caractéristiques inférieures au micron
La technologie de l'électronique imprimée évolue. L'impression de lignes ultrafines est un axe de développement qui permet à la technologie d'empiéter de plus en plus sur le domaine de la photolithographie.
Dans cet article, nous abordons les technologies d'impression directe analogique et hybride, qui permettent à l'électronique imprimée d'atteindre des tailles de caractéristiques de quelques microns et inférieures au micron. Il s'agit d'une évolution importante qui rapproche l'électronique imprimée des applications électroniques. Dans un prochain article, nous aborderons les techniques d'impression numérique.
Cet article est basé sur des présentations et des discussions récentes lors d'événements TechBlick. TechBlick est la maison de l'industrie mondiale de l'électronique imprimée, offrant tout au long de l'année des conférences de classe mondiale en ligne et sur place, des cours de maître et des mises à jour sur l'industrie. Rejoignez TechBlick avec un abonnement annuel ou mensuel pour vous connecter à la communauté mondiale de l'électronique imprimée (www.TechBlick.com). Notre prochain événement sur l'électronique imprimée sera un festival des innovations en ligne qui aura lieu le 24 juin 2022.
Cet article commence par la sérigraphie, car elle est le moteur de l'industrie. À l'exception des écrans, la plupart des applications de l'électronique imprimée reposent sur cette technologie. Aujourd'hui, beaucoup d'entre elles impriment régulièrement des largeurs de ligne d'environ 50 µm en utilisant la sérigraphie. 50µm en production sur des substrats flexibles. Cependant, l'état de l'art pousse déjà en dessous de cette limite. Je présente ici deux exemples intéressants.

L'image de droite provient de Fraunhofer ISE (2019), montrant comment ils ont pu sérigraphier des lignes de 19µm de large sur des cellules solaires en silicium pour agir comme des doigts étroits. Il s'agit d'une avancée importante par rapport aux largeurs de ligne courantes de >30µm, réduisant la teneur en Ag par tranche et laissant plus de surface de tranche solaire ouverte au soleil. Il s'agit de facteurs essentiels pour optimiser le coût et les performances des cellules photovoltaïques en silicium.
Les images du milieu (ci-dessus), réalisées par Asada Mesh (2022), montrent des lignes imprimées sur du PET avec des largeurs de ligne aussi étroites que 22 µm. Il ne s'agit pas d'un exploit facile, qui nécessite l'optimisation du substrat, de la maille, de l'écran, de la pâte, etc. Les mailles ultra étroites en acier inoxydable constituent une technologie clé à cet égard. Ici, à droite, vous pouvez voir des fils à maille de 9µm, récemment annoncés par Asada Mesh, montrant comment la technologie des mailles évolue.
Ces deux exemples démontrent une fois de plus que la sérigraphie n'est pas au bout du chemin. On sous-estime cette technologie à ses risques et périls. Des améliorations progressives mais importantes permettront bientôt d'obtenir des largeurs de ligne S2S inférieures à 25 µm et inférieures à 20 µm sur des substrats PET et wafer/céramique. La limite exacte de la largeur de ligne n'est pas connue, mais on suppose, pour l'instant, qu'elle est d'environ 15 µm.
Pour surmonter les limites de la largeur de trait de la sérigraphie directe, des solutions hybrides sont proposées. Celles-ci impliquent généralement la sérigraphie d'une ligne modérément étroite suivie d'un marquage au laser ou autre. Je décris ici la solution développée par Toray.
L'approche est présentée schématiquement ci-dessous. Une pâte sérigraphique photogravable est développée, qui peut être directement structurée par photolithographie sans nécessiter une étape supplémentaire de dépôt et de développement de photorésist. La version de cette pâte compatible avec le PET à basse température permet un L/S aussi étroit que 10/10 µm. Cependant, la conductivité obtenue n'est pas la plus élevée (environ 30-80 uOhm.cm lors du durcissement à 140C). La version haute température va bien sûr plus loin dans la conductivité, approchant le x2bulk (3uOhm.cm) lors du frittage à 850C.
Cette solution est particulièrement adaptée aux électrodes de bord d'écran tactile à base d'ITO sur des substrats en PET car (a) elle permet d'obtenir des électrodes de bord étroites (L/S plus faible) et (b) le modelage du film d'ITO nécessite de toute façon une photolithographie.
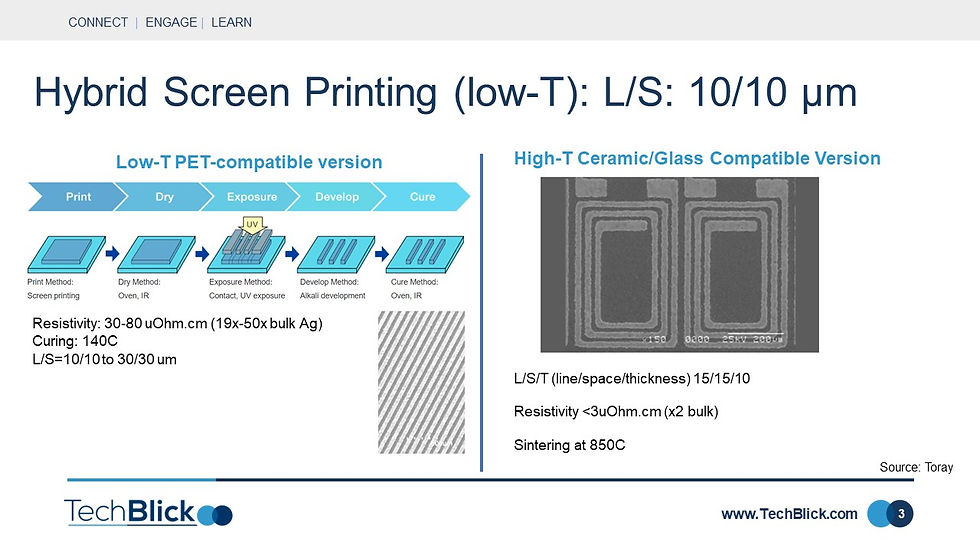
Cette approche peut être affinée pour prendre en charge des L/S encore plus étroites. Dans cet exemple, vous pouvez voir des exemples de câblage de circuits fins et de mailles métalliques, atteignant respectivement une largeur de ligne de 8 µm et 2,5 µm. Notez qu'avec une largeur de trait de 2,5 µm, ce procédé d'impression hybride s'approche des meilleures largeurs de trait de maille métallique de sa catégorie. Cette technologie présente néanmoins certaines limites, à savoir une température de polymérisation élevée de 230°C (qui n'est pas compatible avec le PET, le PEN et le PC) et une résistivité de pâte modérée.
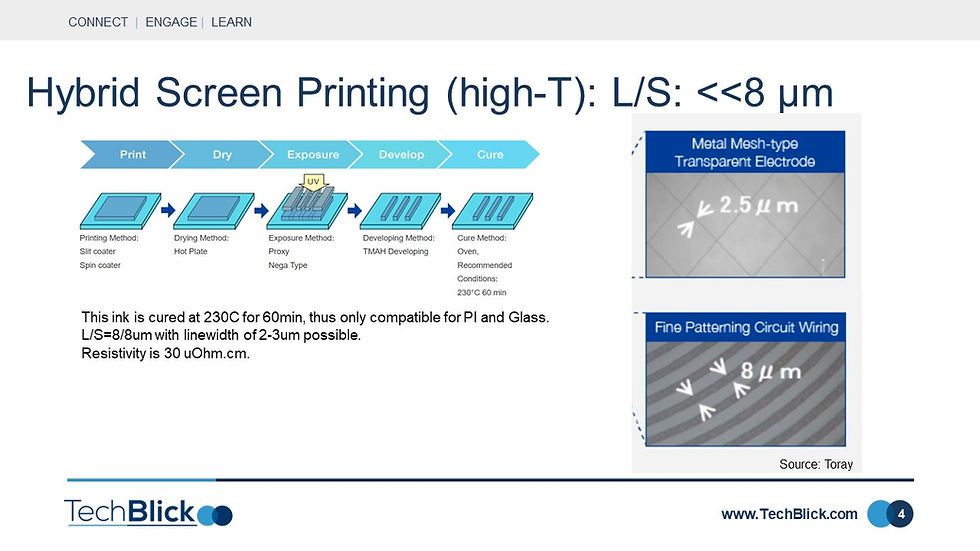
Il existe de nombreuses raisons pour lesquelles on peut vouloir imprimer en utilisant une technique autre que la trame, notamment des vitesses d'impression plus élevées, des tailles de traits plus fines et des épaisseurs d'impression plus faibles. Ces deux graphiques, élaborés par Eastman Kodak, offrent une carte perspicace. Le graphique de gauche montre que la flexographie, l'héliogravure et le jet d'encre sont mieux adaptés à la formation de lignes plus fines à l'aide d'encres à faible viscosité. Le graphique de droite montre que le jet d'encre, la flexographie et divers procédés d'impression par mico-nano-contact permettent d'obtenir des caractéristiques inférieures à 30 µm.
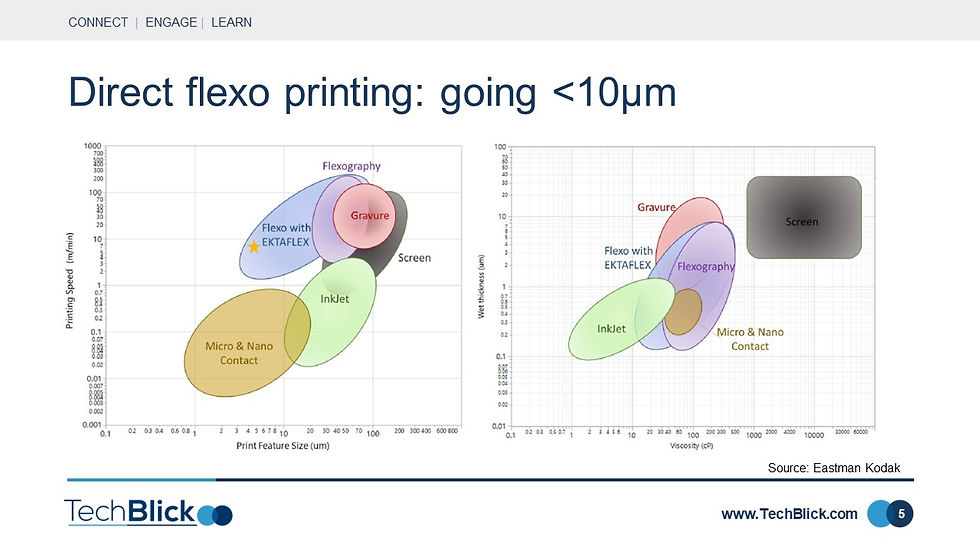
Kodak a encore fait progresser l'art de l'impression flexographique à grande vitesse de couches fonctionnelles. En particulier, ses plaques flexographiques à points supérieurs plats et à haute résolution (obtenues grâce à des lasers non Gaussiens bien conçus) permettent d'obtenir des caractéristiques plus fines. Ici, à gauche, on peut voir un exemple de plaque à points à sommet plat.
À droite, un exemple d'impression de lignes fines est présenté pour une application d'antenne RF. Ici, une fine couche catalytique est imprimée par flexographie, puis plaquée au cuivre pour obtenir une conductivité élevée du cuivre, nécessaire à la bonne performance de l'antenne. La largeur de la ligne imprimée peut être aussi étroite que 7,8 µm, ce qui démontre la capacité d'impression de lignes fines de ce procédé.

Vous trouverez ci-dessous un exemple de procédé d'héliogravure offset développé par Komura Tech au Japon, qui permet d'imprimer directement des lignes continues et ininterrompues avec une largeur de ligne inférieure à 5 um.
Notez qu'il s'agit d'un procédé "offset" et, comme nous le verrons, la plupart des techniques d'impression sub-5um impliquent une étape "offset". Ici, le rouleau hélio encré transfère d'abord la pâte sur un rôle vierge, qui la transfère ensuite sur le substrat. L'un des avantages de cette approche est que l'encre peut être partiellement séchée avant d'atteindre le substrat, ce qui évite les problèmes liés au mouillage qui limitent la largeur de la ligne.
Cette technologie permet une métallisation fine des circuits sur des substrats flexibles. Les lignes sont actuellement basées sur des NPs d'Ag et sont susceptibles d'être très fines (250-300nm).

Shashin Kagaku, au Japon, a démontré l'impression directe S2S de couches minces (250 nm) d'encres à base de nanoparticules d'argent avec des largeurs de ligne aussi étroites que 1,5 µm dans des motifs complexes. Le procédé peut être appliqué sur du verre et du PET (remarque : influence également la résistivité de la feuille obtenue en raison de la différence de température de durcissement autorisée).
Un marché cible évident est celui des TCFs à maille métallique et ici, ils peuvent démontrer une résistance de feuille de 0.2- 0.3 Ohm/sqr à 150C (gamme compatible avec le PET).

Voici un autre exemple d'impression "offset" mis au point par VTT (Finlande). Dans ce procédé d'offset inversé, le rouleau en PDMS est d'abord enduit d'encre. L'encre est semi-sèche sur le rouleau, en partie par absorption dans le PDMS. Cet état semi-séché permet de surmonter les problèmes liés au mouillage lorsque les encres sont à l'état liquide. Le rouleau PDMS encré est mis en contact avec un cliché, ou plaque en relief, ce qui élimine une partie des encres. Les encres semi-séchées sur le rouleau PDMS sont ensuite transférées sur le substrat final.
Dans cet exemple, VTT a réussi à imprimer directement des encres à nanoparticules d'argent de 1µm. L'imprimante RO de petite taille a été utilisée pour imprimer une maille métallique sur du PET avec une largeur de ligne de 1µm. La résistivité de la feuille rapportée n'est pas très faible (100Ohm/sqr), probablement parce que les lignes sont très fines.
Notez que le ROP peut permettre des résolutions minimales entre 0.5-5µm, des lignes d'épaisseur imprimées autour de 20-1000nm, une précision de superposition <2um, et des vitesses d'impression de 50mm/s (3m/min).
Dans tous les exemples démontrés jusqu'à présent, un conducteur imprimé (principalement de l'encre Ag NP) est imprimé. Cependant, ce procédé d'impression de lignes ultrafines peut également imprimer une résine photosensible, ce qui permet de remplacer la photolithographie dans certains cas.

Le dernier procédé d'impression directe de lignes ultrafines que je souhaite mettre en avant est celui d'Asahi Kasei. Ici, des lignes droites et formées ininterrompues de moins de 1 µm sont démontrées. Par exemple, sur l'image de droite, on peut voir des lignes continues de 300 nm de large, ainsi que des motifs TFT imprimés avec une résolution de 2000 ppi (pixels par pouce) [ici, le pas total des pixels TFT est de 12,5 um].
Le processus exact n'est pas divulgué, mais nous pensons qu'il s'agit d'un processus d'offset inverse R2R. Ici, comme dans le cas précédent, un système d'encrage applique l'encre sur un rouleau de blanchet. Un moule contenant le motif final est mis en contact avec le rouleau encreur, ce qui élimine une partie de l'encre pour former le motif. Enfin, le rouleau encreur transfère le motif sur le substrat final.
La formation du rouleau, qui permet essentiellement la nanoimpression R2R, constitue une étape technologique clé. Ici, aucun laser n'est déployé. Au lieu de cela, une lithographie par faisceau d'électrons (avec plusieurs lignes d'exposition) est utilisée pour créer des caractéristiques ultrafines. Dans le cas présent, le rouleau est d'abord revêtu par trempage, exposé à la lithographie par faisceau d'électrons, développé et endossé. La précision de ce processus est illustrée sur les photos du milieu, qui montrent des largeurs de ligne de 1 µm dans des pas de 5 µm. Actuellement, les rouleaux sont disponibles en 250 mm de largeur et 100 mm de diamètre ou plus petits. Nous pensons que la vitesse actuelle de la bande est de 1m/min ou moins.
Asahi Kasei vise la métallisation des fonds de panier TFT ainsi que les antennes RFID transparentes. Les RFID transparentes permettent d'imprimer des graphiques sur toutes les parties de l'emballage puisqu'elles ne bloquent aucune zone. Cette technique d'impression en ligne étroite peut également avoir des applications de sécurité.

Jusqu'à présent, nous avons couvert l'impression directe (à l'exception de la sérigraphie). De nombreuses solutions "hybrides" sont également développées pour permettre la réalisation de lignes ultrafines. Cet exemple est celui de Panasonic, bien que de nombreuses autres sociétés, comme O-Film, aient déjà développé des technologies similaires. Nous avons choisi l'exemple de Panasonic car il s'agit d'une solution techniquement sophistiquée, qui permet d'obtenir des traits de 2 µm sur les deux faces du film PET.
Dans cette approche, de fines rainures sont d'abord embossées dans le film. Les encres Ag NP sont ensuite utilisées pour remplir le sillon (probablement avec une racle). Cette approche présente quelques avantages essentiels : (1) la largeur des lignes est déterminée par l'embossage, qui n'a pas à tenir compte des caractéristiques de mouillage d'un système d'encre liquide ou même semi-sèche ; (2) les lignes conductrices sont intégrées, ce qui signifie que la surface est lisse ; (3) il est possible d'atteindre des niveaux de conductivité élevés, même avec des encres imprimées, sans compromettre la largeur des lignes ou la douceur de la surface.
Le dernier point mérite d'être examiné de plus près. Dans les cas normaux, pour augmenter la conductivité, il faut des lignes plus larges et/ou plus épaisses. Ici, pour augmenter la conductivité, on peut augmenter la "profondeur" de la rainure (bien que cela soit également soumis à diverses limitations).
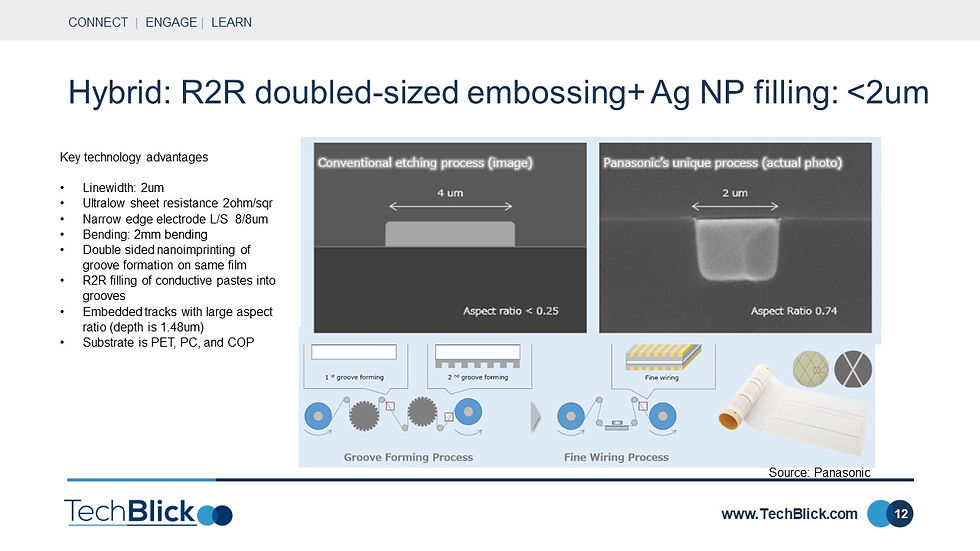
La diapositive ci-dessous montre une variation du concept précédent. Ici, l'innovation consiste à créer d'abord une fine couche d'ensemencement de NP d'Ag (à l'aide d'une raclette) dans la rainure gaufrée avant de plaquer du cuivre. Cette approche permet d'obtenir une conductivité élevée grâce à l'utilisation de Cu plaqué, et non de pâte imprimée. Par conséquent, elle permet des applications efficaces de chauffage transparent sur de grandes surfaces.

Je vous rappelle que la photolithographie, y compris la photolithographie R2R, peut également créer des caractéristiques ultrafines, y compris des mailles métalliques. J'ai inclus ici un exemple de DNP (Dai Nippon Printing) qui représente l'état de l'art. Dans les générations précédentes, il était possible d'obtenir des lignes de 2 um pour des films à maille métallique double face de taille moyenne avec une résistance de feuille de 1,5 Ohm/qr. Les derniers résultats montrent qu'il est possible d'obtenir des films à mailles métalliques d'une largeur de ligne de 1 um et d'une résistance de 2 ohms/sqr à partir de cuivre gravé. Ces résultats sont inclus ici pour montrer le niveau de performance de la technologie alternative non-imprimée.
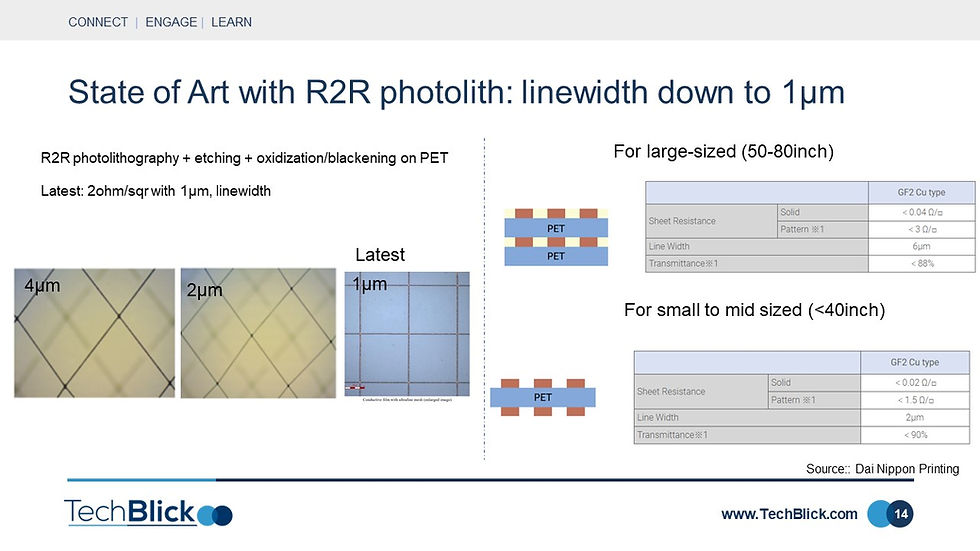
Enfin, sur ce thème, je voudrais également présenter les films à mailles métalliques de PolyIC, Kurz. Ces films à mailles métalliques ont une largeur de ligne de 10 um et un espacement de 100 um avec des couches ultrafines (100 nm) de NP d'Ag imprimées. J'ai inclus ces dernières car je ne connais pas la technique d'impression exacte.
Notez que ces films tactiles capacitifs sont déjà commercialisés dans des applications automobiles, remplaçant les interrupteurs mécaniques par des interrupteurs capacitifs. En plus des propriétés de la maille métallique, une innovation clé ici est le "Functional Foil Bonding", qui permet à ces films à maille métallique d'être intégrés au dos de pièces plastiques façonnées avec des couches de décoration. [This is automatically translated from English]
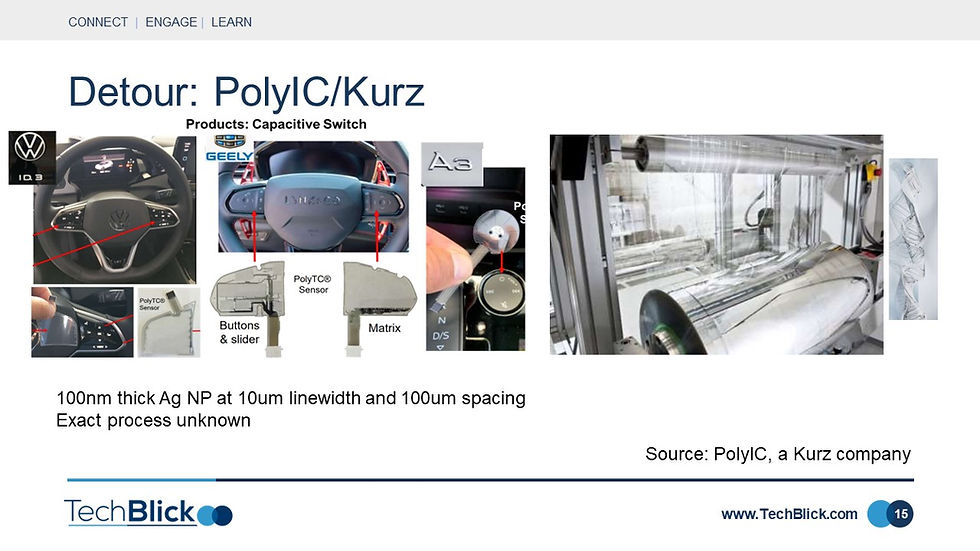
Festival des innovations : Électronique imprimée, hybride, 3D, InMold, textile
24 juin 2022 | 14:00 - 19:00 CET | Plate-forme d'événements virtuels
Asada Mesh aura un stand virtuel au festival de l'innovation.
Visitez le stand virtuel d'Asada Mesh