TechBlick’s event on 29-30 March 2023 focuses on all additive technologies used and/or suited to prototyping and manufacturing of semiconductor packaging - from sub-micro to macro scale - from low-frequency to mmWave - from 2D to 2.5D and 3D.
Additive electronics can not only replace subtractive processes based on cost and green credentials but can also enable truly novel designs, components, and manufacturing processes in semiconductor packaging and PCBs.
In this unique conference - colocated online with TechBlick’s event “Digital & 3D Additive Manufacturing of Electronics, Displays, Photovoltaics, and Beyond” - you will learn about all the key additive electronics technology - both mature and emerging ones and both prototyping and manufacturing ready ones - being developed and/or deployed for various use cases in the semiconductor packaging and PCBs industries
The applications covered are numerous covering EMI shielding, HTCC/LTCC printing, wirebond replacement, solder mask, on-demand PCB production, 2.5-3D circuits, novel component geometries and designs, mmWave and 5G circuits, etching masks, post-production repair, multi-layer interpose development and beyond.

Aix-Marseille Université
Pol Sopena Martinez
Postdoc Fellow

Laser-induced forward transfer: Improved versatility for printed electronics applications
Over the last decades, printed electronics has gained importance as a cost-effective alternative to silicon-based electronics. Capitalizing on the conventional techniques from the graphics industry has allowed printing all the required materials (including metals, polymers, dielectrics, or ceramics) necessary to produce functional components and devices. Among them, direct-write techniques such as inkjet printing are particularly interesting since they allow printing inks on-demand directly from a digital file without the need for expensive pre-fabricated stencils or masks. However, high-viscosity inks, or those containing large particles in suspension, result in clogging of the nozzle output, which limits the range of printable materials. Alternatively, laser-induced forward transfer (LIFT), a more recently developed digital printing technique, has barely any of these constraints.
LIFT is a digital method for printing almost all kinds of inks regardless of their rheology. In LIFT, a thin layer of ink containing the desired functional material is extended on a donor substrate, which is placed facing the receiver substrate at a certain gap. Then, a laser pulse focused on the donor film induces a cavitation bubble that propels the material forward, which results in the material finally being deposited on the receiver substrate. The lack of nozzle in LIFT allows printing inks featuring low and high viscosities (0.001-100 Pa·s) and particles up to several tens of micrometers.
In this presentation, we explore the versatility of LIFT as a printing technique for printed electronics applications. Special attention is devoted to the transfer of conductive pads to be used as interconnects, the fundamental component in electronic devices. In particular, to demonstrate the potential of LIFT, we put into perspective three different cases. First, the LIFT of silver nanowire inks for producing transparent electrodes. Second, the LIFT of high solid content silver screen printing ink to be used as low-resistivity interconnects on regular paper. These two inks are particularly interesting since their rheology makes them unprintable using other digital printing techniques like inkjet. And, third, a striking concept consisting of the LIFT of a silver nanoparticle ink with continuous-wave laser radiation. In each one of these studies, the capabilities of LIFT with printed electronics applications are demonstrated by printing functional components and devices.

Celanese Micromax Microcircuit and Component Materials
Hee Hyun Lee
Micromax™ Senior R&D Scientist

Designing Ink-Jet and Nozzle Dispensable conductive/dielectric Inks for electronic applications
Additive printing technology has evolved to realize functional electric pattern on various type of substrates and form factor to create novel electronic device. While there is a broad range of Polymer Thick Film (PTF) inks for additive technologies including ink-jet, micro-dispensing and screen printing, choice of material depends on not just printing method but applications. In this presentation, we will discuss a ink-jet printable conductive ink and micro-dispensable polyimide series inks by introducing their technical features and potential applications.

Centre de Transfert de Technologies Ceramiques
Elodie Pereira
R&D Project Manager

Digital printing for ceramic based electronics
While the uses of ceramics in electronic devices are multiple, the manufacturing processes are also varied. Whereas conventional and strong processes are still used and need many steps, digital printing processes that emerged can path the way to new 3D complex shapes as well as reducing the number of steps.
Two additive manufacturing processes for substrates fabrication are especially interesting: laser stereolithography (SLA) and robocasting. SLA is a process based on the photopolymerization, by mean of a UV source, lighted on a liquid or paste surface. Usually, the liquid or paste contains a photopolymerizable resin loaded with ceramic particles. Starting from a CAD file, the ceramic pieces are produced layer by layer to obtain the green body of the piece. Starting from a CAD file as well, robocasting method is based on the extrusion of a filament trough a nozzle. The material filament can be obtain from a high viscous paste charged with ceramic fillers or else a thermoplastic filament heated to reach a semi-liquid state. At this stage the material is extruded and deposited into thin layers. Both green parts obtained by SLA and robocasting process need post-printing steps: debinding and sintering.
Once ceramic substrates are produced it is necessary to make them functional. The functionalization means the deposition of metallic traces and lots of processes can be used to do so. The presentation will focus on disruptive technologies like Aerosol Jet Printing (AJP) or micro-dispensing. AJP is a well-known conformal printing method where an aerosol is generated from a low viscous ink. The aerosol is then carried to the nozzle where it is concentrated by mean of an auxiliary gas. The AJP process produces high resolute lines with very low thickness. Micro-dispensing process may then appear to be complementary to AJP. Indeed, this process produces thick lines with higher current carrying capability. Micro-dispensing is a process using positive pressure on the ink that is transferred to a nozzle with a small aperture diameter. While AJP is a non-contact process, micro-dispensing is a different approach where the ink needs to be in permanent contact with substrate to be correctly deposited. Antennas, strain gauge or passive components can therefore be manufactured.
From those different digital technologies, one idea can emerge: their hybridization.

Domicro
Aart-Jan Hoeven
Business Development Manager.
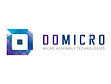
Inkjet Printing For Applications With Small Feature Sizes
The technology for integrating dies is an important enabler for the realization of thin applications in flexible hybrid electronics (FHE). Market needs are in making applications with ever smaller feature sizes. Therefore, we have developed an approach for micro assembly of thin and compact devices using interconnections made with inkjet printing.
Challenges for the realization of advanced applications are in the seamless and invisible integration of multiple components, such as ICs, passive components, sensors and LEDs, in an ever smaller space. There is a market need for making thinner devices, for example for applications in in-mold electronics or smart glass. There also is a need to make devices with smaller lateral dimensions for enabling the integration of more complex components. For example, for offering more advanced functionalities more advanced components will be needed. Such components typically have a larger number of interconnections at a finer pitch, which causes a need for thinner interconnections.
We have investigated how the processes for micro assembly with inkjet printed interconnections, used like wirebonds, can be optimized for realizing a scale reduction. With the integration of ultra-thin bare dies, demonstrators could be made with a total heights down to 0.1 mm. The presentation will share the highlights from this investigation, with a perspective on the opportunities that can be realized using the results from this work.

Dracula Technologies
Florence Archet
R&D Manager
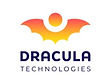
Inkjet Printed Flexible and Free Design OPV Modules for Indoor Application
Inkjet printing is a unique coating and printing technique. Fully digital, it allows to print design with a large variety of shape and dimensions. Drop on Demand technology induces low material waste. Moreover, it presents the advantage to be maskless and contactless allowing to avoid any contamination during the deposition of the thin layers. Thus, it caught the printed electronic community attention and more especially the one of the Organic Photovoltaic (OPV) field. In this context and due to the mechanical flexibility, light weight, aesthetics, absorption tunability and environmental friendliness, OPV have superior application potential over their inorganic and hybrid counterparts. In 2004, V. Shah et al. printed the first OPV active layer by inkjet printing. Although the power conversion efficiency is very low (< 0,1%)1 this is the first proof of concept of the feasibility to use inkjet printing for OPV fabrication. The first efficient active layer printed by inkjet printing is made three years later2 and the first OPV fully printed by inkjet printing is obtained only in 20143,4.
To achieve efficient inkjet printed indoor OPV cells and modules, we show that each OPV layer must be carefully optimized, and several key parameters should be finely tuned. However, inkjet printed devices are often made at laboratory scale with small printers and halogenated solvents. To be competitive at industrial scale, OPV modules should be made in air from green solvents with large scale printhead. Herein we demonstrate the challenge to go from academic lab-scale (spin-coating under inert atmosphere, small cell) to industrial scale (inkjet printing in
air, modules).
To prove the great advantage of inkjet printing as a digital technology allowing freedom of forms and designs, OPV modules with different artistic shapes are demonstrated keeping high performance under indoor conditions and allowing better integration into IoT Products. Reported results confirm that inkjet printing has high potential for the processing of indoor OPV, allowing quick changes in design as well as in materials.

ETSMTL
Sylvain G Cloutier
Professor and Chair

Inkjet-Printed Materials and Flexible Hybrid Electronic (FHE) Devices
This TechBlick presentation will discuss new inkjet-printable optoelectronic materials and their integration into all-printed devices. We will also show how deep-learning can be used to improve the capabilities of low-cost printed devices. Finally, we will discuss recent breakthrough with the hybrid integration of packaged components and copper-based flexible circuits, which was recently achieved with our partners at C2MI.

Elephantech
Masaaki Sugimoto
Co Founder/SVP
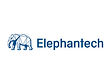
Inkjet-Printed PCBs, a paradigm shift to a needs-driven approach to decarbonization
Elephantech, a printed electronics firm using inkjet technology founded in 2014, began producing flexible printed circuits (FPCs) using additive manufacturing in 2018 and has since then established a large-scale demonstration plant for mass production in 2020. Due to the recent COP26 conference, there is a growing demand from eco-conscious customers for the new manufacturing method, as they recognize its equivalence in performance to conventional products and superior environmental impact. To meet this expectation, Elephantech is focusing future research and development efforts on the scaling of single-sided FPC production, as well as the development of double-sided FPCs and double-sided rigid printed circuit boards, and will provide updates on these endeavors.

Essemtec AG
Irving Rodriguez




Novel automatic repair of populated PCBs in a cost-effective and adaptive way
Repair of soldered components is a constant necessity in the electronics industry. Product performance enhancement, damaged components, and exchange of wrong placed components are some of the motivations behind a repair. Dispensing and placing a 400 µm pitch component manually is very time consuming and could cause collateral damage to the already populated components. A novel automatic repair method and tools with no human interaction were developed. This method uses the advantages of solder jetting and pick and place in one instrument, making it extremely accurate, reliable, and cost-effective. The use of different alloys including low-temperature soldering (LTS) is feasible. The results show that this technique significantly improves the throughput of the repaired devices.

FTMC
Karolis Ratautas
Researcher




Selective Surface Activation Induced by Laser (SSAIL) – technology of electric circuit formation on various 3D dielectric surfaces
Electric circuit traces formation on 3D-shaped dielectrics is one of the highest challenges in 3D Mechatronic Integrated Devices (3D-MID). The advanced technology of Selective Surface Activation Induced by a Laser (SSAIL) can solve emerged production issues for electric traces. SSAIL contains three main steps: laser modification of the dielectric surface, chemical activation of modified areas and electroless plating of activated parts. Ultrashort pulse laser-induced physical and chemical bonding between dielectric substrate material and plated metal guaranty strong adhesion. The process could be applied almost on any dielectric by adapting laser and chemical parameters. No additives are required into base materialand, therefore, polymers, ceramics, glases, composites or even semiconductors can be used as a substrate. Conductive lines as narrow as 1 micrometer can be fabricated using special beam shaping techniques. High diversity of substrate materials and capability of narrow trace formation extends technology application from standard 3D MID to transparent conductive electrodes.

FUJI CORPORATION
Ryojiro Tominaga
Development Center Engineering Department
Section manager

Digital manufacturing of 3D electronics with low temperature SMT
Additive manufacturing driven by digital 3D data is effective approach to make unique shape electrical device.
It also can contribute to accelerate PoC and minimize the production waste.
In the session, we’ll introduce our process technics to realize full additive digital manufacturing of electronics.
Especially, we will focus on the low temperature SMT.

Fraunhofer ENAS
Prof. Ralf Zichner
Manager Printed Functionalities
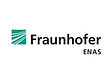
Robot-guided inkjet printing for the production of printed electronics on arbitrary 3D components
The industrial demand for individualized (quantity 1) functionalization of components and devices is increasing. This is why technological alternatives are emerging in order to outweigh the drawbacks of existing and time-consuming production technologies such as molded interconnect device technology (MID) or selective laser sintering (SLS). Robot-guided inkjet printing is particularly attractive in this regard. From a scientific point of view, printed electronics (sensor systems, heaters, conductors, antennas) on 3D devices and components is a particularly promising surface functionalization and highly sought after by industry. The presentation will include current research results as well as selected application examples and demonstrators.

Fraunhofer IAP
Manuel Gensler
Chemist

High Resolution EHDJET Printing of PEDOT:PSS for Display Applications
PEDOT:PSS is a versatile organic semiconductor used in a variety of organic-electronic applications such as sensors, displays, MEMS, OTFT, OFETs and touch screens. Electrohydrodynamic jet (EHDJET) printing is an evolving digital printing technology breaking down the resolution limits of Inkjet. This technology makes use of pulsed voltages in the kV-range instead of piezo actuation to eject jets from a fine nozzle. Directed by the electric field, ink volumes in the femtoliter range are printable without getting deflected by the air or inert gas environment. Feature sizes well below 10 µm are printable in bitmap or vector mode, such as single droplets or continuous lines. Highly conductive inks such as PEDOT:PSS or silver are especially reactive to the electric field, but challenging to print onto conductive or semiconducting surfaces such as pixel electrodes or ITO glass when grounded. Electric discharging prevents from stable printing as soon as the jet connects nozzle and substrate. In this talk, we will present an approach for stable printing of PEDOT:PSS as hole-transport-layer into pixel defining structures for fully printed OLED and QD-LED display applications.

Fraunhofer IKTS
Prashantkumar Pandey
Researcher | PhD Scholar

Additively printed hybrid ceramic components for microsystem applications
Ceramics are one of the more difficult materials to fabricate into complex morphologies and are challenging to employ. Low or High Temperature Co-fired Ceramics (LTCC/HTCC) have a wide range of applications in different fields of electronics and microsystem applications. LTCC/HTCC devices are manufactured by applying conductive, dielectric, and resistive metal pastes on each ceramic substrate sheet or tape as needed and then pressed together in a specified sequence, laminating them together. This ceramic sheet of printed metal is then fired or sintered which takes place at temperature below 1000°C for LTCC and above 1000°C for HTCC. The resulting package is a multilayer, three-dimensional design that is considerably more compact than a traditional planar microsystems component.
The multilayer-ceramic technology offers exceptional capabilities for the manufacturing of packages, printed circuit boards, and microsystems. The ceramic multilayer technology (e.g. LTCC/HTCC) even enhances these advantages because of its ability (i) for a complex 3D miniaturization with embedded deformable bodies (cantilever, diaphragms), channels and cavities as well as (ii) for the realization of hybrid components with integrated dielectric, conducting, magnetic, piezoelectric and sensorial materials, being (iii) very robust against environmental stress, and providing (iv) outstanding high-frequency qualities (εR, tan δ) in combination with a very good thermomechanical adaptation to typical semiconductors..
A cost-effective solution for producing small quantities and individualized products economically is to employ digital printing technologies like inkjet or aerosol jet. These printing techniques are maskless and are entirely additive, making them incredibly adaptable. The combination of both printing technologies enables large-area and simultaneously precise structuring of multilayer ceramics on the one hand, and the creation of three-dimensional structures on the other. These deposition techniques together with co-printing and co-firing possibility further enables the integration of further passive components such as resistors, coils and capacitors, which enables complete sensor systems and packaging in a very compact design and fast development time.
A special feature are the dielectric ceramic inks based on LTCC, which replace conventional ceramic green films. This increases the flexibility of the manufacturing process, the geometric degree of freedom and the achievable integration density.

Grenoble INP-Pagora
Davide Beneventi
LGP2, CNRS Research Director
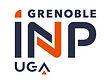
Rapid prototyping of 3D electronics using direct ink writing and 6-axis robots
Over the last decade the integration of printed electronic boards and conductive paths on the surface of 3D structural parts triggered an ever-increasing interest and new manufacturing processes such as Lased Direct Structuring (LDS) and 2-shots molding (2SM) have been developed. More recently, direct ink writing using poly-articulated robots has been proposed as an alternative process to overcome the intrinsic limitations of LDS and 2SM (i.e. the use of specific materials and processes for both substrate and circuits) since it unlocks the combined use of commercial electronic inks, conventional digital printing technologies and generic 3D plastic substrates. The aim of this presentation is to provide an overview of a rapid prototyping process recently developed in our Lab using piezo jetting and a 6-axis robot with a specific focus on the control of the printhead motion and the printing accuracy of conductive paths.

Humboldt-Universität zu Berlin -
Felix Hermerschmidt
Postdoctoral Researcher
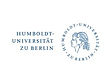
Combinatorically Inkjet-Printed Metal Halide Perovskite Optoelectronic Devices
Beyond the use in home and office-based printers, inkjet printing has become a popular structuring and selective deposition technique in industry. Metal halide perovskites (MHP) have received great attention in recent years, predominantly due to the high performance of perovskite solar cells. Yet, the versatility of this material class has also allowed its use in light-emitting diodes and photo detectors. In all these device applications the tunability of the energy bandgap is of particular importance. In this contribution we will show the fabrication of combinatorically printed photodetector arrays, large area multi color light emitting devices, as well as inkjet printed solar cells.

J.A.M.E.S GmbH
Alexandre Schaefer
Business Development Manager

Accelerating the development of AME
Additively manufactured electronics (AME) is a very important but currently a small part of additively manufacturing itself. The main questions are: how can we come to a more exponential growth in the AME market within the next years and how can we unlock a higher volume earlier for all of us? I will show what is possible today with this technology and where it can go to. And I will provide a possible solution to accelerate the AME market development.

Nanyang Technological University
Guo Liang
Ph.D. | Researcher
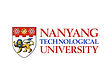
Digital manufacturing for mass customization of printed electronics using aerosol jet printing technology
Printed electronics is a rapidly growing field, and new technologies and materials are constantly being developed to enable low-cost, high-volume production of electronic devices. One such promising technology is aerosol jet printing, which has the capability to significantly change the way printed electronics are manufactured. The main advantage of aerosol jet printing is its ability to enable mass customization of printed electronics through precise control of material deposition. This results in the creation of functional and complex electronic devices with high precision.
Aerosol jet printing has a wide range of applications, including flexible sensors, wearable devices, and medical implants. The technology works by using a high-speed stream of charged particles to deposit materials onto a substrate, allowing for the creation of complex structures with high resolution and reproducibility. This makes it ideal for mass customization of printed electronics.
In this talk, the current state of digital manufacturing for printed electronics using aerosol jet printing technology will be reviewed. The advantages and challenges of this approach, as well as the opportunities for future development in this rapidly growing field will be examined. Through a comprehensive analysis of the latest research, we will gain a deeper understanding of the potential of aerosol jet printing for the mass customization of printed electronics and its impact on the wider field of electronics manufacturing.

North Carolina State University
Jingyan Dong
Professor



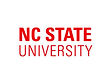
Direct EHD Printing of VIA Interconnects towards Multi-Layer Flexible and Stretchable Electronics
Direct printing of flexible and stretchable conductors provides a low-cost mask-less approach for the fabrication of next generation electronics. In this work, an electrohydrodynamic (EHD) printing technology was studied for low-melting-point metal alloys that are hard to be printed with traditional print methods. We successfully achieved high-resolution printing of these materials, which enables low-cost direct fabrication of high performance electronics with sub-50μm resolution. The EHD printed microscale metallic patterns represent a promising way to create circuits and VIA interconnects with metallic conductivity and excellent flexibility and stretchability. A stable electrical response was achieved after hundreds of bending cycles and during stretching/releasing cycles in a large range of tensile strain for the printed conductors with properly designed patterns. When using low-melting-point metal alloys as functional inks, due to their low melting point, the printed conductor demonstrated excellent self-healing capability, which recovered from failure simply by heating the device above the eutectic temperature of the metal ink and applying slight pressure. A few device demonstrations, including multi-layer electronics, were fabricated to demonstrate the capability of the EHD printing for the direction fabrication of 3D flexible and stretchable devices.

Ntrium
Seyoung Jeong
CEO/Ph.D

Introduction to Mass-producible Component Level EMI Shielding Technology
Electromagnetic interference is one of the most critical problems that must be thoroughly solved to open the era of fully autonomous driving.
If individual electromagnetic wave shielding is applied to thousands of semiconductors and tens of thousands of elements per car,
electromagnetic interference can be dramatically prevented.
This presentation introduces component level EMI shielding materials and processtechnologies and products

SAULE Technologies
German Soto
Materials science specialist

Update on the technology progress of printed perovskite PV
Metal halide perovskites in the last decade emerged as a new class of materials for highly efficient solar cells, with the power conversion efficiency reaching up to 25.7%. Perovskite photoactive materials offer inherent advantages leading to high power conversion efficiencies, such as long carrier diffusion lengths, high carrier mobilities, low exciton binding energies, high absorption coefficients and band gap tunability via interchanges of the precursor components. An important benefit of these materials is the possibility to deposit its thin films via solution-based processing at low temperatures. The use of plastic foils also opens the possibility for a PV product to offer a range of new value propositions, where non cost-related factors can provide an important leverage, such as light weight, high specific power, or ease of integration with various surfaces. The presentation will review the advancements in this rapidly developing field, and Saule's approach to turn it into a commercially viable product.

Seoul National University
Yongtaek Hong
Professor
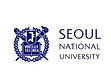
Maskless patterning of electrodes for 3D deformable and stretchable electronics applications
Recently in-mold or 3D deformable electronics and stretchable electronics areas have gained a lot of attention from academia and industry for sensor, bio, energy and display applications. Most of high-end, close-to-commercialization technologies are based on using conventional mask-based patterning methods on a flexible but not stretchable plastic substrate and reforming the final flexible device so that it can be stretched or 3D deformed. However, in order to make final working device directly on either a stretchable or 3D deformable substrates, a new maskless patterning method must be used. The direct maskless patterning will have a significant benefit if it is easy to use and it can be universally applied to various conductive materials.
In this talk, I will show you our group's efforts developing maskless pattering methods for solution-process AgNW and other various vacuum deposited electrodes for potential usage in stretchable or 3D deformable electronics application.

Syenta
Jekaterina Viktorova
CEO and Co-Founder

Electrochemical Printing of Multi-Material Electronics.
Syenta is excited to introduce its patented fabrication method for multi-material 3D printing using electrochemistry for the first time. Our method combines electrochemical with three-dimensional control of electrode positions to culminate in a new process for 2D patterning and 3D printing of metals, semiconducting materials as well as polymers into complex shapes with feature sizes as low as 10 mm. Our method does not rely on nanoparticles and therefore does not need post-treatment and allows for nearly bulk material properties and conductivity of copper up to 82% that of bulk metal.
In this talk we will showcase the capabilities of our method, focusing on speed, resolution, and material quality, as well as some of the printed electronic applications for our printer.

TCL Corporate Research
Longjia Wu
Materials Development Expert/ Lead R&D Manager

The Development of IJP-QLED Display towards its Commercialization
Quantum dots light emitting diodes(QLEDs), have been widely recognized as the most promising next-generation display technology candidate. At current stage, the lifetime issue of QLEDs remains the critical challange towards commercialization, especially for blue devices. For mass-production of QLEDs, other issues need to be addressed including device structure compatible for production and improvement in the Ink-Jet-Printed(IJP) device performances.
To solve these issues, TCL QLED team has made significant progress in the development of high-performance QLED devices.The lifetime performance of QLED devices were able to be competitive with that of OLEDs. We have successfully adopted the top emission device structure, which is compatible for panel mass-production with better current efficiency. Furthermore, the performance gap between spin-coated and IJP devices has been largely resolved, owing to the effort on the optimization of inks, film quality and IJP fabrication flow. Such progress is expected to shed light on the dawn of QLED commercialization.

University Paris Cité
Vincent Noel
Professor & Director of the Printup Institute (CEO)




Perspectives and Pitfalls of Inkjet-Printed Electronics: A Chemist's Point of View
Printed electronics is experiencing considerable growth due to the ability of inkjet printing methods to integrate functional (bio)materials under ambient conditions. The trend is to manufacture connected devices using "all-print" methods. To meet this demand, printed electronics must make several advances. On the one hand, it is necessary to move from printing mainly metallic inks (temperature and pressure sensors, RFID antennas...) to printing inks with very high added value (e.g. biosensing functions, energy supply....). On the other hand, to achieve competitive analytical performances, the spatial resolution of the printed patterns must be optimized by several orders of magnitude to reach sub-micrometer scales.1
To satisfy this dual need, we are developing original approaches for surface functionalization by and for inkjet printing with electron-aytical targets. One of these approaches consists in formulating reactive inks composed of molecular structures able to covalently bind to the surface of a substrate and thus modulate its local wettability characteristics. Another major approach consists in printing suspensions of functionalized nanoparticles able to induce nanostructures by self-assembly on the substrate surface during the evaporation of the solvents constituting the ink. These two approaches will be illustrated through examples of realization in order to underline their relevance and to establish the scientific and technological barriers associated with the functionalization of surface by high resolution printing methods.

XTPL S.A.
Łukasz Kosior
Business Development Manager
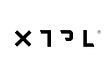
High resolution printing of functional materials for advanced high density 3D interconnections.
XTPL is a supplier of micron-scale, additive fabrication technology and conductive materials to solve complex challenges in the advanced electronics industry.
The company’s proprietary solutions enable ultra-precise printing of micron-sized functional features with high resolution. This is possible on planar and non-planar complex substrates, including printing continuous highly conductive interconnections over the steps.
During the presentation we will focus on application in high density interconnections (< 10 µm Line/Space) used in Advanced IC Packaging and Flexible Hybrid Electronics (FHE) as a great alternative to traditional wire bonding approach.