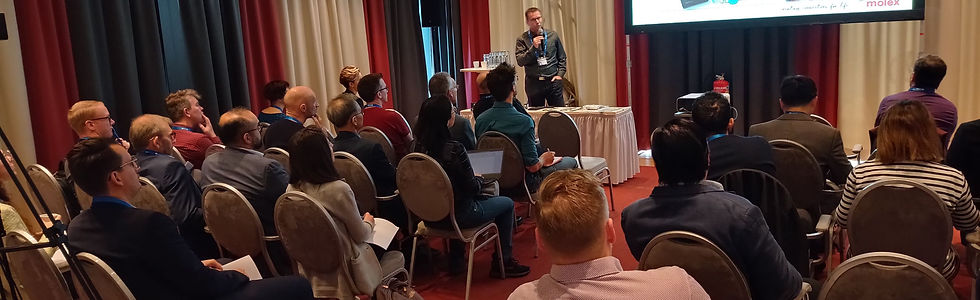
On-Site Masterclasses
There will be three parallel tracks of industry-led masterclasses on 22 October 2024, the day before the conference. Each 45-min masterclass will cover a technology or application in detail, offering an insightful blend of practical, technological and application knowledge. These masterclasses will be delivered by industry experts & may involve live demonstrations.
The content below describes the outline of the classes. Please note that you will be able to move between tracks at the end of each class. The numbers in each class are limited to 50, and will be allocated on a first come, first served basis. PDFs of all masterclass presentations will be made available online to masterclass attendees.
Contact Chris@TechBlick.com if you have any queries.

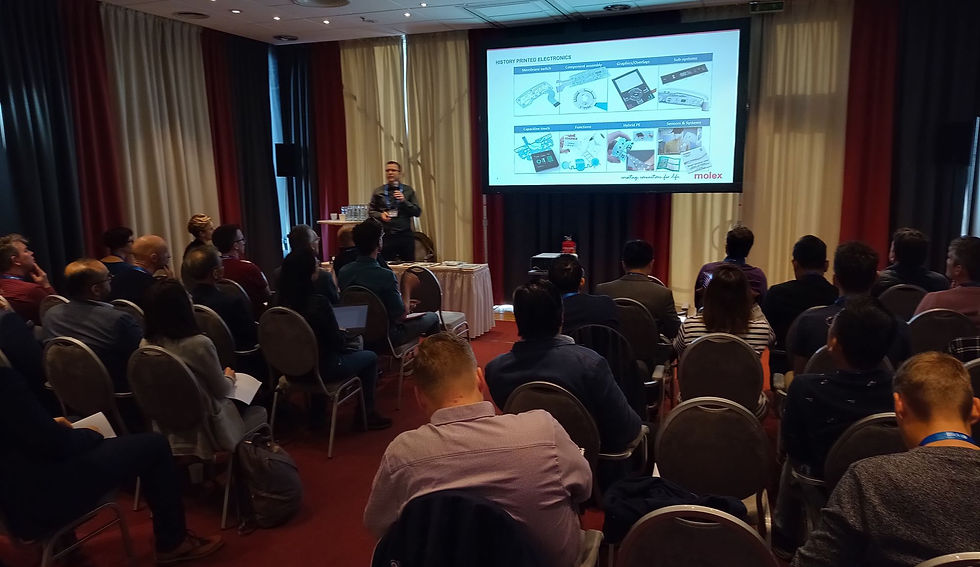
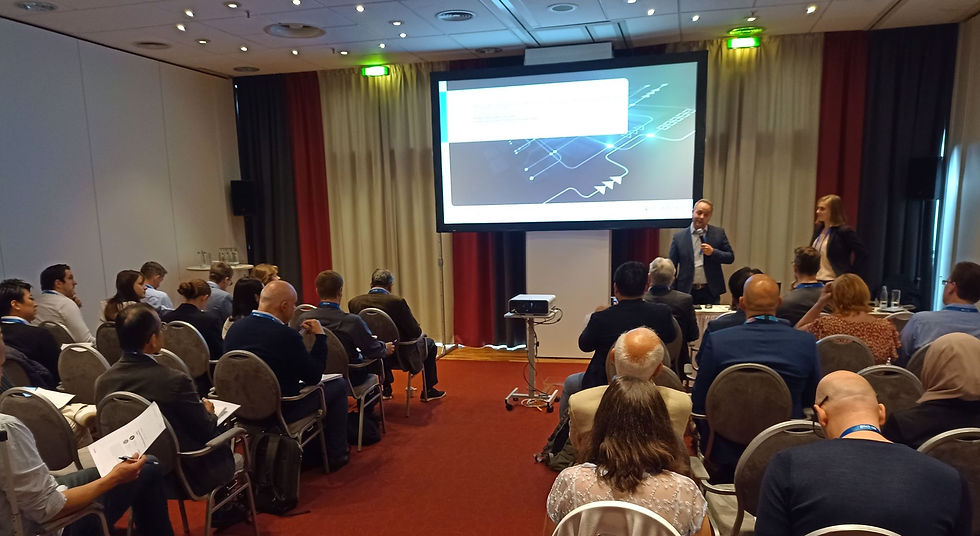

Masterclasses | Track 1

9:00 AM
Polymer Thick Film Master Class
Celanese
Saeed Madadi
This class introduces a detailed view on polymer thick film paste conductor technology. It comprises a descriptions of its main constituents, their respective functions and its critical parameters. An insight into resin and metal powder technology is given and the range of substrate materials and their properties discussed. Paste manufacturing steps and functional testing schemes for quality
assurance are summarized. Beyond screen printing alternative off- and on-contact deposition technologies as well as downstream processes are reviewed. The class closes with an overview of typical industrial applications.

10:00 AM
From Liquid Metal droplets to stretchable, self-healing, and sinter-free printed hybrid electronics
University of Coimbra
Mahmoud Tavakoli
When it comes to stretchable electronics, e-textile, smart gloves, and wearable patches, Liquid Metals (LMs) are becoming the number one choice for most researchers. But research on LMs are also entering fields of energy storage, thermal interfaces, displays, energy harvesting, and even carbon capture. This is due to the excellent combination of electrical and thermal conductivity and fluidic deformability, that makes liquid metals the first choice for many applications. However, unlike the electrically conductive inks and pastes, LMs are not easy to deposit and pattern, they are smearing, and interfacing them with microchips is not straight forward. The good news is that these problems are being addresses rapidly, and there are already some steps toward commercialization of LM based electronics.
In this master class I will summarize the research on liquid metals during the last 15 years, and will demonstrate various aspects of liquid metals. The talk will be divided into 3 sections: Materials (Liquid Metals, LM composites, LM micro and Nano droplets), Fabrication Techniques (Deposition, Patterning and Microchip Interfacing) and Applications. I will talk about the results of electromechanical testing, and durability of circuits when subjects to over 100, 000 strain cycles. I will as well talk about the applications in the space of smart textiles, wearable patches, additive manufacturing, and mechanical sensing, and how some of the top manufacturers (e.g. in automotive sector) are already adopting solutions. If time permits, I will briefly talk about how LMs are entering the energy storage field, both as current collectors, and as active electrodes.

11:00 AM
The Role of Bio-based Materials and Additive Manufacturing in Achieving Sustainability Goals for Electronics
RISE
Jesper Edberg
Electronic waste (e-waste) poses a pressing global challenge with the World Health Organization (WHO) reporting a staggering annual generation that exceeds 50 million tonnes. Less than 20% of this waste is recycled, highlighting severe environmental and health risks associated with the disposal of hazardous materials such as lead, mercury, and flame retardants. This challenge is further compounded by the overreliance of the global economy on rare earth elements and critical raw materials. Addressing this crisis requires a concerted effort to align with the United Nations Sustainable Development Goals (SDGs), particularly Goal 12 (Responsible Consumption and Production), which emphasizes reducing waste generation and promoting sustainable practices. Achieving this goal requires a paradigm shift in the electronics industry. Our course delves into the urgent need for sustainable materials and manufacturing methods within electronics. We explore alternatives to synthetic, often non-sustainable materials like PFAS (per- and polyfluoroalkyl substances) which persist in the environment and harm ecosystems. - Enter biobased materials—nature-inspired alternatives: Derived from renewable sources like trees, plants and algae, these materials offer a greener path. We’ll explore their properties, applications, and potential to revolutionize electronic design. - Additive Manufacturing and Printed Electronics: Create intricate electronic components layer by layer, minimizing waste and energy consumption for thin flexible solar panels, printed circuit boards, sensors, displays and more. We explore how these innovative techniques can reduce environmental impact. Join us on this journey toward sustainable electronics. Let’s design a future where innovation meets responsibility.

12:00 PM
Chip Interconnections for Flexible Printed Electronics.
Beckermus Technologies
Aviv Ronen
In this masterclass we will learn the packaging hierarchy and learn how the chip interfaces and structure can help us in building a reliable electronic system. We will see how wire bonding, although famous, is not suitable for the flexible electronic eco-systems and than we see how flip chip bonding is better but still has it disadvantages.
We will see how solders and conductive adhesive has their pros and cons and how they both suffer from thermal mechanic stresses when bonding in elevated temperatures. Therefore, we will see why there is a motivation for lowering this temperature not only because the materials cannot withstand these elevated temperatures.
Masterclasses | Track 2

9:00 AM
Electroactive Polymers & Applications Focus on sensors & Actuators
Arkema and KEMET
Fabrice Domingues Dos Santos | Valerio Zerillo
In this Masterclass we will introduce the use of electroactive polymers for organic, printed and flexible electronics.Electroactive polymer is a class of different materials that convert electrical energy in Mechanical energy.Different types of electroactive polymers exists : Dielectrics, ionic, ferroelectric, Relaxor ferroelectric. Among them, ferroelectric polymers do the other way, converting mechanical energy into electrical energy. With these unique properties EAP find numerous applications and developments in printed and flexible actuators, sensors, energy-harvesters etc..In this Masterclass, we will introduce the different class of electroactive polymers and their applications.We will then focus on the processing and emerging applications of ferroelectric Polymers in sensors.In a third par we will introduce the use of electroactive polymers in flexible applications from AR/VR to Medicals.

10:00 AM
R2R Flexible Hybrid Electronics: printing, assembly and testing
TracXon, Lohmann
Ashok Sridhar | Volker Lutz
In this joint masterclass by TracXon and Lohmann, an in-depth view of R2R manufacturing technologies that are essential for next-gen Wearables and IoT devices will be provided, based on practical examples.
These technologies include, but not limited to, R2R screen printing, SMD component assembly, downstream conversion processes such as lamination and die cutting. Furthermore, key considerations on materials selection will be highlighted.
Different testing methods and protocols that are essential in qualifying the IoT and Wearable devices will also be introduced in this masterclass. Based on experience we will provide an estimation of manufacturing scales to adopt increasing demand for new products.

11:00 AM
Digital Additive Manufacturing of Electronics: Inkjet, Aerosol, EHD Printing, Microdispensing and Beyond
Printed Electronics Ltd
Neil Chilton
In this masterclass, you will learn about all key digital additive techniques for manufacturing electronic devices - in 2D, 2.5D, and 3D. These techniques include inkjet printing, aerosol printing, electrohydrodynamic printing, microdispensing, and beyond. This class introduces the techniques and include practical insights and real-life application orientated advice on technology use, selection and operation

12:00 PM
Techniques for optimizing an inkjet printing process for printed electronics
ImageXpert
Jochen Christiaens
In this masterclass, ImageXpert will discuss new technologies for the development of printed electronics. These tools allow you to build a better understanding of your inkjet process, improve performance, and accelerate your rate of development. We will explore the latest analysis tools, from new dropwatching technologies to smarter inspection tools."
Masterclasses | Track 3

9:00 AM
Opportunities for improving sustainability and circularity for electronics
VTT
Liisa Hakola
The EU is proposing a Regulation on Ecodesign for Sustainable Products (ESPR) that sets requirements for all products in the EU market to become more sustainable, circular, energy-efficient, and environmentally compatible. The EU has specified electronics and ICT sector as one of the priority sectors that the ESPR will regulate. The current electronics industry causes significant direct and indirect environmental impacts, such as the formation of electric and electronic waste (e-waste), great demand for critical raw materials (CRMs), and high energy consumption during manufacturing. Therefore, actions are required to meet the requirements from the upcoming regulation. The electronics industry has several opportunities to increase its sustainability and circularity. These include among others (1) shifting from fossil-based, critical and rare materials to renewable, bio-based and abundant materials; (2) utilization of additive manufacturing processes that offer material and energy efficiency; and (3) utilization of circular economy business models for extending product use life with e.g. reuse, repair and recycle concepts. Since typically 80% of the environmental impacts are determined during the design phase, the product design is a critical stage when targeting more sustainable products that must balance between cost, performance, and sustainability aspects. This masterclass specifies sustainability (environmental, social, economic) and circularity for electronics industry, covers areas with opportunity for more sustainable approach, highlights means to improve environmental sustainability (green electronics), and discusses the relevant regulatory aspects.

10:00 AM
Wearable Sensors: Applications, Technical Requirements, and Manufacturing
Screentec
Mikko Paakkolanvaara
In this masterclass I will go through the basics of different kind of wearable sensors and typical applications used in the field of medical electrodes. Technical requirements and properties of the materials typically used for wearable sensors will be presented together with the cost distribution of materials on disposable medical electrodes. I will also talk about the sustainability aspect of materials used as well as manufacturing possibilities for different kind of sensors.

11:00 AM
From Fabric to Future: Mastering Smart Textiles and Wearable Technology Integration
Elitac Wearables
Guus De Hoog
In this masterclass keynote, we delve into the cutting-edge realm of integrating electronics with textiles to create revolutionary smart clothing and wearable technology. As the line between fashion and functionality blurs, this session provides a comprehensive exploration of the latest advancements, techniques, and innovations driving the smart textile industry forward. Participants will gain insights into:Integration Techniques: Understanding the state-of-the-art possibilities in seamless incorporation of electronics into textiles: sensors, actuators, interconnections, power, and more. Selection of the Best Option: Evaluating different technologies and approaches to determine the best solutions for your specific applications and needs. Design and Development: Navigating the design processes and challenges in creating aesthetically pleasing yet highly functional smart garments.Applications and Use Cases: Examining real-world applications, from healthcare and fitness to safety, and beyond, showcasing the transformative potential of smart wearables. Future Trends and Opportunities: Identifying emerging trends and potential opportunities in the smart textile market, preparing for the next wave of innovations.Join us to unlock the potential of smart textiles and wearables, transforming ordinary garments into extraordinary technological marvels that will shape the future of fashion and functionality. Whether you're a designer, engineer, entrepreneur, or enthusiast, this keynote will equip you with the knowledge and inspiration to pioneer in the burgeoning field of wearable technology.

12:00PM
From Sustainable to Circular: these are the challenges for Printed Electronics
Holst Centre
Stephan Harkema
The environmental impact of electronics has to be reduced. Therefore, we need to make the transition from petrochemical materials to bio-based, recycled or bio-degradable alternatives. This important first step is within reach. The second step is to reduce the complexity of products and the amount of materials used. The result: lower impact from materials and manufacturing, but also reduced fuel emissions during a product’s lifetime. Many other circular strategies must be implemented if we want to further reduce a product’s impact. One such strategy would be to prevent replacement before a product’s end-of-life by extending its lifespan through repair or refurbishment. But what if we have exhausted all these circular strategies? How can we recover the valuable materials and components if these materials are fused together? This presentation addresses some of the challenges involved with end-of-life treatment of hybrid & printed electronics.

Quantica
Digital Printing of high viscosity pastes
Quantica is an advanced additive manufacturing company headquartered in Berlin, Germany. Their groundbreaking inkjet-based technology, NovoJet, transforms production by enabling the digital deposition of high-viscosity and high particle-load materials. With their advanced systems, users can print and combine new materials seamlessly in a single process for 2D and 3D application development. From car coatings to printed electronics to hearing aids, Quantica's technology offers an innovative new solution.
On this tour, attendees will gain insight into the research and development behind Quantica's printheads and systems. Additionally, they'll have the opportunity to witness a live printing demonstration, showcasing the technology firsthand.
Quantica is a 30 minute drive from Estrel Congress Center, transportation will be provided. Places will be allocated on a first come, first served basis.


-
As part of the Fraunhofer-Gesellschaft, the Fraunhofer IAP in Potsdam is developing future-oriented solutions all along the polymer and nanomaterial value chain to support customers in their transition towards sustainable materials, processes and business models. The institute specializes in synthesis and processing of materials in an environmentally-friendly and cost-effective way from laboratory to pilot plant scale.
-
On this tour, attendees will get insights into the research divisions “functional polymer systems”, “biopolymers” and “polymeric materials and composites”. Key topics are quantum dot materials and devices for displays and lighting, organic and perovskite photovoltaic devices, polymer solid electrolytes for batteries, PFAS-free membranes for fuel cells, electrochromic devices, materials and processes for sensors and actuators, highly conductive and chemically resistant carbon fibres based upon cellulose, integration of microelectronics and photonics into polymeric compounds, and microfabrication of medical devices.
-
Participants will be guided through Fraunhofer IAP pilot plants and labs on-site in Potsdam: clean room area for the printed electronics, pilot plant for fibre technology from spinning up to carbonization, and through labs for polymer and quantum dot synthesis.
Fraunhofer IAP is a 60 minute drive from Estrel Congress Center, transportation will be provided. Places will be allocated on a first come, first served basis.
Fraunhofer IAP

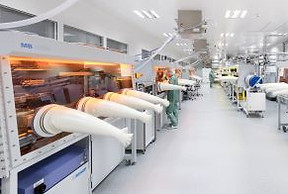

Fraunhofer IZM
Fraunhofer IZM is a 45 minute drive from Estrel Congress Center, transportation will be provided. Places will be allocated on a first come, first served basis.
As part of the Fraunhofer-Gesellschaft, Fraunhofer IZM specializes in applied and industrial contract research. Fraunhofer IZM’s focus is on packaging technology and the integration of multifunctional electronics into systems. Fraunhofer IZM was founded in 1993 and is today one of the global leaders in microelectronics and microsystems packaging. The focus lies mainly on material, process and substrate development, characterization and simulation, advanced system engineering, assembly and interconnection technologies and environmental engineering. Fraunhofer IZM is employing about 438 employees and graduate students with its main branch in Berlin. Together with its partner institute at the TU Berlin it is running a ~1000m2 clean room of with full thin film and packaging capabilities from 4” to 12” wafers.
The guided tour at Fraunhofer IZM is organized by three working groups. “System on Flex" advances flexible hybrid electronics, stretchable electronics and electronic textiles by developing scalable manufacturing processes and transforming novel concepts into production-ready solutions. The “Technologies for Bioelectronics” group designs, fabricates, and tests active neural interfaces and flexible, biocompatible implants for neural stimulation and recording, exploring new methods for stimulation and wireless power transfer. The “Sensor Development and Integration” group develops micromechanical sensors for various applications, offering complete services from concept to testing, using semiconductor effects for high sensitivity and linearity.
Participants will be guided through our labs for flexible and stretchable electronics assembly and characterization. In our clean room tour we will demonstrate the variety of assembly technologies on small and large panel size substrates such as flip chip bonding and various technologies such as finest line patterning of flexible, stretchable and rigid substrates. The Substrate Integration Lab focuses on the integration of microelectronics into flexible and stretchable substrates. This includes several processes such as lamination, laser patterning, mechanical drilling and milling, thermoforming, and various types of inspection and qualification tools. On the other hand, the Lab of Technologies for Bioelectronics focuses on the fabrication of flexible electrodes for neural stimulation and recording, protection of active implantable devices using soft materials, and wireless ultrasound energy transfer and communication for deep implants. The Mechanical Testing Lab enables the customization of standardized test methods for specific applications and is used to characterize the electrical and mechanical properties of devices as well as their lifetime. Furthermore, in combination with our Textile Lab, we will provide an overview of our in-house developed AI-based non-invasive system for monitoring cardiovascular insufficiency by integrating bioimpedance spectroscopy and other sensor technologies into smart textiles.
-web.jpg)


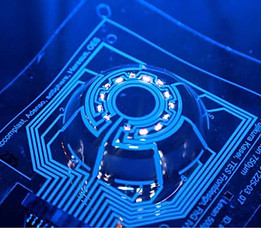

Inuru
This tour is full
Inuru is a 30 minute drive from Estrel Congress Center, transportation will be provided.
(!) Please register in advance for this tour by sending a message to christoph@techblick.com to secure your spot.
Inuru simplified the production of OLED through printing, making it not only affordable but revolutionary. Changing branding, medication and clothing and in the future replacing every single LED with a more sustainble alternative.
Inuru's vision is to bring OLED technology to the level of maturity, to produce low-cost displays can replace static surfaces of packaging and clothing. Towards a society without waste!

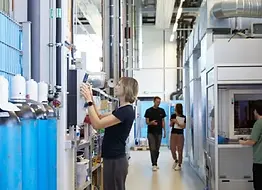