
Airbus
Alois Friedberger
Senior Scientist
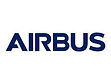
3D printed and hybrid electronics durability under aeronautic conditions
Sensor and electronic integration on aircraft structures enables real time monitoring of structural loads and environmental parameters such as temperature and pressure. The direct integration on composite structures without the need of conventional housings, connectors and cabling reduces weight, complexity and installation effort. We have investigated approaches based on flexible hybrid electronics (FHE) technology with electronic devices being embedded in thermoplastic polyurethane (TPU) foils and these functionalized foils being integrated on aeronautic composite coupons. Alternatively, similar structures have been fabricated using Additively Manufactured Electronics (AME). So far, only limited information was available on the durability of such AME structures. The talk will cover an overview on potential aeronautic applications, manufacturing of our test structures and results of the extensive durability tests of the FHE-based structures as well as test results on the devices made by AME.

Holst Centre | imec
Stephan Harkema | Maarten Cauwe
Program Manager

True competitiveness of printed electronics: is it really more sustainable than PCBs?
Printed Electronics has many advantages compared to traditional printed circuit board (PCB) technology. The simplified process flow and additive nature of the technology also make it a good candidate for more sustainable electronics. One aspect that is often overlooked when comparing the environmental impact of printed electronics to PCBs, is the dependency on the application and its inherent demands related to functionality and reliability. Moreover, the lifetime of a product is determined by the environment it is operating in and the reliability of a technology directly relates to that lifetime. Some applications may exhibit a mismatch of product lifetime and PCB lifetime, resulting in more complex technology being used than needed or vice versa, the PCB lifetime limiting the lifetime of the product. A second challenge in the comparison of printed electronics and PCB technology is the lack of data on both sides to perform an accurate Life Cycle Assessment (LCA). While volume production of PE is occurring, it is not at the same level as PCB manufacturing. In addition to the data collection, the definition of the functional unit and scope of the LCA need to be aligned. A number of cases will be presented to illustrate this challenge. Finally, the sustainability of PCB manufacturing is not set in stone. Many developments are ongoing to reduce the environmental impact of the process, the materials and the generated waste. These developments address some of the inherent disadvantages of the technology and may surprisingly tip the balance back in favour of the PCBs.

AdapTronics
Lorenzo Agostini
Co-Founder & CEO

Thin-layer electro-adhesive gripper technology with printed flexible electronics
Robotic grasping is an action of fundamental importance in all kinds of automated processes, but also a huge challenge since there is a current lack of versatile and effective solutions to grasp objects of different shapes, size and materials in any context, from industrial automation to Space. Recent advancements in electroadhesive technologies have shown great potential to overcome current limitations. Its simple electrostatic principle of operation can be employed to generate adhesive forces to grasp and release any object on command.
What really unlocks the full potential of this technology is the fact that compact devices can be manufactured in a scalable and reliable way by leveraging the benefits of printed flexible hybrid electronics, such as lightweight and adaptable components, which integrate seamlessly into various surfaces and allow for greater design freedom and compact system development.
Thus, this presentation will delve into printed electronics manufacturing processes, including inkjet and screen printing, as well as laser-etching techniques, employed to produce prototypes of electroadhesive devices, from laboratory prototipe to industrial scalability.

Air Force Research Laboratory
Christopher Tabor
Research Scientist

Liquid Metal Inks for Printed Stretchable Electronics
Liquid metal technologies are progressing at an increasing rate, opening up new capabilities, applications, and functionality at smaller dimensions. Most composite and thin film printed conductors must be geometrically engineered to tolerate excessive strain and remain conductive; however, liquid conductors take the volume of their encapsulation. Gallium specifically is of interest here as it forms its own insulating casing that allows it to be patterned at fine features and to generate stable colloidal suspensions used as inks for printing. Additionally, liquid gallium alloys are ideal for many of the extreme environments in which flexible hybrid electronics are being asked to operate, to include extreme mechanical loads as well as extreme cold and space conditions. In this talk, I will discuss the work done at the Air Force Research Laboratory within my group to understand the fundamental nature of gallium alloys used for stretchable electronics and how we have designed them to be used as a drop in replacement for more traditional printed electronic inks (e.g. silver, carbon) to be processed using screen printing, blade coating, extrusion, and material jetting techniques. While it is fairly straightforward to generate suspended gallium alloy particles in solution, the work that our team has done to engineer the surfaces of these particles, understand the thin oxide shell growth dynamics, control the oxide composition, and correlate these properties to mechanical properties that effect the final mechanically sintered conductive traces will be discussed. A few select applications will be briefly discussed, including soft electrodes for long term physiological monitoring, actively heated textiles, and stretchable data cables utilized in soft robotic inspection tools.

Alpha Micron
Pedro Coutino-Soto
VP of Technology

Guest-host liquid crystal system for AR/VR/XR applications
Augmented Reality (AR/XR) devices are a fast-expanding part of the wearable electronic industry that has attracted significant attention in recent years. One aspect that has hindered their growth and penetration into the broader consumer market is the lack of control of ambient lighting that in tandem with the image combiners such as waveguides control the image display contrast in different lighting conditions. Some technologies such as photochromic and twisted nematic LCDs have been attempted to address this issue. However, their optical and environmental performance was not considered acceptable. Guest host liquid crystals are a new class of materials that are now being successfully employed in commercial AR/XR eyewear to address this issue. In addition to enabling the required image contrast in different lighting conditions, the GHLCs have demonstrated the ability to reduce the overall power consumption of the device and as such extend the battery life during operation. This presentation will focus on this technology, its performance, and implementation in select XR devices.

Beckermus Technologies
Aviv Ronen
CTO
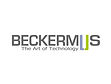
Challenges of interconnections between chips and flex substrates
In this lecture I will give a short intro to bare die chips and their different interfaces to the outer world like mechanical interface, electrical interface, thermal interface and more. Some slides about different technologies of mounting chips to flexible substrates will be presented such as using wire bond, solder and electrical adhesives. In the last part of the lecture I’ll give some daily examples of challenges in implementing these interfaces between the chips and flexible substrates.

Binghamton University
Mark D. Poliks
Professor

Wireless Vital Sign Monitoring Devices for Ambulatory Aeromedical Care
General societal trends across the globe, including a shortage of centralized laboratory and medical facilities, aging populations with increasing incidence of infectious and chronic diseases, earlier diagnosis of diseases, personalized medicine, companion testing for pharmaceutical use, government initiatives and insurance acceptance, are all important factors behind continued demand for reliable, low-cost, wireless, wearable health monitoring and medical devices. In this presentation, we will highlight our recent efforts towards development of two generations of single use Vital Signs Monitoring (VSM) devices, both allowing for continuous measurement of multiple vital sign parameters, including ECG (heart rate), respiration rate, 3-wavelength reflective PPG (pulse oximetry), skin temperature and motion (3-axis accelerometry), for up to three days. These patches are designed to measure the vital signs parameters of interest at anatomically relevant locations to achieve clinical relevancy. Robust wireless Bluetooth communications capabilities developed in this program allow for ease of implementation and integration with both mobile (Android based) devices and Cloud platforms. The multi-parameter patch prototypes are fabricated in a manufacturing relevant environment, using multiple medical device manufacturing suppliers with GMP certifications, to ensure realistic pathways for low-cost single use devices that can be FDA cleared in the future. This project is a result of a long term collaboration with Azar Alizadeh, Andrew Burns and their team at GE Research.

BotFactory
Carlos Ospina
CEO

Rapid PCB Manufacturing
We present a remarkable amalgamation of a conductive and insulating ink printer, solder paste extruder, and pick-and-place machine encapsulated into one singular product, designed to accelerate your PCB prototyping from weeks to mere minutes. Upon uploading your design, our intuitive software navigates you seamlessly through the printing journey, enabling the creation of a fully assembled and functional 3D Printed circuit board swiftly. Explore how our PCB 3D Printer can revolutionize your electronics manufacturing pace!

Ceradrop
Frédéric Soulier
General Manager
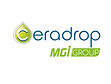
Digital Printed Electronics solutions : enabling industrialisation
How advanced digital Printed Electronics equipment enables seamless transition from prototyping to mass production. Illustrated use cases to discover how to industrialize Printed Electronics process

Coatema Coating Machinery GmbH
Thomas Kolbusch
Director Sales, Marketing, Technology, VP

Tech Pillars of the green hydrogen economy – how to scale the production methods for PEM Fuel cells from lab2fab.
The author describes the process of scaling up coating and drying technologies for the indirect or direct coating of platin catalyst on the membrane or to the gas diffusion layer. A state-of-the-art coating tech like slot die is being explained and the next tech development for digital fabrication of PEM fuel cells using a LIFT technology and laser drying are being explained. As a summary, the author shows how important standardization and inline quality controls are for further development stages of PEM fuel cells.

Creative Materials
Brian Violette
Application Engineer

Advances in Materials for Additively Manufactured Electronics Skin Patches
Electronic skin patches have emerged as promising platforms for various biomedical applications, including healthcare monitoring, prosthetics, wound care, stimulation, rehabilitation, medicine delivery, and human-machine interfaces. Advances in flexible and strechable supporting films and compatible functional materials have enabled conformal integration of sensors onto the skin, facilitating real-time monitoring of vital signs, pressure profiles, motion, and environmental parameters.Careful selection of all materials of construction as well as the geometries of the patch are critical to ensure the maximum durability of the end device while maintaining user comfort. This includes consideration of the thicknesses and moduli for mechanical matching of substrates, functional, and decorative material features. The chemical compatibility of these materials, and design considerations with regards to the interfaces to conventional electronic devices are also important to be properly engineered for mechanical matching. A multivariable design of experiments is necessary to optimize the final device bill of materials and design for reliability, performance, and comfort.

DECATHLON
Christophe Dupuis
MecaPlasTronic Leader

How Plastronic LDS process can reduce CO² emissions for Electronics devices
DECATHLON is committed to reducing its CO² impact by 20% by 2026. In order to meet this ambition, we started by actions like to reuse recycled materials or to reduce the weight of our components, but these levers will not be sufficient to achieve our target. We have no other choice but to explore disruptive solutions that break with standard technologies in order to respond to the climate challenge.This presentation aims to present the study of a concrete application of LDS technology on a headlamp product.
We will present first the Environmental evaluation of the LDS process to focus then on the Carbon footprint improvement compared to conventional technologie, without forgetting finally the technical and economic evaluation of LDS technology applied to the case study.

Danish Technological Institute
Nina Nielsen
Specialist

DTI Printed Electronics: On body eTextile sensors for physiological and neurological monitoring
The demand for flexible, stretchable and sustainable electronic solutions is growing rapidly due to the growth in eHealth, automotive, smart buildings and other similar application areas. At the core is printed electronics, which uses printing technologies such as screen, flexographic and inkjet printing, together with functional materials and inks to fabricate electronics directly onto plastic foils, paper or textiles. To de-risk European industry to adept these novel materials and technologies, Danish Technological Institute (DTI), has established a One-Stop-Shop, which facilitates European industry with consultancy, development and pilot production. DTI can take novel ideas and perform proof of concept projects, develop these into full prototypes and in many cases, upscale prototypes to a pilot scale. Furthermore, DTI can provide support throughout the entire value chain, from materials to final products. In this presentation, you will witness DTI's work on novel material formulations, particularly focusing on bio-based and sustainable printable materials, including 2D material inks. DTI will also showcase various fully functional eTextile demonstrators and prototypes they have developed, including a fully functioning wearable EMG sleeves using bio-based materials, heated wearables and an EEG headband.

Elephantec
Sugimoto Masaaki
Co Founder/SVP
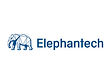
Printed Electronics as sustainable solutions
Elephantech is a company that develops manufacturing processes for Flex PCBs utilizing metal inkjet printing technology. We plan to introduce new technology that pushes the boundaries of circuit manufacturing using inkjet printing.

Essemtec
Irving Rodriguez
Product Specialist

Enhancing circular economy by facilitating the repair of electronic components
A circular economy and sustainable electronics are a must in the modern industry, not only for environmental reasons but also for commercial ones. Facilitating electronic repair helps to prolong the life span of products, enhance their performance and to correct production mistakes. Dispensing and placing a fine pitch component manually is very time consuming and could cause collateral damage to the already populated devices. A novel automatic repair method and tools with no human interaction were developed. This method uses the advantages of medium jetting, pick-and-place and quality control in one instrument, making it extremely accurate, reliable, and cost-effective. This method can be applied to replace components on PCBs and for BGAs reballing. The use of different alloys including low-temperature soldering (LTS) is feasible. The results show that this technique significantly improves the throughput and yield of the repaired devices.

Exxelia Micropen
RJ Greco
Business and Product Development Manager

Functionalization of Medical Devices Using Additive Dispense Technology
Medical device designs are constantly evolving as the trend to make passive devices functional is taking over the market space. Using additive dispense technology, one can print conductive traces, sensors,and markers on a variety of different medical device products.The direct printing system, Micropen, is a CAD/CAM driven capillary dispensing tool akin to an ultra-precise micro-dispense gun. If a material is flowable and can be loaded into a syringe, the Micropen can print it onto virtually any surface. It’s a non-contact, additive printing technique that dispenses the precise amount of material needed. This makes it beneficial when using novel, expensive or rare inks. The efficient use of materials and the ease of changing them provides product designers with increased prototype control as well as reducing time-to-market. Direct printing is an ideal way to form many different patterns on 2D substrates giving them superior electrical characteristics. However, the capabilities of the Micropen don’t stop at 2D substrates. Printers have been designed with 5-axis of movement. This allows many different medical device form factors to be printed such as thin, flexible,irregular, and highly three-dimensional shapes.This talk will provide an overview of the Micropen additive dispense integration with a variety of products in the medical device arena.

FOM Technologies
César Omar Ramírez Quiroz
R&D Senior Scientist

The role of slot-die coating in the future of photovoltaics.
Solar cells, crucial for reducing global CO2 emissions, must reach a capacity of 70 TW by 2050 for a swift transition to renewables. Sili-con technologies dominate, boasting well established supply chains, processes, and markets. However, enhancing power conversion efficiency (PCE) while maintaining cost effectiveness remains challenging. Tandem solar cells, combining two cells to capture different parts of the sunlight spectrum, offer promise. Silicon-perovskite tandems, particularly, show potential for efficiency gains. Perovskite-based materials could disrupt efficiency while aligning with current manufacturing methods, offering a rapid solution to climate change.This review examines fabrication routes for perovskite-based photovoltaics' industrial integration, focusing on non-concentrated tandem designs. Challenges include processing decisions, but slot die coating emerges as a scalable and efficient solution. Its potential for rapid processing on non-flat substrates makes it strategic for advancing the field.

Flexoo
Jean-Nicolas Tisserant
Head of Development

Novel printed pressure sensors for mass customization.
Printed pressure sensors have been widely employed and mass-produced for several decades now. They find applications for example in medical applications, inventory control, video games, robotics, and athletic apparel and sports equipment. Most of these sensors are based on force sensing resistors (FSR), typically polymer-carbon or polymer-metal composite materials whose electrical resistance decreases with applied pressure. FSR-based sensors still suffer from strong limitations in terms of performance, regarding the ability to calibrate them towards quantitative pressure measurement. Such sensors are subject to two common errors which affect their accuracy and repeatability, hysteresis and drift. These are typically still so high that a quantitative measurement of weight and weight distributions using currently produced FSR sensors remains extremely challenging. We developed a novel, patented, FSR sensor configuration to overcome both hysteresis and drift to a very large extent, compared to competing FSR sensors with this new sensor, we can for the first time propose calibrated FSR-based printed pressure sensors in the range 1-103 N/cm2 with an accuracy of some %, depending on the pressure applied. This sensor configuration not only improves drastically the sensor performance but also loosens the alignment requirements between the two parts of the FSR sensors. These new sensors allow a tremendous number of applications in the field of quantitative pressure measurement. We illustrate their benefits in the form of a printed personal scale, a quantitative pressure mapping system for electric vehicle battery monitoring as well as other large-scale applications in logistics. These best-in-class sensors are printed continuously on a roll-to-roll machine, with loose alignment constraints, making them very competitive in terms of costs and manufacturing volumes.

Forvia
Damien Bouisset
Director Marketing and Business Development
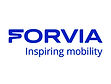
Strategy for interiors using printing electronics
Printed Electronics & In-Mold Electronics are two technologies with strong potential benefits for the automotive industry.
FORVIA and its Interior Business Group is investigating how to use this techno for different use cases, functionalizing standard interior plastic based components and bringing more value to their customers.
Interior Lighting is one of the most fast growing segment where new technologies such as Printed Electronics & IME enable to embed lighting elements to IP and DP.
However, there is still technical challenges to over come for those technologies to become a standard and replace existing solutions.

Fraunhofer ISE
Roman Keding




Thinner than a human hair - fine line metallization for next-generation silicon solar cells
The metallization of solar cells with the finest printed lines is one of the most demanding disciplines in the field of printed electronics. Finest lines which are smaller than a quarter of a human hair have to be printed on fragile silicon wafers with high throughput and without interruptions. The aim is to shade as little of the active cell surface as possible and at the same time to ensure high conductivity. Various printing processes can be used for fine-line metallization. In this article, the challenges of solar cell metallization as well as various innovative processes and current results are presented. A special highlight is the metallization of ultra-fine line contacts with a width of only 14 μm.

Fuelium
Marina Navarro Segarra
Researcher
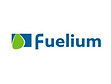
Fit-To-Purpose batteries for responsible portable electronics.
This talk presents a rationale for ecodesign portable batteries by re-thinking their life- cycle under an environmentally conscious framework. Through careful device design and advocating for a ‘fit-to-purpose’ approach, the development of these batteries is paired with the application value chain, in such a manner that even the power source end-of-life is redefined according to the use-case scenario. Several examples of these ecodesigned portable power sources will be
presented. Firstly, a paper-based battery commercialized by Fuelium to power portable diagnostic devices. These liquid activated batteries can be fabricated under the same procedures used in the rapid test industry and have shown the ability to power the most relevant features needed in portable medical devices, such as sensors, displays, wireless communications or heating. Then, further battery concepts developed at BCMaterials will be introduced, such as a bio-based battery using laser induced graphene current collectors in a cardboard tape format for smart packaging, as well as different approaches of biodegradable batteries for precision agriculture and environmental monitoring. Developed under this rationale, environmental sustainability has been placed as a core priority to guide the batteries’ conception and materialization, from materials to end-of-life. Hence all materials used as electrodes, electrolytes, or structural components are abundant, non-toxic and renewable; selected to meet the specific end-of-life requirements and endow a safe and ethical manufacturability.

Fuji Corporation
Ryojiro Tominaga
Project Leader




New era of additive manufactured electronics with the integration of SMT process and machine.
Additive manufactured electronics is efficient approach for the view point of capability of shape and speed, environmental friendly process. Since the process and material differ from common PCB manufacturing method, the important thing is that the part mounting technology will also be transformed and integrated accordingly. In the presentation, we’ll show the worldview of future electrical device manufacturing driven by additive manufactured electronics with the integration of SMT process and machine.

Global Access Diagnostics (GADx)
Kevin Land
Head of Innovative Research and Development

Advancing Innovative Diagnostics for Global Health
In recent years, numerous innovative products and technologies have been developed, offering significant advantages in the field of affordable medical diagnostics. These advancements span diverse areas, including communication, data transfer, power and energy storage, optical and biosensors, and readout systems. They are further enabled by advanced manufacturing techniques such as printed and functional electronics, new materials, microfluidics, and microsystems engineering, all of which support large-scale and low-cost production. The challenge now is to refine these technologies further and achieve a greater degree of integration, enhancing affordability and accessibility in low- and middle-income countries. The REASSURED criteria can be successfully harnessed to drive a mission-oriented approach in these developments.

Hahn-Schickard Institute
Zhe Shu

Hybrid 3D printing of conductive bulk metal and dielectric polymer for sustainable and smart 3D electronics
Electronics are the dispensable element in the current modern society and new era of industrial 4.0, Internet of things (IoT), smart homes, wearable electronics as well as modern health solutions. However, the current electrical circuits manufacturing such as printed circuit boards (PCB) are mainly relying on the complex factories with a series of expensive instruments, consuming large amounts of etching chemicals and producing toxic wastewaters [1,2]. Moreover, the electronics are also limited to 2D rigid FR4 boards, which highly hinder it for individualized smart systems. Printed electronics offers high potential in integrating sustainable electronics on flexible and large area surfaces. It has advantages of high resource efficiency, miniaturized usage of energy in both fabrication and utilization, reduce the usage of the hazardous chemicals, higher potential in recyclability and usage of the biodegradable materials. However, it still faces some critical challenges: a) usage of chemicals and solvents; b) required of post-treatment; c) expensive particle-based ink d) high restriction on 3D printing In this talk, we introduce a hybrid printing system where the polymer/dielectric substrates can be directly printed from FFF technology. The StarJet technology is directly integrated into the 3D printing system as the 2nd extruder which prints the bulk metal (e.g. SAC305 solder) through digital and non-contact deposition of the molten metal droplets or Jet. Compared to current printed electronic technologies, the StarJet technology provides advantages of bulk electrical conductivity, conform printing, no pre- and post-treatment, high compatibility on flexible substrates due to solvent-free printing. Furthermore, when the bulk solder (e.g. Tin silver copper alloy) is used for the molten metal printing, the SMD components can be directly soldered and bonded onto the large-area flexible substrates. It eliminates the troublesome solder reflow process and simplifies the fabrication process. In the contrary to the high temperature of the StarJet printhead (e.g. 320 °C for soldering printing), the printed molten metal structure has high adhesion, high flexibility and no damage to the temperature sensitive polymer foils, textiles, and 3D-printed plastics. The high flexibility has been also shown on foldable polymer foils, where the printed circuits can be folded into a small part and stay fully functional after unfolded. A highly simplified workflow is also introduced where non-experts can make electrical designs and generate hybrid 3D electronic models. Then the hybrid 3D printing system will take care of the rest of printing. With this hybrid-printing platform, it provides high potential to direct prototype 3D electronics and integration of smart sensors with highly conductive traces, direct soldering, and without any post-processing (e.g drying, sintering).

Hamamatsu Photonics
Alexander Goerk




Thermal Laser Processes in Printed Electronics
Sustainable and rapid post-processing for high volume production

Hasselt University
Wim Deferme
Professor

ACT-3D_Assembly and Connection Technology for 3D plastic carriers
Smartization of existing or new products is a trend that is linked to Industry 4.0 and Internet-of-Things. There are several ways to integrate electronics into or onto 3D products. The combination of printed electronics for circuit layers and the assembly of rigid electronic components onto those circuit layers is one of the solutions that is getting a lot of attention nowadays. However, hybrid electronics (as the combination of both printed and rigid electronics) or structural electronics (as products aim to be 3D), needs adapted materials and processes to achieve functional conductive traces and interconnects. In this presentation we present the process of screen printing of conductive Ag-based inks on different 2D foils and the subsequent thermoforming of the same to achieve 3D circuit layers on which, afterwards, rigid electronics can be placed via the use of pick-and-place and conductive adhesives. Besides the description of the process, the different foils and different inks are discussed in this work and the properties of their combination for functional 3D products is discussed.

Henkel | Teca-Print
Thibaut Soulestin | Dominik Aeschbach

Advancing Pad Printable Solutions with Henkel Materials
Henkel is an industry-leading supplier of printed electronics materials and services. The broad LOCTITE portfolio includes conductive inks and coatings and resistive and dielectric inks. Wireless communication has evolved rapidly over the past few decades and antennas play a fundamental role in wireless communication systems. 5G pad-printable antennas are especially unique to the mobile communication industry and Henkel has developed a range of pad-printable inks that enable direct printing on 3D-shaped surfaces. Pad printing of functional inks can be viewed as an alternative technology to more traditional Laser-Direct-Structuring (LDS), offering an additive manufacturing process that is more environmentally friendly. Henkel has started a technical collaboration with Teca-Print to accelerate our customers' projects. Teca-Print is a Swiss-based world-leading machine and consumables supplier for pad printing. In this presentation, we will discuss pad-printing process parameters and focus on the properties of the LOCTITE portfolio that make these inks unique.

Horizon Microtechnologies
Andreas Frölich
CEO
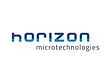
Hybrid Microfabrication by 3D printing and subsequent Coating for Electronics and Radio-Frequency Applications
Additive manufacturing technologies with precision and resolution on the micrometer scale (micro AM) today are realistically being looked at as viable production technologies, and are no longer the expensive and slow processes of a decade ago. If properly used, the design freedom of micro AM allows of higher miniaturization, functional integration, better performance, or reduced size, weight and power consumption of parts and components. However, most micro AM technologies work with photopolymers which lack certain functionalities. Combining micro AM-derived parts with coating technologies for non-polymer materials that are able to conformally coat 3D substrates is an efficient approach to overcome the lack of functionalities of bare polymer parts. It brings together the benefits of photopolymer based 3D printing such as precision, repeatability and relatively simple processing with the functionalities which the respective coatings can achieve. This talk will present a process portfolio for depositing thin (<10 µm), conformal, electrically conductive, protective and metallic films on three-dimensional polymer substrates made by micro-AM processes to enhance the functionality of the polymer microstructures and their application in radio-frequency devices and electronics.

ISC Konstanz
Tudor Timofte
Senior Scientist




Copper ink and electrically conductive adhesives for future PV production
Copper ink and electrically conductive adhesives for future PV production Achieving net-zero emissions by 2050 will require a significant expansion of PV production capacities, accompanied by a drastic reduction of Ag consumption in solar cell metallization compared to today's standards. We demonstrate the application of new mentalization concepts for high-efficiency c-Si solar cells (TopCon and IBC) based on screen-printed Cu inks and investigate their performance and reliability. This screen-printed approach can serve as a drop-in replacement for Ag inks and drastically reduce Ag consumption and production costs for PV manufacturing. In order to realize lead-free solar cell connections and to facilitate the production of PV modules with temperature-sensitive cell concepts such as silicon perovskite tandems, we are also introducing ECA based cell-cell connections that use minimal amounts of Ag-filled materials.

Jiva Materials Ltd
Jack Herring
Chief Product Officer

Soluboard: An alternative end-of-life solution for PCBs
In an industry dominated by incumbent fibreglass-epoxy rigid PCB laminates, there is an alternative. With a laminate containing biodegradable natural fibres, thermoplastic water-soluble polymer and a non-brominated flame retardant, PCB waste can now be classed as non-hazardous, benefitting from more than a 60% reduction in carbon footprint compared to the FR-4 incumbent as well as water solubility at end-of-life to avoid incineration and increase precious metal recovery rates.
The laminate is processable through industry standard fabrication/assembly processes to produce functional PCBs with electrical, mechanical and thermal properties comparable to the market incumbents. This recyclable solution for PCBs is considered to be the missing piece of the puzzle on the road to circularity.

KIMOTO
Christoph Bosshard
General Manager
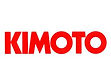
Adhesive carrier and protection films for advanced manufacturing
Advanced production processes require protection of sensitive surfaces and materials, while other processes require the fixation of parts or stretchable substrates for efficient processing. The challenge is to find the best possible combination of base film and adhesive for a given material combination and environmental condition. After processing, the film must be released without adhesive residue to prevent unnecessary process steps. In cooperation with our customers, we developed a wide range of different solutions with variable adhesive strength, that when combined with specific base films, allows to extend the application and temperature range. Our presentation will focus on typical examples as well as on some special use cases, that are currently under development for areas such as: Printed electronics, sensors, batteries, displays and micro LED’s.

Karlsruhe Institute of Technology
Martin Ungerer
Research Associate
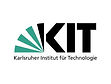
The Aerosol-on-Demand (AoD) jet-printing principle:
a novel concept for 3D-printed electronics
Additive manufacturing of electronics is experiencing increasing demand. Since neither molds nor printing forms are required, the integration of functional electronic components onto 3D objects by means of digital printing technologies such as inkjet, extrusion, aerosol and electrohydrodynamic printing facilitate mass customization. Due to a constant jet width over a large range, aerosol jet printing has the advantage to allow printing onto 3D surfaces without adaptation of the distance between the printhead and the object. However, existing aerosol jet printing systems require the printheads to be orientated in the direction of gravity, operate only continuously and thus need a shutter system to realize discontinuous structures. We develop a novel Aerosol-on-Demand (AoD) jet-printing system that solves the major challenges of digital printing technologies. The core of the patented AoD technology is a new method for aerosol generation from a point-like source within the printhead directly in a sheath gas flow, which hydrodynamically focuses the generated aerosol by means of the inner contour of the attached nozzle. Based on the results obtained by first experiments we implement a CFD model of the printhead. CFD simulations show the feasibility of the hydrodynamic focusing of the locally generated aerosol as well as the existence of stable operating points. Furthermore, the simulations lead to the design of a test setup. Experiments with the test setup verify that aerosol generation can be controlled on demand and thus printing of discontinuous microstructures is possible without ink loss and need for a shutter. There are no aerosol-conducting parts other than the nozzle, i.e. there is no dead volume and no material waste. The minimum ink volume and the cleaning effort are extremely reduced; ink degradation occuring in common atomizers is eliminated. In addition,after a short initial run-in period for the sheath gas no further run-in period is required for the aerosol jet. The aerosol mass flow can be controlled inline to provide a constant ink transfer rate over a wide range of printing speeds. Finally, the printhead can be freely rotated in space during the printing process. Thus, it is also possible to print on stationary components of complex 3D-shape. In conclusion, the novel AoD jet-printing principle shows great potential for applications in functional printing of 2D & 3D electronics

Marquardt GmbH
Wolfgang Käfer
Technical Project Manager
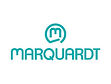
Printed electronics: why is it difficult to leave the ‘trough of disillusionment’?
Marquardt is a mechatronic specialist for almost a century now. Beginning with the production of electrical switches, Marquardt became a serious international automotive supplier for control elements, vehicle access and driver authorization, as well as battery management systems. Other areas Marquardt supplies sensors and switches to are the white goods and power tool market, and the off road and agriculture sector. Do printed electronics enable new applications or is it just about cost optimization? At Marquardt, printed electronics are in focus since around ten years, although the first application dates back to the early 2000s. In this speech, you will get an overview about the developments and applications of printed electronics in the past years at Marquardt. Nevertheless, Marquardt uses printed electronics only to a very limited extent, so where do we see opportunities and which obstacles do we have to overcome to enter the ‘slope of enlightenment’ and to reach the ‘plateau of productivity’?

Meta
Li Yao
Research Scientist

Noninvasive Biopotential Sensors for Future Wearable Electronics
Noninvasive biopotential sensors have garnered considerable interest for their potential use in wearable electronics because of their capability to capture diverse physiological signals without piercing the skin. This approach presents multiple benefits over conventional invasive methods, including enhanced comfort and diminished risk of infection. The development of noninvasive biopotential sensors is a rapidly evolving field with numerous applications across healthcare, fitness monitoring, and human-machine interfaces. In the consumer electronics sector, there exists a significant demand for the reusability of biopotential sensors, rendering many technologies designed for the healthcare industry unsuitable for consumer electronic applications like wearable wristbands. This talk offers an overview of the current state of noninvasive biopotential sensors for future wearable electronics, encompassing various measurable biopotentials, such as electroencephalography (EEG), electromyography (EMG), and electrocardiography (ECG). It will also emphasize the challenges related to the materials used in noninvasive biopotential sensors, particularly in electrodes. Finally, the talk will spotlight the encouraging future prospects for noninvasive biopotential sensors, including their integration into wearable devices and the potential influence on human-computer interactions.

Metafas
Luc van Neer
CEO

Printing Electronics: Technical and Business Transition from the manufacturing of Membrane Switches to Printed Electronics, including smart textiles and smart plastics.
Metafas is a high level screen printing company with more than 30 years experience in printing electronics. We have developed from screen printing front foils and membrane switches to printing sensors on (non-)stretchable substrates, including connectors, pick-and-place, cutting and assembly. The company has transformed from a local build-to-print manufacturer for the machine- and electronics industry towards a supplier & partner for smart applications in the Automotive, Healthcare and Consumer electronics. In this presentation, Luc will guide you shortly through this journey, and explain how system integrators can benefit from this, and you will learn (both upsides and downsides) from various cases and projects.

Momentive | BSC Computer
Jan Geboers | Andreas Schneider
Head of Technical Service & Application Development

Sustainable Motion based on Silicone
Highly efficient, biocompatible linear actuators can be produced from silicones. Structures like artificial muscles that contract when an electrical voltage is applied and relax again just as quickly. In this presentation, the authors will discuss how bring this Dielectric Elastomer Actuator (DEA) technology is being brought to market maturity and can replace small motor-gear units with highly energy-efficient and maintenance-free DEA solutions.The DEAs are stacks of thousands of individual silicone layers with conductive coatings. The motion dynamics depend heavily on the silicone base material used and the dimensions of the stacks. Specific solutions are specified for a maximum force of up to 20N and a compression of up to 8% of their length at rest. The DEA’s electronic control unit generates and regulates the required high voltage of approx. 800 V, protects against overvoltage and takes care of charge, trickle charge and discharge management. The electronics are designed so that they can be used with standard supply voltages in battery operation and are extremely energy-efficient. This makes DEA technology easy to integrate into end products: The module and its interfaces fulfill the approval requirements in the voltage range used.In this presentation, we will provide background information on all the components for the use of DEA technology in real products. Sustainable motion through dielectric elastomer drives is becoming a reality, and the first end products will be launched on the market in the course of 2024.

NRCC
Arnold Kell
Research Officer

Molecular Inks for Printed Electronics
A suite of silver and copper molecular ink (MINK) platforms will be described. MINK is particle-free alternative to traditional flake-based inks that can be formulated for a variety of printing methods, including screen printing. MINK can be processed by traditional thermal methods, broadband UV light and intense-pulsed light to produce thin and narrow traces with exceptional electrical and mechanical properties including excellent tolerance to bending, flexing and elongation. This talk will discuss how several properties inherent to MINKs have enabled the design and manufacture of novel printed electronic devices. In particular, we will focus on the development In-Mold Electronic (IME) devices where, the inks are printed in 2D and thermoformed to create 3D Human-Machine Interface (HMI) Devices. We will also highlight some recent examples of their incorporation into 3D printing applications and the processing advantages they can offer.

Nagase ChemteX
Alan Brown
Business Development Manager

Conductive Inks for Wearable/ Stretchable Electronics
As wearable and stretchable electronics applications continue to evolve, conductive inks have an integral role in the fabrication of these applications. From the silver ink to the dielectric ink there are multiple variables that must be taken into consideration when designing the device. Whether it’s choosing an appropriate substrate, if hydrogel is going to be incorporated or even if the application needs to be washed, ink selection is critical. In this presentation the roles inks play and testing that must be considered will be discussed.

Nano OPS
Ahemd Busnaina
Founder and CTO

Fully Additive Manufacturing of Electronics at the Nano and Microscale for Making Active Components and Integrated Circuits
We introduce a new sustainable and scalable technique to additively manufacture nano and microelectronics. The technique eliminates etching, vacuum deposition and other chemically intensive processing by utilizing direct assembly of nanoscale particles or other nanomaterials at room temperature and atmospheric pressure onto a substrate. The presented technology enables the printing of single crystal conductors and semiconductors [1]. The technology enables the additive manufacturing of passive and active components at the nano and microscale using a purely additive (directed assembly enabled) process utilizing inorganic semiconductors, metals, and dielectrics nanoparticles. The process demonstrates the manufacturing of transistors with an on/off ratio greater than 10 6 . This new technology enables the fabrication of nanoelectronics and electronic compenents while reducing the cost by 10-100 times and can print 1000 faster and 1000 smaller (down to 25nm) structures than ink-jet based printing. Printed applications such as transistors, diodes, display [2], MEMs [3] and all carbon electronics [4], and sensors at the micro and nanoscale using inorganic and organic materials will be presented. Nano OPS introduced the world’s first Nanoscale fully-automated printing system (NanoOPS) prototype with built-in alignment and registration. This is the only demonstrated solution for high-throughput printing of interconnects and circuit components at a scale equal to or less than 2 microns on rigid or flexible substrates. This new Fab-in-a-Box is designed to print electronics and products with minimum features down to 600 nm and is expected to democratize the electronics industry by eliminating the current high-cost entry barrier.

Neotech AMT
Johannes Hörber
Product Development Manager

3D Printed Electronics – Towards Sustainable Mechatronic Systems
This presentation will review the current status of 3D Printed Electronics (3D PE) and the move towards sustainable mechatronic systems. The use of 3D PE processes offers significant advantages in terms of product form, functionality and economics as well as sustainability by way of simplifying the materials mix, improved materials efficiency and compressed process chains that localise manufacture. The fundamental technology combining free-form, 5-axis 3D printing of mechanical and electronic components, Surface Mount Device (SMD) placement and pre- and post-processing techniques, is described. The State-of-the-Art of the manufacturing process chain is demonstrated by way of a proof-of-concept study of a novel lighting product. Additional use cases for the medical, automotive and wearables industries will be briefly presented.

NextFlex
Scott Miller
Director Of Technology
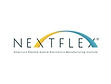
Hybrid Electronics Innovations and Ecosystem: A U.S. Perspective
Hybrid electronics are at an inflection point, with products currently on the market that rely on this manufacturing paradigm, many products in late-stage development, and even more opportunities poised to take-off. Applications in medical, aerospace, and consumer electronics, structurally integrated systems, and advanced packaging are all rapidly moving forward. As the U.S. Manufacturing Innovation Institute focused on Hybrid Electronics, NextFlex convenes a broad ecosystem of companies, universities, and government partners to advance technology, create and mature domestic manufacturing capabilities, and support the education and training of the workforce for this manufacturing sector. This talk will describe the Institute’s approach to carrying out its mission, provide examples of technical projects, and offer perspectives on exciting new opportunities for the ecosystem.

Notion Systems
Kai Keller
VP Business Development
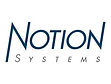
Advancing Additive Processes into Electronics Mass Production - Breaking Boundaries One at a Time
Additive technologies, and in particular digital printing processes are a very powerful tool in the hands of electronic designers and solution providers. The main area of adoption for additive technologies, however, still is in prototyping and low volume manufacturing. Nevertheless, additive technologies unfold their real potential only when implemented in mass production process chains. Qualified additive processes in electronics mass production provide means to improve quality of end products and to implement new features & solutions with zero time to market. In this presentation I will focus on how the inkjet solder mask process increases flexibility while maintaining stability in PCB mass production. I will also speak about limitations of the current inkjet process and provide an outlook on how they can be overcome by new EHD printing technologies.

PERC
Alkim Akyurtlu
Professor/Co-Director

Additive Manufacturing for Advanced Microwave and RF Applications
Additive approaches have been motivated by the need for rapid prototyping and systems that are flexible, lightweight, conformable, and wearable. There is growing need to adopt Additive Manufacturing (AM) technologies for Radio Frequency (RF)/Microwave (MW) electronics motivated by the need for rapid prototyping and the production of RF systems that are flexible, lightweight, conformable, and wearable. Printing RF electronics for DoD applications (e.g., radars, communication systems) is challenging since the requisite materials, components and systems demand higher performance than required for low frequency applications. Materials play a critical role in the application of AM to RF and MW applications. Development and characterization of low-loss dielectrics, ferroelectric inks, and convertible inks are essential in printing devices that will provide desired performance metrics. The formulation of new materials, including UV curable dielectric, resistive, and ferroelectric inks, and characterization of their properties at microwave frequencies, are key challenges in applying additive manufacturing to printed RF and microwave devices.Details of these challenges and ways of mitigating them through specific applications, which exemplify all stages of development, will be presented. Details of the key enablers for these applications and devices will also be described. Recently, there has also been interest in applying Additive Manufacturing (AM) in packaging of microelectronic devices. Additive packaging offers advantages of expanded functionality in restricted volume, through miniature, low-SWaP-C sensors, allowing for non-traditional form factors. In this presentation examples of additive packaging including, design, fabrication, and characterization of a non-planar multi-material MMIC structure as well as bare-die integration is presented to demonstrate significant footprint reduction and circuit compaction. The results of this work show that fully additive approach is feasible for non-planar circuits, which will allow for footprint reduction, weight reduction, and achievement of novel form factors that are critical for microwave applications.Finally, describe several printed devices and subsystems, including tunable Frequency Selective Surface (FSS) based filters, wearable metasurface filters, and printed connectors will be provided. Our work includes multi-physics-based design and modeling as well as the development of printing/processing technologies using various direct-write printers for these applications.

PROFACTOR
Pavel Kulha
Senior Scientist

Concept for direct integration of electronic circuits and sensors on textiles using inkjet printing.
The paper presents a new concept of integration of electronics and sensors directly on textiles by additive manufacturing namely inkjet printing and dispensing. A breath rate sensor, accelerometer and pulse sensor were integrated on a stretchable fabric with their conditioning circuit and their performance was evaluated using a tensile stretching machine to mimic human respiration. The device enables wirelessly data transfer to a base station for futher data analysis.

Papierfabrik Louisenthal GmbH
Dr. Christoph Hunger
Project Manager R&D

Large-scale fabrication of low-haze transparent metal mesh foils
Indium tin oxide is widely used in transparent applications such as heated glass, antennas, touch screens or smart windows, but has limitations when it comes to e.g. brittleness and low resistances. Metal mesh structures offer a cheaper alternative for truly flexible and low resistance applications.A self-assembled crack template approach enables a fast R2R production on a large-scale. The metal mesh foil based on PET or PC shows both high transparency and low optical haze.

PolyPhotonix
Richard Kirk
CEO
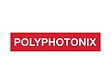
Saving Sight with Light: Treatment for Diabetic Eye Disease.
The World Health Organization regards diabetes as a global epidemic and estimates that there are 422 million people living with the condition. Diabetic Retinopathy is a serious sight threatening complication of diabetes. Two thirds of Type 2 and nearly all Type 1 within 20 years of their initial diabetes diagnosis develop the condition and it is a major cause of world blindness. Current treatments involve expensive and invasive injections of drugs directly into the eyeball and place a huge treatment burden on patients, carers, clinicians and national healthcare budgets. As a result, current treatments are not used in the early stages of eyesight deterioration, rather they are withheld until oedema levels are significant and serious vision loss has already occurred. In most countries, outside of the West, intraocular injections are simply not affordable, and many patients go blind from diabetes.The solution is the Noctura 400 Sleep Mask, a highly effective, low cost, safe and non-invasive home use device which is a CE certified medical device which delivers a low level of light through closed eyelids during sleep and manages the oxygen demand of the retina. This avoids nocturnal hypoxia which is a known driver of diabetic retinopathy. Recent clinical evaluations undertaken in the UK by the NHS resulted in 96% of patients seeing clinical improvement. Of the patients expected to receive injections within 12-months, none progressed to the point of requiring injections. The visual acuity in 98% of eyes was improved, some up to 15 letters. Follow up studies have shown that patients who still using the mask 3 years on have still not progressed to injections.

Pragmatic Semiconductor
Vincent Barlier
Director

Bringing flexible intelligence to Medicine 3.0
Healthcare is undergoing a quiet revolution, shifting from traditional models that respond to symptoms, to proactive, personalised care that prevents issues before they arise. Technology is key to this paradigm shift. Next-generation devices – such as wearable sensors and point-of-care diagnostic tools – promise patients a convenient and interconnected digital health experience. But their widespread adoption depends on their ability to achieve the necessary performance at low cost. In this presentation, Vincent Barlier introduces FlexICs – ultra-thin, flexible semiconductors – and the pivotal role they will play in this healthcare revolution, delivering performance at an appropriate price point, while maximising ease of use and patient comfort.

Printed Electronics Ltd
Neil Chilton
Technical Director
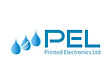
Experience-Driven Process Selection and Scale-Up in Printable Electronics: Manufacturing-led insights from micron to metre scale.
With decades of experience in printable electronic manufacturing, PEL offers valuable insights into scaling up production processes. This presentation covers key considerations for successful transition from prototype to full-scale production, including machine, process and material selection. Additionally, we introduce our open-access facility, where our team supports customers in their development journey while minimising costs and maximising resource utilisation.

SPGPrints
Tom Overgoor
Product manager

The 3 C’s of de-risking industrialized Printed Electronics production
In this talk we will take you through the journey of scaling up Printed Electronics production along the 3 C’s of de-risking industrialized production: Cost, Capacity and Certainty. Using real-life customer cases we will dive into the technical and application-design decisions you need to make to ensure steady and predictable production. We will share some of our experiences with finding the right balance between pattern design, inks, substrate and choosing the correct production method. Once the functionality of the application is proven, there are several scenarios to scale up to full production. We will explain how to choose the best scenario for your business while minimizing risk.

Semikron Danfoss
Michael Schleicher

Classifying Additive Electronic Manufacturing Technology: From 2D to 3D and From Simple to Complex System
Additive manufacturing processes have today reached the middle of industry. In some industrial
sectors, the “Hype Cycle” [1] is moving into productivity. The first companies have set up "Digital
Warehouses". The digital printing principle makes it possible to realize "System in Package" (SiP) with higher variety, compared to previous technologies. Currently known manufacturing processes for Additive Manufacturing (AM) are described within standards bodies. Additional materials and methods were developed permanently. There are many possible combinations of materials and procedures, which may seem confusing from outside. From an electronics design & manufacturing perspective, there are unanswered questions and a huge variety of complex procedures. Classifying from the perspective of the Application, the user can identify useful tools, methods and materials which are needed for simple or verry complex AME projects. A side effect can be to optimize processes or to identify gaps in the workflow and closing them and to get a first impression of the possible costs or e.g. the CO2 footprint/sustainability effects. The goal of a classification is supporting user, designer, hard- and software vendor taking advantage of the technology and get in discussion! In previous discussions, the “FED Arbeitskreis 3D Elektronik” has coordinated the classification with institutes and industry partners.

Sun Chemical
Philip Nicholas
Technology Lead

Biosensor Materials Requirements – Challenges and Opportunities
Biosensor materials are used in electrochemical sensors for medical, agricultural, and environmental monitoring. The range of applications is expanding and extends to medical and wearable electrodes; for health and wellbeing monitoring, as well as cosmetic applications. Material requirements and performance targets vary depending on the end-use application. With the biosensor market moving towards continuous monitoring and prolonged skin or analyte solution contact, requirements for biosensing materials increase. The presentation will provide an insight into electrochemical testing, chemical resistance requirements for biosensor materials and latest advancement in biosensor ink technologies.

Sungkyunkwan University
Gyoujin Cho




Sustainable Roll-to-Roll Printing Foundry for Realizing 4 Things: Internet of Things (IoT), Display of Things (DoT), Vision of Things (VoT), and Care of Things (CoT)
As global climate change and warming have drawn attention to a carbon footprint in ICT, a green foundry for less carbon dioxide emission has been considered especially for manufacturing flexible inexpensive devices with simple functions for edge computing applications. Therefore, a roll-to-roll (R2R) printing-based foundry has been developed as a sustainable high throughput for manufacturing inexpensive and disposable electronic and bioelectronic devices. Here, the R2R gravure printing system will be introduced to show how to manufacture a limitless number of sensor-computer integrated labels for IoT, DoT, VoT, and CoT. Through the R2R printing foundry, displays,processors, wireless modules, and sensors can be all integrated by a continuous in-line printing system by simply changing gravure rolls and electronic inks in the gravure printing system. To demonstrate the concept of the R2R printing foundry, a limitless number of integrated logic gates for developing the label-like IoT, DoT, VoT, and CoT were fabricated via all R2R gravure printing processes with precisely controlled overlay printing registration accuracy, electronic ink transfers, circuit designs, and device passivation. Furthermore, analyzing the hazardous byproducts through the R2R gravure printing-based foundry will be introduced.