
Adapttech
José Rafael Silva
Embedded Systems Engineer

Wearable medical gait sensors: the role of printed flexible electronics
INSIGHT Sense generates a 3D model utilizing new By-Measurement technologies to create a digital copy of the patient's socket that enables the analysis of objective data that shows the pressure map of the residual limb, both in static and dynamic acquisitions.

Agfa
Peter Willaert
Product Manager Printed Electronics

Up your Silver Performance - the USPs of Agfa PRELECT Silver Inks
Agfa PRELECT Sintering silver inks are developed to offer significant advantages over standard PTF inks, as they will get you more conductivity out of the silver they contain. On top of that, PRELECT screen-, inkjet and spray coating inks offer finer features and thinner layers, and they enable digital workflows in Printed Electronics applications, as we will show in this talk.

Airbus
Dennis Hahn
Project Leader Printed Electrics




The Printed Future of Cabin Electronics

Applied Materials
Marco Galiazzo
R&D manager

Advanced Screen-Printing: A Study to Entirely Manufacture a Medical Sensor by Screen-Printing
Developments in electronics and sensors have demonstrated the ability to manufacture wearable devices to remotely monitor human health in real-time at reasonable cost. A wide variety of smart sensors are now available, both on rigid and flexibRecentle substrates, to monitor the health and well-being of patients suffering from chronic illnesses. We’ve used our advanced screen-printing capabilities to manufacture medical devices: in particular, we studied and developed the realization of medical sensors entirely by screen printing. Thanks also to the constant improvements of the screen-printing ecosystem (paste, screen, equipment), enabling high processing yields and throughput, manufacturing of such devices by screen printing technology was proven to be a cost-efficient solution, compared to conventional microfabrication techniques, for mass manufacturing of healthcare devices.

Asahi Kasei Corp
Fujito Yamaguchi
Chief of Product Development




Anti-counterfeit solution that applies high-definition printing technology
Asahi Kasei has been developing high-definition R2R printing technology using seamless roll mold (SRM). As a result, we have succeeded in seamlessly high-speed printing of continuous patterns at a resolution on the order of nm from several μm in R2R printing. On the day, we will explain a new business solution (Anti-counterfeit solution) that applies this R2R high-definition printing technology. Furthermore, as another application example, "UnPad", which is the product vision we have been advocating for a long time.
"A world where people can interact with data through a set of interconnected sensors, actuators, computing and storage devices"
As an example of embodying this, we will also introduce a touchless pointing device jointly developed with TNO Holst Center.

BeLink Solutions
Pierre Ball
Sales & Marketing Director
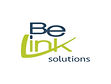
Innovative in-mold and hybrid electronics with direct PCB-on-film integration: a cost-effective way to create smart plastics solutions
This presentation will highlight the key principles of innovation in printed electronics by BeLink Solutions along 3 axes:
Equipment
Materials
Processes
Replacing incumbent technologies is usually challenging, but hybrid electronics technologies are opening up new solution and design areas that are driving the migration and expansion of the market from conventional electronics to the printed electronics market.
Here we will not only address sensors and traces based on well-known conductive screen-printing techniques, but more importantly how to integrate any variety of SMT components and packages (BGA, fine pitch) with direct PCB-on-film integration.
In other words, how to bridge the gap between both technologies (conventional and printed electronics) to foster new designs in 2D and 3D electronics?

Brewer Science
Adam M. Scotch
Director of R&D, Smart Devices

Mass-Deployable Printed Electronics for Air and Water Quality Measurements
Brewer Science's vision is to design, build, and deploy connected gas and water sensors that monitor environmental contaminants on a large scale. For the last 10 years, Brewer Science has developed the technology to print cost-effective sensors that can measure contaminants in water, such as heavy metals (lead, cadmium), nitrate, and arsenic, as well as sensors that assess air quality by measuring gases like carbon monoxide, carbon dioxide, hydrogen, and oxygen. Producing low-cost sensors with low-power electronics and wireless communication will enable the deployment of sensors over vast areas for real-time monitoring of environmental conditions.

Brilliant Matters
Nicolas Bouchard
Business Development Associate

Sustainable advanced materials platform unlocking the lab-to-fab transition in printed electronics.
Printed electronics are bringing to life the vision of manufacturing advanced flexible electronics devices in a scalable, cost-effective, and sustainable way. Organic semiconductors, which can be formulated as inks and then printed under ambient conditions, are poised to unlock even more disruptive applications in printed electronics. The tunability of these carbon-based materials allows them to achieve key performance and processing metrics in various applications. This presentation will outline how Brilliant Matters provides added value to projects in printed electronics by offering a unique scale-up platform for environmentally-conscious advanced materials such as organic semiconductors with applications in printed electronics. Highlighted technologies include energy harvesting, light sensing, and low-power displays.

Chasm
Tom Eldridge
Business Development Director, EMEA ·
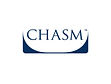
Bringing Clarity to Printed Electronic Solutions
As industries evolve, designers are challenging the fundamental nature of materials and using carbon nanotubes, and nanotube hybrids, to exceed limitations once imposed by existing materials. Carbon nanotube technology is ushering in a new era of printed electronics, introducing transparent solutions for printed electronics that push the boundaries previously known for strength, reliability, and performance.
In this presentation, we will review several existing commercial applications of carbon nanotubes for printed electronics in the automotive, aerospace, healthcare, and consumer electronics industries. As optical cameras, RADAR & LiDar sensors, antennas and other innovations continue to become ubiquitous within these devices, new nanocarbon technology continues to evolve delivering heating, connectivity, and other performance advancements with full transparency and without the use of wires. Simply put, cutting edge-developments happening now using nanotechnology are the biggest innovations in the printed electronics industry that you will never see

Coatema Coating Machinery GmbH
Thomas Exlager
Scientist, Slot-Die Expert

How to Make PE More Sustainable.
The talk is about the production of nanocellulose by slot die coating and drying process to replace PET plastic substrates. This process was part of the European project Greensense and on the nanocellulose there had been printed a biosensor platform. So the talk covers coating, printing and drying technologies in combination with sustainable materials.

DuPont Micromax
Andree Maindok
Senior Application Development




Designing Conductive Inks for the Market: Focus on Bio & eHealth
DuPont Microcircuit and Component Materials (MCM) continues to expand our portfolio of screen-printable inks (carbon, conductive, and dielectric) for use in the growing biosensor and health/wellness/fitness markets. These inks enable production of reliable, consistent, and high-accuracy electrodes used in medical monitoring, diagnostics, drug delivery, and wearable electronics. Through partnership with our customers and understanding of new market dynamics our new offerings include stable solvent-resistant inks, flexible/stretchable/washable inks for wearable applications, and thermally curable inks for abrasion resistance and long-term stability.

DuPont Teijin Films
Valentijn von Morgen
Business Development Manager

Polyester Film Solutions That Are Meeting The Changing Needs in Flexible Electronic Markets
Continued advances in the Flexible and Formable Electronics is driving the material suppliers to provide functionality to meet wide ranging demands for applications such as displays, TFT backplanes, energy harvesting and storage, sensors and Human Machine Interfaces.
This talk will give a brief overview of PET and PEN product range meeting wide ranging application needs.
Thereby the focus will be on the recent progress made with the development of Kaladex® PEN substrates for extreme processing requirements, formable PET films for in-mold electronics, films with ultra clean and smooth surfaces for ultra-barrier and high resolution structures and combining UV absorption, weather resistance or fire retardancy whilst also offering more sustainable solutions with the incorporation of recycled materials in the substrates.
DuPont Teijin Films (DTF) has launched many Mylar®, Melinex®, and Kaladex® polyester films through collaborations with partners in the flexible electronic industry as our DTF has proved to be uniquely capable of offering customised and affordable polyester substrate solutions

Eastman Kodak
Carolyn Ellinger
VP, Printed Electronics
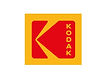
Manufacturing Using High-Resolution Flexography
Many everyday products contain mass produced printed electronic components. Each mass-produced printed component is a replicate of the last, making their manufacture well suited for “analog” print manufacturing, such as flexography. The use of high-resolution printing enables smaller individual features and finer increments in size - enhancing the ability to print high-fidelity patterns with very complex shapes. These benefits, among others, enable improved form, fit, and function for the user of products manufactured using these techniques.
In this talk an overview of the benefits of high-resolution, additive manufacturing will set the stage for a more in-depth investigation of high-resolution flexography. The focus will then turn to addressing the challenges of making high-resolution patterns that are truly functional. A technical assessment of using print (or print-enabled) manufacturing to get sufficient material (z) height for function while maintaining the small x-y features will be presented. Examples will be shared from both lab-scale and production scale evaluations.

FaceBook /META
Jim Huang
Research Scientist, Meta Reality Labs

Wearable System Design Challenges toward Human-Centric Computing
As we move from personal computing to human-centric computing, we see great promises for people to better connect with their family, friend, or colleague around the globe despite of physical distance. All-day wearable devices such as virtual reality (VR) and augmented reality (AR) glasses, wristbands, or gloves equipped with the ubiquitous connectivity can empower people to connect, feel, and interact more intuitively than using today’s mobile phones or personal computers. In my presentation, I will talk about the promises and the technical challenges of wearable systems design using flexible, hybrid, and printed electronics, and how a design-manufacture ecosystem might help.

FononTech
Rob Hendriks
CEO

Rapid printing across different resolutions, viscosities, and shapes
One of the challenges in printed electronics is the large gap between costly, high-resolution lithography, and cost-effective – but also less refined – printing technologies. A brand new and revolutionary technology has been developed that fills that gap and enables the next generation of manufacturing to start today.
Impulse Printing is a novel additive manufacturing technology that transfers high-resolution patterns through rapid surface heating. When the solvent at the heated interface reaches its boiling temperature, rapid gas generation leads to pressure build-up. This pressure causes the ink to transfer to the substrate at incredible speed. Impulse Printing has several unique features. It can deposit feature sizes ranging from several microns to many millimeters, with aspect ratios of up to 0.5. Since the ink is released from a surface, it does not experience any shear forces, which means a wide range of viscosities can be deposited. Impulse Printing can therefore solve common manufacturing challenges, including printing on any surface topology with inks of extremely high viscosity. Patterns can even be wrapped around substrates.
Impulse Printing is a non-contact and high-throughput technology, so it is compatible with large substrates, like roll-to-roll processes. It was designed to be user-friendly and to have a low cost of ownership. It can therefore be seamlessly integrated into many current manufacturing set-ups. What’s more, the solution reduces waste associated with current manufacturing techniques, as it consumes low amounts of power and utilises ink with the highest efficiency.

Forvia
James Gourlay
Technical Director
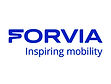
Innovations in Luminous and HMI Surfaces
DesignLED combines the integration of electronics and micro-optics to create homogeneously and dynamically lit luminous surfaces. Innovations bring together printed electronics, surface optics and surface electrodes, with polymer encapsulation or in-mold structural electronics. designLED is a Faurecia Clarion Electronics company and part of the FORVIA group.

Fuji Corporation
Ryojiro Tominaga
Business Development Manager
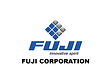
Development of an Electronics 3D Printer - Full Additive PCB Manufacturing Process Plus Low Temperature Surface Mount Technology
We’ll introduce a novel electronics 3D printer which integrates resin printing, circuit printing, and low temperature Surface Mount Technology (SMT). Based on these three key functions, we named this machine “FPM-Trinity”.
FPM-Trinity enables the manufacturing of uniquely shaped electrical devices within one day. This can drastically reduce the development time for electronic products, adding value to the process of creating new products. In this presentation, we’ll introduce key process technologies of the machine and its main features. In addition, we’ll show some of the samples which have made using FPM-Trinity.

GE Healthcare
Juha Virtanen
Principal Engineer, Wearable Sensors

Wearable Ward Monitoring Solution
Continuous ward monitoring is expected to improve patient outcome. Respiration rate has been recognized as a promising early indicator for deterioration of patient status. Department-wide solution is needed to make full benefit of the solution. Data quality and patient comfort are key factors in acceptance of a new monitoring modality. This talk will address the key technical choices behind our newly released wearable ward monitoring solution.

Henkel
Aad van der Spuij
Business Development Manager Printed Electronics EMEA

Connecting surfaces of the smart building to the cloud with sensors enabled through printed electronics.
Step into smart buildings of the future and you might not see a difference. Combining the scalability of coatings and building materials contemporary sensing techniques opens-up an incredible range of possibilities for predictive, preventative, and responsive maintenance. For Henkel, a global leader in specialized and cross-functional ink formulations for printed electronics, and Laiier a smart surface technology provider, the next decade will see the rise of smart buildings that integrate new capabilities into the built environment. Whether it’s office facilities that warn of leaking pipes, walls that heat our rooms, or floors that tell us when an elderly relative has suffered a fall, many of the core technologies are already here. Today, the challenge besides the technology innovation is more about building networks and creating markets.
The presentation will cover the unique ecosystem required to bring this vision to life that includes the whole value chain from construction, materials, manufacturing industry to IoT integrators. The session will take the attendees through technical explanations and customer use cases demonstrating clear ROIs and customer insights.

Heraeus
Franz Vollmann
Global Head of Printed Electronics

Selective inkjet printing of particle-free conductive metal ink in large scale production
Heraeus has in-house developed a full system solution consisting of particle-free metal inks, equipment and processes for the selective coating of semiconductor packages. Large scale inkjet printing and photonic curing on 300mm wafer frames has become a reality. Experience the advantages of this solution such as design freedom, material efficiency, high print accuracy and many more in various applications ranging from EMI shielding to metallization or plating replacement.

Hummink
Pascal Boncenne
Co-Founder & COO

Using capillarity for nanoscale manufacturing: introducing breakthrough additive manufacturing
Hummink will present its revolutionary nanoprinting technology that enables the deposition of any material, on any surface, with a unique freedom of design. By combining a nanometric pen with an oscillating macro-resonator, Hummink performs capillary deposition of liquids with micronic and sub-micronic resolutions, opening a new era for electronics manufacturing. Simple, fast and versatile

IDS
David Keicher
Vice President

Significant New Advances in Aerosol Printing
IDS’ novel, patented approach to aerosol printing has found very good acceptance around the world in multiple market segments and applications. The unique method for in-situ aerosol generation, minimizing transport distance and dual focusing lenses is delivering performance that is making aerosol printing ready for production.
Now, IDS will be introducing its next iteration of improvements! IDS will discuss how new standards of daily print performance are being set, accelerated aerosol transport times that exceed conventional standards by multiples, and new novel technology to facilitate rapid cycling of the aerosol stream to serve high speed intermittent applications. These new capabilities will be discussed and data will be presented showing how these improvements affect print performance. Notable measured improvements will be showcased.

Identiv GmbH
Thomas Germann
R&D Manager

Advances in Reel-to-Reel produced Hybrid Electronics for flexible NFC, UHF and Bluetooth Low Energy Tags
In Hybrid Electronics, the advantages of electronics based on discrete components are combined with those of printed electronics, in order to render new products at a price-point that would not be possible with either technology alone. Especially reel-to-reel produced Hybrid Electronics based IoT Tags promise to enable the Internet of Things vision due to their low price-point, combined with industrial reliability. The recent availability of single-chip Bluetooth Low Energy ICs in package-less form have brought about a vast amount of new possibilities, especially when combined with printed electronics based components, like printed batteries or OPV cells. In this talk, recent advances in this field are shown, based on real-life products, displaying the state-of-the-art concerning reel-to-reel produced hybrid electronics based NFC, UHF and Bluetooth Low Energy Tags

Jet Metal Technologies
Pierrick Plantevin
R&D Plastronic Engineer

The advantages of using thin silver films as electrodes for printed sensors
While the use of conductive inks is widely spread for electrodes manufacturing, in some cases it shows limitations regarding general performances and reliability. Thus, recent developments on technologies that are able of delivering reliable R2R thin film metal coating led to consider their use for printed electronics and more specifically for manufacturing various sensors electrodes.
The primary reason is the high demanding nature of a sensor that implies having good performances in terms of sensitivity, range of measurements, as well as stability over time. Pure silver offers highest electrical conductivity and, along with an extremely low roughness surface condition, this leads to a significant increase in both sensor dynamic range and yield compared to traditional conductive inks. Thin film electrode shows also better temperature stability and overall aging capabilities that extend the operating conditions of the sensor.
The metallic deposit is - by nature - not subject to any compatibility issues with sensing elements thus allowing the manufacturing of all kinds of sensors. A combination of thin film electrodes interconnected via printed conductive ink can be considered, improving the integration of this sensors within more complex systems. Finally, as for the environmental aspect, relying on thin thicknesses of metal ensures a very low material consumption and a final product that can be easily recycled.

Laiier
Matt Johnson
CEO & Co Founder

Connecting surfaces of the smart building to the cloud with sensors enabled through printed electronics.
Step into smart buildings of the future and you might not see a difference. Combining the scalability of coatings and building materials contemporary sensing techniques opens-up an incredible range of possibilities for predictive, preventative, and responsive maintenance. For Henkel, a global leader in specialized and cross-functional ink formulations for printed electronics, and Laiier a smart surface technology provider, the next decade will see the rise of smart buildings that integrate new capabilities into the built environment. Whether it’s office facilities that warn of leaking pipes, walls that heat our rooms, or floors that tell us when an elderly relative has suffered a fall, many of the core technologies are already here. Today, the challenge besides the technology innovation is more about building networks and creating markets.
The presentation will cover the unique ecosystem required to bring this vision to life that includes the whole value chain from construction, materials, manufacturing industry to IoT integrators. The session will take the attendees through technical explanations and customer use cases demonstrating clear ROIs and customer insights.

Ligna Energy
Jakob Nilsson
CTO

R2R manufactured Energy storage for IoT Applications based on Forest Materials
Energy storage based on forest residues in combination with R2R manufacturing opens up for a new range of possibilities for the IoT market. Each sensor and display in the world needs powering. This power must be green and cost efficient in order to get the intended impact from the technology. The sensor and display units, in mass-production, need to be sustainable themselves in order to enable benefits like energy efficient buildings and better consumer decision making.
We will present our way to solve this challenge and the foundation for the Ligna S-power product. We will also elaborate on how this fundamental technology can be applicable and scaled also for other storage purposes.

Ligna Energy
Peter Ringstad
CEO

R2R manufactured Energy storage for IoT Applications based on Forest Materials
Energy storage based on forest residues in combination with R2R manufacturing opens up for a new range of possibilities for the IoT market. Each sensor and display in the world needs powering. This power must be green and cost efficient in order to get the intended impact from the technology. The sensor and display units, in mass-production, need to be sustainable themselves in order to enable benefits like energy efficient buildings and better consumer decision making.
We will present our way to solve this challenge and the foundation for the Ligna S-power product. We will also elaborate on how this fundamental technology can be applicable and scaled also for other storage purposes.

LiquidWire
Mike Hopkins
VP of R & D

Soft Boundaries in Human Machine Interfaces
User interfaces with machines have long relied on tactile feedback to give crucial information to users. Whether pressure felt through a steering wheel or a clear detent on a pushbutton, people intuitively rely on this type of embodied information to communicate the state of the system under control. As machines incorporate more robotic elements this tactile feedback will need to become a 2 way street. Textiles, which are the only artificial technology human beings tolerate being in constant close physical contact with, provide an ideal platform for both sensing and active haptic communication between robots and the people who they serve. Incorporating smart textiles into apparel and active upholstery such as anti-bed sore platforms will pave the way for advanced soft robotics that can operate comfortably in close contact with people.

MacDermid Alpha
Rahul Raut
Director, Strategy and Technology Acquisition

Next Generation Assembly and Interconnect Technologies for Smart Structures and Functional Surfaces
Emerging electronic structures in consumer, automotive, medical and several other end-applications are rapidly moving towards integrated, interactive, smart interfaces from their current physical and mechanical forms (such as switches, connectors, housings, etc.). Electronics assembly, manufacturing and processing are also evolving to be compatible with the next generation of sleek, lightweight, compact form factors. Additionally, current megatrends such as sustainable and green electronics, and increasingly additive manufacturing approaches and fully automated assemblies will start to become mainstream.
To enable and deploy these next generation smart structures and functional surfaces, a combination of smart materials and compatible processes are needed. In this paper, we present a holistic view from materials, high-volume manufacturing (HVM) approaches and sustainable processes. We discuss/review key building blocks of 3D smart structural platforms that represent an integrated approach, which covers:
- Novel film substrates (for example, multifunctional PC Substrates for In-Mold Electronics),
- Highly conductive and formable Silver Inks
- High performance formable Dielectrics (Thermally curable),
- Formable Structural and Electrically Conducting Adhesives (ECAs), and
- Formable Encapsulants.
We present performance and compatibility of an integrated multi-layer stacks that can be thermoformed and then injection molded to produce smart, interactive 3D structures. Details of several technology demonstrators showcasing these leading-edge technologies will be presented. A key requirement for many of these integrated 3D structures is that they will need to meet or exceed stringent reliability requirements for automotive, medical, military and other demanding applications. Finally, a summary of key reliability testing results will be presented for the 3D IME structures.

Meta Materials
Jonathan Waldern
CTO

Nanoimprint electronic functional films for multifunctional metasurface applications
Meta Materials Inc. is developing discrete platform specific proprietary technologies for large-surface-area lithography, allowing the manufacture of nanostructures to be carried out in a cost-effective manner. Each platform employs a massively parallel patterning scheme, designed to be scalable to large areas of either rigid substrate materials and rolls of flexible films. In certain cases we use a phase-shift mask approach called Rolling Mask Lithography and in others, cast NIL printing – all allowing the creation of resonate plasmonic structures with feature sizes down to 50 nm.
In addition, we are also using a first of its kind Plasma deposition technology, which enables high speed coating of any solid material on any type of substrate. We use this metallization step in our roll-to-roll production process for functional films, including security films, which will significantly accelerate line speed and increase capacity. Large scale and efficient metallization coating of ultra-thin substrate with zero defect, is a critical step for volume production of safe reliable lightweight battery materials like separators, requiring hundreds of millions of square meters per year. Additional applications being brought to market include 5G reflection, transparent microwave shielding and windscreen and sensor-window heater functional films, all of which will be reviewed.

Nano Dimension
Shavi Spinzi
PCB Technologies Director

Roadmap for 3D AME Designs
This presentation will describe the industry drivers for increased electronic devices and circuits performance and packing density and how multi-level and multi-material Additively Manufactured Electronic (AME) technology enables corresponding innovative designs and fabrication from DC to mmWave applications. The presentation will focus on AME devices including design, materials, fabrication, and testing. This technology provides for electronic circuits not only in 2D but also in 3D where connections can be made without vias, but direct wiring between the electronic elements. The wires can be shielded and unshielded. Furthermore, the fabrication technology allows for traces with different thicknesses at the same level. Yielding fully functional boards with smaller size and lower weight, as compared to equivalent PCB fabricated ones. The presentation will include also devices with chip first embedded active ICs. Components such as capacitors, coils, band pass filters, and multilevel Fresnel lenses exhibit superior RF performance as compered Surface Mount Technology (SMT) of components.

Novem Car Interior Design
Dominique Heilborn
Director Light & Function

Integrated Products for Integrated Interiors
Integration of lighting – both, styling and function – is in the center of upcoming interior concepts. This is achieved by merging components visually, applying holistic and scalable concepts and at the same time preserving a high level day time design. Traditional electronics concepts and injection molded electronics are reshaping the future of in vehicle electronics.

Novo Nordisk
Nikolaj Eusebius Jakobsen
Principal Device R&D Engineer

Printed Electronics in Mass-Produced Medical Devices
Novo Nordisk A/S supplies nearly 50% of the world’s insulin for treatment of diabetes, and 34 million people are using our diabetes care products. On top of this we are also supplying medicine for growth disorder, haemophilia, and obesity.
In Device and Delivery Solutions, we develop delivery solutions, combining Drug, Data, Diagnostics, digital solutions, and devices to make a meaningful treatment for our end users. Most of our drugs are formulated in a liquid state, so an injection device is needed for administration. To make a link between injection data and digital solution, we need to integrate sensors and communication in our devices. Integrating electronics in the injection devices gives data directly to the user who can use the data together with a health care professional to optimize the treatment.
To get at true mass producible connected device, we have had a couple of projects with printed electronics over the last years. The presentation will take you trough a printed electronics project and share some learnings, opportunities and struggles in making a printed connectivity solution for a mass-produced medical device.

Panasonic
Tsuyoshi Takeda
Product Marketing Manager

Development of a Novel Thermoset Stretchable Film for Printed Electronics.
Panasonic Industry Co Ltd., Electronic Materials Division, a leading company in the electronics field, has developed a new high-performance film designed as substrate for FHE/PE applications. Featuring unmatched heat resistance, these stretchable films are based on a proprietary, non-silicone polymer system, freeing designers, and manufacturers from the constraints of conventional thermoplastic films like TPU and PET.
(i) Applicable to high-temperature processes: With a temperature resistance of greater than 260℃, these films withstand elevated drying temperatures for inks, coatings, and sintered materials. Even works well with typical SAC reflow processes.
(ii) High printability: It has excellent adhesion performance with a wide range of conductive materials.
(iii) Excellent reliability: The product exhibits a good durability in evaluations such as high temp/humidity tests, temperature shock tests, and insulation reliability tests.
This presentation will provide details of the substrate technology, test results, and use-case demonstration parts manufactured with these materials.

PragmatIC Semiconductor
Vincent Barlier
Commercial Director – Foundry

Sustainable Semiconductor Manufacturing
In this session we will look at the environmental impact of semiconductor manufacturing and how new manufacturing approaches can help in reducing its footprint. We will also explore the limitations of the present solutions and explain how novel flexible and hybrid electronics can lead to a reduction in carbon footprint by helping consumers, brands and retailers to reduce their waste and recycle the valuable materials that they use.

PulseForge
Stan Farnsworth
CMO




Sustainable Manufacturing of Innovative Product Concepts: Soldering on Light-weight Plastic
Electronics manufacturing is not exempt from the societal drive to improve overall sustainability, including materials and energy utilization. Multi-zone solder reflow ovens are a major energy uses due to prolonged operation at elevated temperatures necessary for reflowing traditionally-used SAC305 solder, both functionally for effecting the solder melt, as well as operationally to avoid their extended warm-up and equilibration times. At the same time, this same thermal process used for reflowing solder is a barrier to broader utilization of flexible hybrid electronics. Market demand for lightweight, conformal electronics has surpassed current traditional equilibrium-based thermal processes such as reflow soldering. Low-temperature, lightweight substrate materials such as PET, and electronic components such as cameras, sensors, and bioprocessors can typically not withstand sustained exposure to soldering temperatures.
The presenter will offer next-generation thermal processing, which decarbonizes the supply chain by utilizing as little as 15% of the energy of standard processing. Sustainable manufacturing practices often come at the sacrifice of performance and/or cost, with what can be referred to as a Green Premium. Through also providing improved performance and throughput, this new soldering technology dispels a notion of a Green Premium. The new soldering capability enables next-generation applications in applications such as medical and lifestyle wearables, consumer electronics such as AR/VR goggles, and opens the door to broader innovation while still meeting ideals and practice of sustainable manufacturing.

Quad Industries
Wim Christiaens
R&D Director

Flexible Printed Electronics: A World Of Opportunities
This talk will provide insights into printed electronics, a platform technology to create electrical devices on various substrates. Printed circuits have been used since more than 20 years for the production of user interfaces, including membrane switches and capacitive touch sensors, but the biggest opportunity in the field of printed electronics is that many new applications are emerging. Quad Industries is a leading innovator in this field, and by means of highly accurate screen-printing techniques, smart functionality is integrated on a wide range of materials such as flexible and stretchable films, textiles and paper. Some of our recent developments and applications include smart electrode patches, PTC film heaters, force sensors and in-mold electronics

Schneider Electric
Philippe Prieur
Global, Electronics Industrialization Director

3D Electronics vs Industrial Mission Profile / Case study From Schneider Electric
Schneider Electric / Company presentation
Mechatronics physical integration, constraints & compacity
Context and Proof of concept on 3D electronics applications (IME, LDS, Printed 3D)
Industrial mission profile, robustness
Antenna use case / validation plan
Sensor use case / validation plan
Perspectives and next Steps
Questions mark

Smooth & Sharp
Alan Wu
President & Founder

A NFC Biosensor Test Stripe made with Reel-to-Reel Hybrid Electronics on the same Substrate
TELETENTO® has innovations in FHE and POCT aspects.
In FHE aspect,
●Integrated Printed Electronics from NFC antenna, MCU socket to Biosensor
All the major parts are printed R2R on same substrate.
●Precise FHE assembling
Up to 10 pads MCU chip assembling in R2R operation.
●Fine Line Printing
Line width/gap < 100um for MCU socket
●Possible with Paper Substrate
Verification of all production conditions with paper substrate.
In POCT aspect,
●Further Decentralization
via NFC smartphone, testers don’t need to come to hospital or clinic for medical specimen collection.
●Risk Reduction
no need medical specimen transportation, avoid latent virus spreading with contaminated medical specimen.
Used test stripe with medical specimen e.g body fluids can be disposed onsite.
●Quick Response
Test result is informed via APP, SaaS or PaaS.
●Cost Saving
No more costly medical specimen required transportation e.g. temperature control, time.
Let contaminated medical specimen stay where it is collected.

Spark Biomedical
Alejandro Covalin
Chief Technology Officer
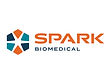
From standard flex circuit technology to printed electronics in a wearable medical device: Printing a Disposable Neuromodulation Earpiece
The use of traditional electronic manufacturing technologies has been long favored in the medical device industry. In light of rising costs due to trade wars as well as unpredictable supply chain issues, we decided to steer away from standard flex circuits and adopt a printed electronics approach to manufacture our disposable earpieces. These earpieces have to adhere to the skin and reliably deliver electrical stimulation pulses for a period of up to 24 hrs. to help people overcome opioid withdrawal symptoms. In order to minimize cost and increase the reliability of our disposable earpiece, we converted our original flex circuit design to a single-sided print and transferred all components to a specially designed double-sided spring-loaded terminal cable connector. We expect an FDA clearance for our printed electronics earpiece before the end of the year.

Stabilo
Peter Kämpf
Head of Special Product Development




Panel Discussion

SunRay Scientific
John Yundt
Vice President

Enabling Scalable Manufacturing of Printed Flexible Hybrid Electronics
Advancements in the development of flexible hybrid electronics (FHE) technologies and materials continue to progress rapidly; however, reliable, high-volume manufacturing of complex FHE-based products remains elusive. This issue becomes even more into focus when the objective is for printable, wearable technologies. Due to the nature of the stresses applied during use, such stretchable devices are expected to be mechanically robust and sustain their electrical performance under high tensile strain. Most of these stretchable electronic devices are hybrid in nature, comprising both soft and rigid electronic components. Hence, robust and reliable electrical interconnections between these soft and rigid components is necessary to ensure proper functionality of the device. Interconnections between the electrically functional control systems and wearable e-textile materials have a variety of current, traditional methods, such as high pressure and high temperature Anisotropic Conductive Adhesives (ACA), solder, snap/cinch connections, and isotropic epoxy adhesives. Each of these electrical connections pose issues with the necessary material sets for wearables/e-textile materials. There are significant drawbacks related to mechanical and/or thermal damage during the connection process; poor mechanical adhesion; inability to connect standard-pitch functional devices; and lack of robustness when connecting to nonplanar surfaces seen in wearable technology. And additional challenges exist which limit the high-volume manufacturing of these products. SunRay Scientific will present recent results in the development of a novel anisotropic conductive adhesive, ZTACH® ACE, for high-volume surface mount assembly of electrical components, including those to by mounted/attached to flexible, stretchable, textiles in wearable applications.
ZTACH® ACE technology demonstrates superiority in achieving environmentally stable and mechanically robust electrical connections. For improved manufacturability, it allows for pressure-less assembly, low-temperature cure, excellent adhesion to various substrates, and fine pitch reliability without sacrificing contact resistance or mechanical bond integrity. Because ZTACH® ACE can act as its own underfill and edge encapsulant, the rigors of use in typical wearable applications on host substrates like textiles and TPU, do not experience the same types of failures alternate competing technologies would experience without the addition of underfill and/or encapsulation. In providing superior adhesion, low contact resistance, and mechanical robustness during electromechanical testing, ZTACH® ACE proves itself to be a reliable interconnect between stretchable to stretchable/flex/rigid materials with high electrical conductivity. This enables easier and lower cost manufacturing of more flexible and robust applications through integration of SMD components directly onto e-textiles, without additional laminated protective layers. As a result, flexible, wearable printed electronics can finally be integrated into a wider range of cost effective, reliable end use application.

Sunway Communication
Nouhad Bachnak
Managing Director
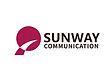
The Latest Development in 2D/3D Microcircuits
The traditional LDS (laser direct structuring) process is fantastic but only works on special plastic substrates containing sub-surface activation particles. This limits the choice and functionality of materials. Firstly, it typically does not work with glass, ceramics, PET or thermosets. Furthermore, the addition of activation particles can render a transparent material opaque or eliminate bio-compatibility. Furthermore, the linewidth resolution is typically around 80-100um (but can be pushed further down) with surface roughness of 20-30um
In this talk, Nouhad Bachnak unveils a new process, which promises to overcome these limitations. Here, the process first involves a special laser structuring process followed by a so-called chemical activation step. After this step, the structured and activated part undergoes typical plating (Cu-NiP-Au)
This is an important development and advancement of the technology, because it greatly lessens the limits on the choice of materials which can be 3D metallized with bulk-like properties and solderable surfaces
Furthermore, it will be shown that this process- when optimized- will achieve 5um linewidths with a surface roughness of just 2-3um (great for antennas, for example). It can also plate within vias with 40um diameter.
This is still not the full production level for all substrates. The most advanced development is for thermoset, which is production ready. The other substrates like glass, PET, and ceramics are still in development. Nonetheless, it is a good space to watch

VTT
Antti Kemppainen
Printed Intelligence -Solution Sales
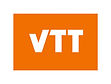
Manufacturing and Sustainability Considerations for Next Generation Wearables
This presentation highlights critical design, manufacturability, sustainability and reliability aspects related to development of novel stretchable devices for the wearables market based on thermoplastic polyurethane (TPU), polydimethylsiloxane (PDMS) and nanocellulose substrate platforms. We will present examples of several fully integrated functional devices such as a stretchable wireless electrocardiography (ECG) smart patch and a disposable enzymatic amperometric biosensor for real-time sweat monitoring. Developments and upscaling aspects on Roll-to-Roll manufacturing will cover double-sided printing and via-forming, component assembly, lamination and encapsulation, structuring of PDMS films and sustainable substrate materials for single use devices.

Voltera
Alroy Almeida
CEO & Co Founder

Print Anything on Everything: Unlocking Additive Electronics for the World
Electronics has lived in a subtractive world for a really long time. But the future is additive. Let’s take a look at how the industry — and the world — will evolve with the help of additive manufacturing and prototyping methods. Soft, biocompatible, textile and wearable electronics. In-mold structural electronics. It’s a brave new world and we won’t get there unless we break out of our subtractive box — so let’s take a look at how we do that. Explore the possibilities! Print anything. On everything.

Wuerth Elektronik eiSos
Christoph Voelcker
Team Leader

Advanced Electronics – to enable a sustainable future.
How to fuse established processes and disruptive technologies. Insights from an industrial point of view.
The presentation will highlight market potentials for advanced electronics and how to use them sensibly. What steps can the industry take to enable and interact with the rapid development to pave the path to a more sustainable future with disruptive technologies.
With a focus on the transfer of innovative projects, the presentation will show examples of how Würth Elektronik eiSos works with start-ups, technology and research projects.

XTPL
Lukasz Kosior
Business Development Manager
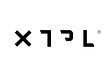
XTPL Ultraprecise Deposition Technology for Advanced Printed µElectronics Applications
The Ultraprecise Deposition (UPD) technology is a novel additive manufacturing technique for advanced Printed µElectronics applications. UPD can be used for fabricating micrometer-size interconnections in microelectronic systems, as well as for making redistribution layers on chips and filing vias in semiconductor devices.
UPD may be considered as a much-needed intermediary approach between printing of 2D planar structures and free-standing 3D architectures. This technology gives the ability to print metallic structures at micrometer scale on complex substrates, so that the printed features map the topography of the substrate. The UPD approach is based on a direct extrusion of highly-concentrated silver paste using a printing nozzle with the diameter in the range from 0.5 to 10 𝜇m. This defines the unique operating range for the UPD technology, compared to other printed electronics techniques: the combination of high-viscosity pastes and fine printed features. The process itself is governed by pressure, but the possibility to extrude such high-viscosity materials using such narrow nozzles is possible thanks to the simultaneous optimization of the paste, parameters of the process, as well as the printing nozzle (both in terms of the geometry and material properties).
The key advantage of using the high-viscosity pastes is that the printed structures preserve their shape regardless of the wetting properties of the substrates. Therefore, the design of a metallization scheme is not constrained by the surface properties. The printed feature size can be in the range from 1 to 10 𝜇m and the printing resolution (i.e., the distance between the printed structures) can be even below 1 𝜇m.
The structures can be printed on complex substrates, including substrates with pre-existing features (like steps), substrates with different surface properties, as well as flexible substrates. The resulting printed structures can be bent and are uniform regardless of the wetting properties of the substrates. Therefore, it is possible to print on materials like oxides (e.g., SiO2), nitrides (e.g., SiNx), metals, glass, and foils (e.g., PI, Kapton), as well as to print on junctions (metal/semiconductor/insulator).