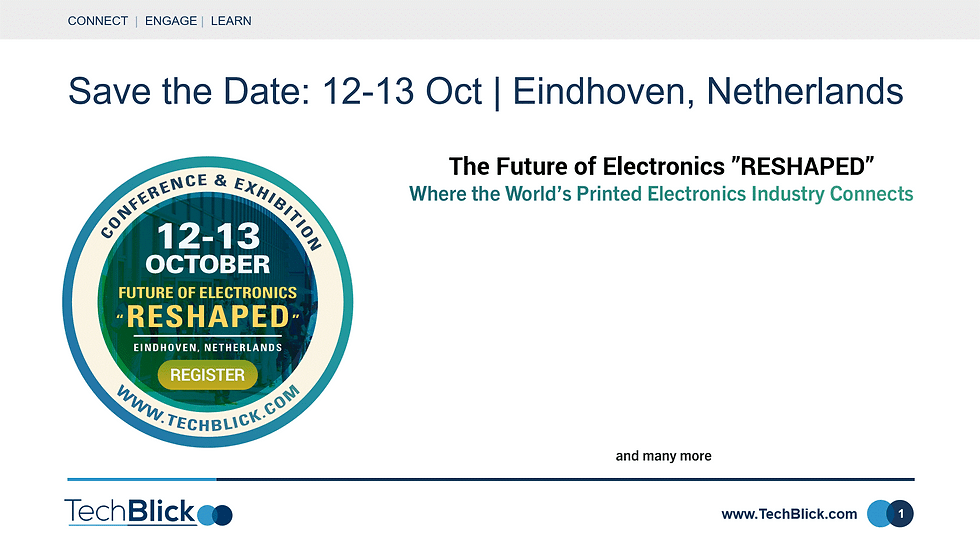